PVC(Polyvinyl chloride) foam core material and production process thereof
A foam core material and production process technology, applied in the field of foam materials, can solve the problems of product quality to be improved and low foam yield, and achieve the effects of high yield, low density, and simple production process
- Summary
- Abstract
- Description
- Claims
- Application Information
AI Technical Summary
Problems solved by technology
Method used
Image
Examples
Embodiment 1
[0054] The embodiment of the present invention provides a kind of PVC foam core material, and it adopts following production process to make:
[0055] S101 Prepare raw materials: 50kg PVC, 31.9kg 1,5-naphthalene diisocyanate, 5.1kg AIBN, 2kg AC, 1kg epoxy resin, 8kg succinic anhydride, and 2kg chitosan.
[0056] S102 Mixing: Pour the raw materials except PVC into a planetary mixer for premixing, first mix at 50rpm for 25min, use a homogenizing pump for 2min, then mix at 50rpm for 20min, homogenize for 2min, and then mix at 35rpm 10 minutes, homogenization for 2 minutes, the temperature during premixing is not higher than 30°C, and the premixed material is obtained. Add PVC to the premix, and mix at 35 rpm for 15 minutes under the condition of vacuum ≤ -0.09MPa, and the temperature during main mixing is not higher than 35°C to obtain a pasty mixture.
[0057] S103 Molding: Inject the paste mixture into the mold, cover with a layer of PET film, and then send it to a 1500T multi...
Embodiment 2
[0061] The embodiment of the present invention provides a kind of PVC foam core material, and it adopts following production process to make:
[0062] S201 Prepare raw materials: 60kg PVC, 26.2kg toluene diisocyanate, 4kg AIBN, 2kg AC, 0.6kg epoxy soybean oil, 6.2kg methyl hexahydrophthalic anhydride, and 1kg chitin.
[0063] S202 Mixing: Pour the raw materials other than PVC into a planetary mixer for premixing, mix at 60rpm for 5min, use a homogenizing pump for 3min, and cycle 5 times according to the above process. The temperature during premixing should not be higher than 30°C to obtain a premix. Add PVC to the premix, and mix at 50 rpm for 30 minutes under the condition of vacuum ≤ -0.09MPa, and the temperature during main mixing is not higher than 35°C to obtain a pasty mixture.
[0064] S203 Molding: Inject the pasty mixture into the mold, cover with a layer of PET film, and then send it to the 1500T multi-layer press system for molding. First, the temperature is raise...
Embodiment 3
[0068] The embodiment of the present invention provides a kind of PVC foam core material, and it adopts following production process to make:
[0069] S301 Prepared raw materials: 40kg PVC, 36.5kg carbodiimide modified isocyanate, 7kgAIBN, 3kgAC, 1.5kg epoxy triglyceride, 10kg pyromellitic dianhydride, 2kg alkaloid, 1kg polyethyleneimine (accounting for the remaining raw materials 1% of the total amount).
[0070] S302 Mixing: Pour the raw materials except PVC into a planetary mixer for premixing, first mix at 30rpm for 4min, homogenize for 5min, then mix at 40rpm for 5min, homogenize for 6min, then mix at 50rpm for 6min, homogenize 7min, the temperature during premixing is not higher than 30°C, and the premixed material is obtained. Add PVC to the premix, carry out main mixing, mix at 50 rpm for 30 minutes, the temperature during main mixing is not higher than 35°C, and obtain a pasty mixture.
[0071] S303 molding: inject the paste mixture into the mold, cover with a layer...
PUM
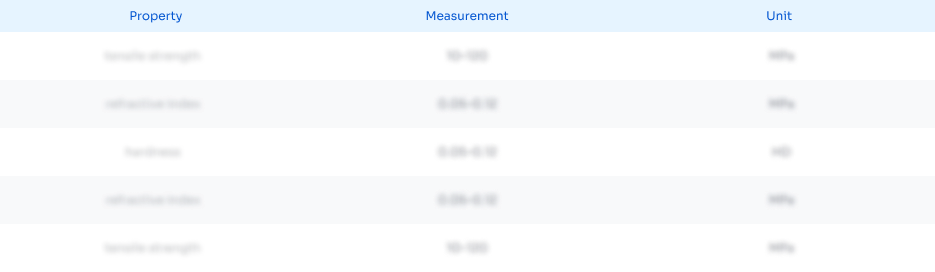
Abstract
Description
Claims
Application Information

- Generate Ideas
- Intellectual Property
- Life Sciences
- Materials
- Tech Scout
- Unparalleled Data Quality
- Higher Quality Content
- 60% Fewer Hallucinations
Browse by: Latest US Patents, China's latest patents, Technical Efficacy Thesaurus, Application Domain, Technology Topic, Popular Technical Reports.
© 2025 PatSnap. All rights reserved.Legal|Privacy policy|Modern Slavery Act Transparency Statement|Sitemap|About US| Contact US: help@patsnap.com