Low-grade magnesite pulp preparing system and method for flotation
A preparation system and magnesite technology, applied in grain processing, etc., can solve the problems of high infrastructure investment, low stand-alone production capacity, affecting operation and operation, etc., and achieve the effect of reduced infrastructure investment, high degree of automation, and reduced labor costs
- Summary
- Abstract
- Description
- Claims
- Application Information
AI Technical Summary
Problems solved by technology
Method used
Image
Examples
Embodiment 1
[0034] figure 1 A schematic structural diagram of a low-grade magnesite slurry preparation system for flotation is provided, the preparation system includes a grinding machine 1, a dust collector 4, a stirring tank 5 and a storage tank 7, and the outlet of the grinding machine 1 is connected to The feed port of the dust collector 4, the discharge port of the dust collector 4 is connected to the feed port of the stirring tank 5, and the discharge port of the stirring tank 5 is connected to the feed port of the storage tank 7 through the slurry pump 6, so The water inlet of the mixing tank 5 is connected to the water interface. Among them, the grinding machine is a vertical mill.
[0035] A method for preparing low-grade magnesite slurry for flotation is to adopt such as figure 1 The shown preparation system comprises the following steps:
[0036] (1) Grinding: feed the magnesite raw material into the grinding machine and grind it to a particle size of ≤74μm;
[0037] (2) Du...
Embodiment 2
[0042] figure 2 A schematic structural diagram of a low-grade magnesite slurry preparation system for flotation is provided, the preparation system includes a grinding machine 1, a powder separator 3, a dust collector 4, a stirring tank 5 and a storage tank 7, and the grinding machine 1. The discharge port is connected to the powder separator 3 feed port through the conveyor 2. The powder selector 3 discharge port is connected to the dust collector 4 feed port. The fine powder outlet 3-2 of the powder separator and the coarse powder The outlet 3-1 is respectively connected to the feeding port of the stirring tank 5 and the feeding port of the grinding machine 1, the outlet of the dust collector 4 is connected to the feeding port of the stirring tank 5, and the discharging port of the stirring tank 5 is The port is connected to the storage tank 7 feed port through the slurry pump 6, and the stirring tank 5 water inlet is connected to the water interface; the connecting pipe be...
Embodiment 3
[0051] figure 2 A schematic structural diagram of a low-grade magnesite slurry preparation system for flotation is provided, the preparation system includes a grinding machine 1, a powder separator 3, a dust collector 4, a stirring tank 5 and a storage tank 7, and the grinding machine 1. The discharge port is connected to the powder separator 3 feed port through the conveyor 2. The powder selector 3 discharge port is connected to the dust collector 4 feed port. The fine powder outlet 3-2 of the powder separator and the coarse powder The outlet 3-1 is respectively connected to the feeding port of the stirring tank 5 and the feeding port of the grinding machine 1, the outlet of the dust collector 4 is connected to the feeding port of the stirring tank 5, and the discharging port of the stirring tank 5 is The port is connected to the storage tank 7 feed port through the slurry pump 6, and the stirring tank 5 water inlet is connected to the water interface; the connecting pipe be...
PUM
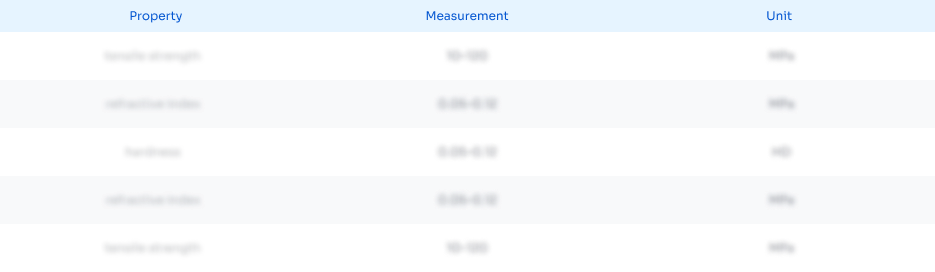
Abstract
Description
Claims
Application Information

- R&D Engineer
- R&D Manager
- IP Professional
- Industry Leading Data Capabilities
- Powerful AI technology
- Patent DNA Extraction
Browse by: Latest US Patents, China's latest patents, Technical Efficacy Thesaurus, Application Domain, Technology Topic, Popular Technical Reports.
© 2024 PatSnap. All rights reserved.Legal|Privacy policy|Modern Slavery Act Transparency Statement|Sitemap|About US| Contact US: help@patsnap.com