Method for preparing fluorine content- and dimension-adjustable carbon fluoride fibers
A technology of carbon fluoride and carbon fluoride adjustment, which is applied in the fields of carbon fiber, fiber treatment, textiles and papermaking, etc. It can solve the problems of high equipment requirements, long processing time, harsh reaction conditions, etc., and achieve simple reaction devices and short reaction time , cheap effect
- Summary
- Abstract
- Description
- Claims
- Application Information
AI Technical Summary
Problems solved by technology
Method used
Image
Examples
Embodiment 1
[0026] Add 0.1g fluorinated carbon fiber (the size of the raw material is 4000-5000μm, the fluorine content is 47at.%), 30mL ethylenediamine, and stir the reaction at 120°C for 3 hours under the protection of nitrogen. After cooling, use a 0.45 μm organic membrane to suction filter, wash, collect and dry the filter cake to obtain fluorinated carbon fibers with a size of 50-100 μm, a fluorine content of 34.3 at.%, a nitrogen content of 4.2 at.%, and significantly improved dispersion stability. The yield (yield=product mass / raw material mass) was 75%. After collecting the filtrate and removing the solvent with a rotary evaporator, fluorinated carbon fibers with an element content close to that of the filter cake and a size of less than 0.45 μm were obtained, with a yield of 15%.
Embodiment 2
[0028] Add 0.1g fluorinated carbon fiber (raw material size 4000-5000μm, fluorine content 47at.%), 30mL ethylenediamine into a round bottom flask, and stir at 100°C for 5 hours under nitrogen protection. After cooling, use a 0.45 μm organic membrane to suction filter and wash, collect the filter cake and dry it to obtain a fluorinated carbon fiber similar to Example 1, with a yield of 77%. Collect the sample in the filtrate to obtain an element content close to that of the filter cake, and the size is less than 0.45 μm fluorinated carbon fibers with a yield of 17%.
Embodiment 3
[0030] Add 0.1g fluorinated carbon fiber (raw material size 3500-4500μm, fluorine content 57at.%), 10mL ethylenediamine into a round bottom flask, and stir at 60°C for 8 hours under the protection of argon. After cooling, use a 0.45 μm organic membrane to filter and wash, collect the filter cake and dry it to obtain a fluorinated carbon fiber with a fluorine content and size close to that of the raw material and with improved dispersion. The yield is 71%. The cake was close, with a yield of 13% for fluorinated carbon fibers with a size below 0.45 μm.
PUM
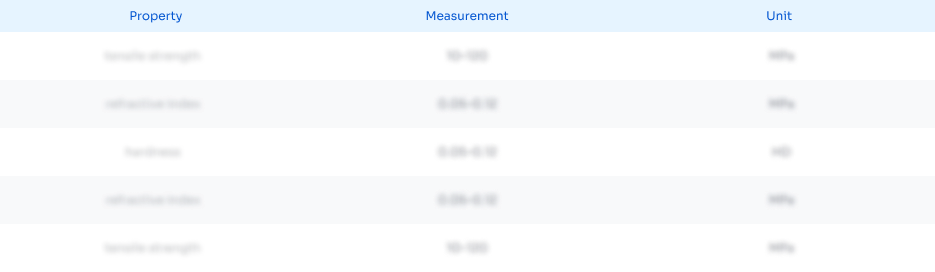
Abstract
Description
Claims
Application Information

- Generate Ideas
- Intellectual Property
- Life Sciences
- Materials
- Tech Scout
- Unparalleled Data Quality
- Higher Quality Content
- 60% Fewer Hallucinations
Browse by: Latest US Patents, China's latest patents, Technical Efficacy Thesaurus, Application Domain, Technology Topic, Popular Technical Reports.
© 2025 PatSnap. All rights reserved.Legal|Privacy policy|Modern Slavery Act Transparency Statement|Sitemap|About US| Contact US: help@patsnap.com