High-strength wear-resistant rubber material
A wear-resistant rubber, high-strength technology, applied in the field of rubber materials, can solve the problems of hard and brittle, poor wear resistance, easy aging and so on
- Summary
- Abstract
- Description
- Claims
- Application Information
AI Technical Summary
Problems solved by technology
Method used
Examples
Embodiment 1
[0016] A high-strength wear-resistant rubber material, its raw materials include by weight: 55 parts of epoxy natural rubber, 27 parts of EPDM, 18 parts of styrene-butadiene rubber, 12 parts of polyurethane elastomer, 1 part of carbon black N330, carbon black 6 parts of N660, 12 parts of modified reinforcing filler, 10 parts of light calcium, 22 parts of montmorillonite, 10 parts of polypropylene fiber, 5 parts of molybdenum disulfide, 3 parts of silane coupling agent, 3 parts of nano zinc oxide, accelerator 2.5 parts of DM, 1 part of accelerator TMTM, 2 parts of sulfur, 0.5 parts of anti-aging agent, 0.5 parts of anti-aging additive, 4 parts of trioctyl trimellitate, 4 parts of tributyl citrate, butyl epoxy soyate 3 copies;
[0017] Wherein, the preparation method of the modified reinforcing filler includes: adding 100 parts of multi-walled carbon nanotubes into concentrated nitric acid solution in parts by weight, ultrasonically treating at 40°C for 1h, then adding to a wate...
Embodiment 2
[0020]A high-strength wear-resistant rubber material, its raw materials include by weight: 75 parts of epoxy natural rubber, 15 parts of EPDM rubber, 32 parts of styrene-butadiene rubber, 6 parts of polyurethane elastomer, 3 parts of carbon black N330, carbon black 3 parts of N660, 20 parts of modified reinforcing filler, 4 parts of light calcium, 28 parts of montmorillonite, 3 parts of polypropylene fiber, 8 parts of molybdenum disulfide, 0.8 parts of silane coupling agent, 8 parts of nano zinc oxide, accelerator 1.5 parts of DM, 3 parts of accelerator TMTM, 0.2 parts of sulfur, 1.5 parts of anti-aging agent, 0.1 part of anti-aging additive, 8 parts of trioctyl trimellitate, 1 part of tributyl citrate, butyl epoxy soyate 5 copies;
[0021] Wherein, the preparation method of the modified reinforcing filler includes: adding 100 parts by weight of multi-walled carbon nanotubes into a mixed acid solution of concentrated nitric acid and concentrated sulfuric acid with a volume rat...
Embodiment 3
[0024] A kind of high-strength wear-resistant rubber material, its raw material comprises by weight: 60 parts of epoxy natural rubber, 24 parts of EPDM rubber, 22 parts of styrene-butadiene rubber, 10 parts of polyurethane elastomer, 1 part of carbon black N330, carbon black 5 parts of N660, 14 parts of modified reinforcing filler, 8 parts of light calcium, 24 parts of montmorillonite, 8 parts of polypropylene fiber, 6 parts of molybdenum disulfide, 2.4 parts of silane coupling agent, 5 parts of nano zinc oxide, accelerator 2.2 parts of DM, 1.5 parts of accelerator TMTM, 1.5 parts of sulfur, 0.8 parts of anti-aging agent, 0.4 parts of anti-aging additive, 5 parts of trioctyl trimellitate, 3 parts of tributyl citrate, butyl epoxy soyate 4 parts;
[0025] Wherein, the preparation method of the modified reinforcing filler includes: adding 100 parts by weight of multi-walled carbon nanotubes into a mixed acid solution of concentrated nitric acid and concentrated sulfuric acid with...
PUM
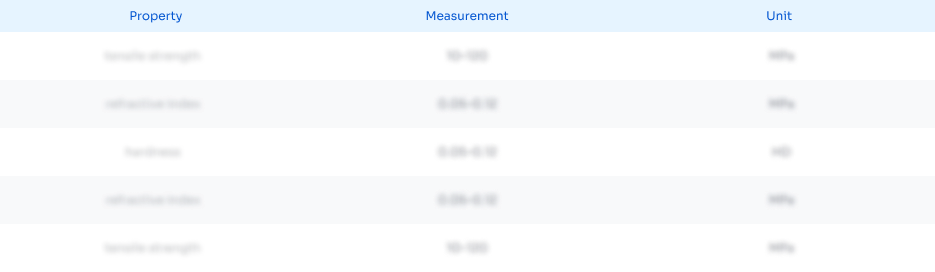
Abstract
Description
Claims
Application Information

- R&D Engineer
- R&D Manager
- IP Professional
- Industry Leading Data Capabilities
- Powerful AI technology
- Patent DNA Extraction
Browse by: Latest US Patents, China's latest patents, Technical Efficacy Thesaurus, Application Domain, Technology Topic, Popular Technical Reports.
© 2024 PatSnap. All rights reserved.Legal|Privacy policy|Modern Slavery Act Transparency Statement|Sitemap|About US| Contact US: help@patsnap.com