Fuse wire filled multifunctional controllable additive manufacturing device
A kind of additive manufacturing and multi-component technology, which is applied in the direction of manufacturing tools, electron beam welding equipment, metal processing equipment, etc., can solve the problems of unstable vacuum degree of vacuum chamber, increased manufacturing cost of vacuum chamber, and reduced protection safety factor. Achieve the effects of fast welding and cooling speed, improved fusion ratio, and small welding heat-affected zone
- Summary
- Abstract
- Description
- Claims
- Application Information
AI Technical Summary
Problems solved by technology
Method used
Image
Examples
Embodiment 1
[0032] Embodiment 1, select non-melting slag filling welding with particles, the specific implementation steps are as follows:
[0033] 1. Turn on the high-voltage power supply 6, start the vacuum preheating for 45 minutes, and fix the substrate required for additive manufacturing on the workbench;
[0034] 2. Place the metal particles required for filling in the material storage box 29, adjust the size of the valve 32 according to the size of the weld, and use the valve 32 to control the flow of the metal particles.
[0035] 3. Adjust the outlet of the material guide pipe 31 to the weld seam through the adjustment of the motor 28, so that the metal particles are pre-filled.
[0036] 4. Close the vacuum chamber, and the vacuum chamber is evacuated by the vacuum unit. When the vacuum of the gun and the vacuum of the chamber reach 7E-2 and 8E-3 respectively, turn on the intermediate frequency unit, parameter power supply, high voltage and filament current, and the electron gun 3...
Embodiment 2
[0040] Embodiment 2, select non-melting slag inclusions of particles and wire filling welding, the specific implementation steps are as follows:
[0041] 1. Turn on the high-voltage power supply 6, start the vacuum preheating for 45 minutes, and fix the substrate learned by additive manufacturing on the workbench;
[0042] 2. Wrap the n kinds of wire materials required for additive manufacturing on the corresponding welding wire spools 12, respectively install them on the corresponding welding wire spool shafts 13, and pass the welding wire through the wire guide nozzle and the concave hole on the active wire feeding wheel. Groove, connecting rod mechanism, groove on the driven wire feed wheel, enter the wire feed hose, turn on the control switch of the wire feeder, pass the metal wire through the wire feed hose, the four-dimensional adjustment machine, and pass through the wire guide nozzle . Adjust the protruding length of the two wires. The metal particles required for fi...
Embodiment 3
[0048] Embodiment 3, the same kind of wire material is selected to be fed at the same speed for multi-wire additive manufacturing, and the specific implementation steps are as follows:
[0049] Turn on the high-voltage power supply 6, start the vacuum preheating for 45 minutes, and fix the substrate learned by additive manufacturing on the workbench;
[0050] The same kind of wire required for additive manufacturing is wound on the wire spool 12, and installed on the wire spool shaft 13 respectively, and the welding wire is passed through the wire guide nozzle, the groove on the active wire feed wheel, the connecting rod mechanism, Drive the groove on the wire feeding wheel into the wire feeding hose, turn on the control switch of the wire feeding machine, pass the metal wire through the wire feeding hose, the four-dimensional adjustment machine, and pass through the wire guide nozzle. Adjust the protruding length of the two wires.
[0051] The wire feeding regulator is adjus...
PUM
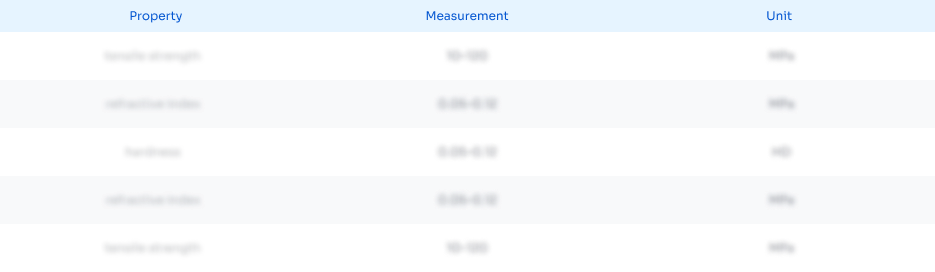
Abstract
Description
Claims
Application Information

- R&D Engineer
- R&D Manager
- IP Professional
- Industry Leading Data Capabilities
- Powerful AI technology
- Patent DNA Extraction
Browse by: Latest US Patents, China's latest patents, Technical Efficacy Thesaurus, Application Domain, Technology Topic, Popular Technical Reports.
© 2024 PatSnap. All rights reserved.Legal|Privacy policy|Modern Slavery Act Transparency Statement|Sitemap|About US| Contact US: help@patsnap.com