Steering-by-wire system test bench
A technology of test bench and steer-by-wire, which is applied in the direction of vehicle steering/bumping performance, etc. It can solve the problems of low bearing capacity of ball screw, abrupt change of jump, slow transmission speed, etc., and achieve the effect of simple and effective construction method
- Summary
- Abstract
- Description
- Claims
- Application Information
AI Technical Summary
Problems solved by technology
Method used
Image
Examples
Embodiment Construction
[0023] The present invention will be further described below with reference to the drawings.
[0024] A tension pressure sensor 13 and a linear displacement sensor 12 are installed on the steering rod. These two sensors reflect the road surface conditions in real time, and the road feeling information can be obtained. These information are converted into electrical signals and sent to the ECU in the main control module 6. According to the vehicle speed signal from the vehicle speed generator and the current signal fed back from the road sensor motor 4, the ECU calculates the road sensor motor PWM signal through an algorithm, and uses the Flexray bus 15 to transmit the PWM signal to control the rotation direction and output torque of the road sensor motor Size to complete the real-time control of the road sense motor.
[0025] The torque sensor 3 and the rotation angle sensor 2 are mounted on the steering shaft, and the steering motor 14 and the resistance simulation motor 10 are co...
PUM
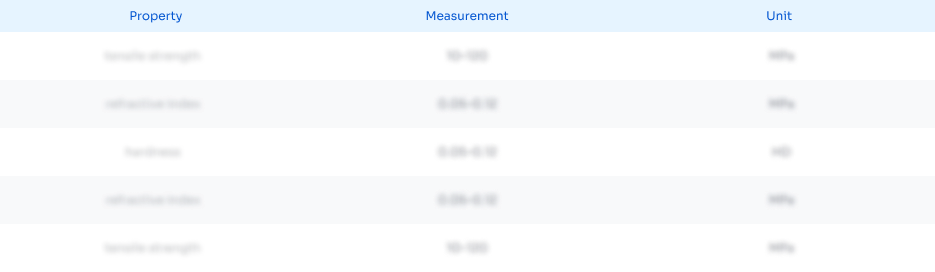
Abstract
Description
Claims
Application Information

- R&D Engineer
- R&D Manager
- IP Professional
- Industry Leading Data Capabilities
- Powerful AI technology
- Patent DNA Extraction
Browse by: Latest US Patents, China's latest patents, Technical Efficacy Thesaurus, Application Domain, Technology Topic, Popular Technical Reports.
© 2024 PatSnap. All rights reserved.Legal|Privacy policy|Modern Slavery Act Transparency Statement|Sitemap|About US| Contact US: help@patsnap.com