Sensorless control method of permanent magnet synchronous motor
A technology of permanent magnet synchronous motor and control method, applied in the direction of motor generator control, electronic commutation motor control, control system, etc., can solve the problems of low reliability, poor dynamic and static performance, complex algorithm, etc., to increase reliability , improve dynamic performance, low complexity effect
- Summary
- Abstract
- Description
- Claims
- Application Information
AI Technical Summary
Problems solved by technology
Method used
Image
Examples
Embodiment Construction
[0051] The specific implementation manners of the present invention will be described below in conjunction with the accompanying drawings.
[0052] figure 1 It is a flow chart of the method of the present invention, and it can be seen from the figure that the present invention includes the following steps.
[0053] Step 1 (S01), the signal generator generates a high-frequency voltage signal v h , and injected into the estimated In the shaft system, v h As shown in the following formula:
[0054] v h =V h sin(ω h t+π)
[0055] Among them, V h is the high-frequency voltage amplitude, ω h is the high-frequency voltage angular frequency, and t represents the signal injection time.
[0056] Step 2 (S02), according to the high-frequency voltage signal v injected in step 1 h , calculate the signal modulation array A m The dimension N, generate signal modulation array A m .
[0057] Step 3 (S03), the current sensor samples the stator winding current i a i b and i c ,...
PUM
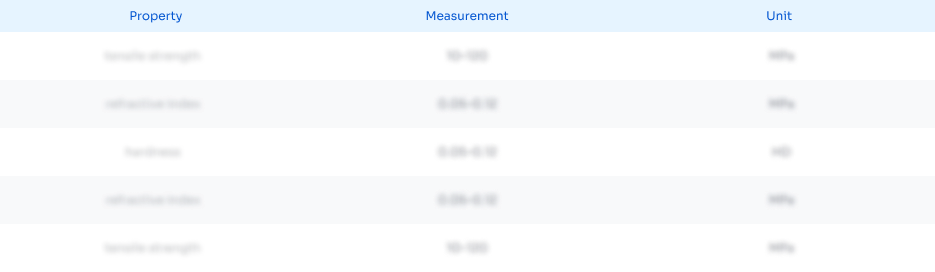
Abstract
Description
Claims
Application Information

- R&D
- Intellectual Property
- Life Sciences
- Materials
- Tech Scout
- Unparalleled Data Quality
- Higher Quality Content
- 60% Fewer Hallucinations
Browse by: Latest US Patents, China's latest patents, Technical Efficacy Thesaurus, Application Domain, Technology Topic, Popular Technical Reports.
© 2025 PatSnap. All rights reserved.Legal|Privacy policy|Modern Slavery Act Transparency Statement|Sitemap|About US| Contact US: help@patsnap.com