Plastic screen cloth for chemical engineering powder screening
A technology of plastic screen mesh and powder material, applied in the field of chemical equipment, can solve the problems of shortening the service life of the screen mesh, introducing impurities into the powder, polluting the powder, etc., and achieving the effect of reducing replacement cost, prolonging service life and long service life.
- Summary
- Abstract
- Description
- Claims
- Application Information
AI Technical Summary
Problems solved by technology
Method used
Examples
Embodiment 1
[0023] (1) Add 5 parts of C5 petroleum resin and 2 parts of ultra-fine polytetrafluoroethylene powder to 25 parts of hard PVC regenerated granules, and heat up to 125-130 °C at a heating rate of 5 °C / min and mix for 30 minutes, then add 3 parts of organic fillers and 0.5 part of nano-zinc oxide, continue to insulate and mix for 15 minutes to obtain material I;
[0024] (2) Add 2 parts of Darmar resin and 1 part of polymethyl methacrylate to 10 parts of saturated polyester resin, and heat up to 120-125 ° C at a heating rate of 5 ° C / min and mix for 15 minutes, then add 3 parts Ceramic micropowder and 1 part of molecular sieve raw powder, continue to keep warm and mix for 15 minutes to obtain material II;
[0025] (3) Add material II, 5 parts of lignocellulose, 3 parts of bamboo powder, 0.5 part of lanolin alcohol and 0.05 part of lanthanum oxide to material I, mix well, and the resulting mixture is processed into a plastic screen by injection molding.
[0026] Preparation of...
Embodiment 2
[0029] (1) Add 5 parts of C5 petroleum resin and 2 parts of ultra-fine polytetrafluoroethylene powder to 25 parts of hard PVC regenerated granules, and heat up to 125-130 °C at a heating rate of 5 °C / min and mix for 30 minutes, then add 5 parts of organic filler and 0.5 part of nano-zinc oxide, continue to keep warm and mix for 15 minutes to obtain material I;
[0030] (2) Add 2 parts of Darmar resin and 2 parts of polymethyl methacrylate to 10 parts of saturated polyester resin, and heat up to 120-125 ° C at a heating rate of 5 ° C / min and mix for 15 minutes, then add 4 parts Ceramic micropowder and 1 part of molecular sieve raw powder, continue to keep warm and mix for 15 minutes to obtain material II;
[0031] (3) Add material II, 8 parts of lignocellulose, 3 parts of bamboo powder, 0.5 part of lanolin alcohol and 0.05 part of lanthanum oxide to material I, mix well, and the resulting mixture is processed into a plastic screen by injection molding.
[0032] Preparation o...
Embodiment 3
[0035] Utilize the plastic sieve made in Example 1 and Example 2 to sieve the same batch of powder, and test its performance, the results are shown in Table 1.
[0036] The performance of table 1 plastic screen of the present invention
[0037] Test items Example 1 screen Example 2 screen Corrosion resistance no corrosion no corrosion wear resistance no wear no wear Vibration resistance No deformation and damage No deformation and damage
[0038] Corrosion resistance test conditions: soak in 3wt% sodium chloride solution, 10wt% sulfuric acid solution, 10wt% sodium hydroxide solution for 24 hours each;
[0039] Wear resistance test conditions: grinding disc Φ122mm, rotating speed 185r / min, hardness 60HRC, surface roughness Ra=0.4μm, grinding time 2h, load 30kg;
[0040] Vibration resistance test conditions: the vibration frequency of the vibration motor is 3000r / min, the excitation force is 50kN, and the vibration time is 48h.
PUM
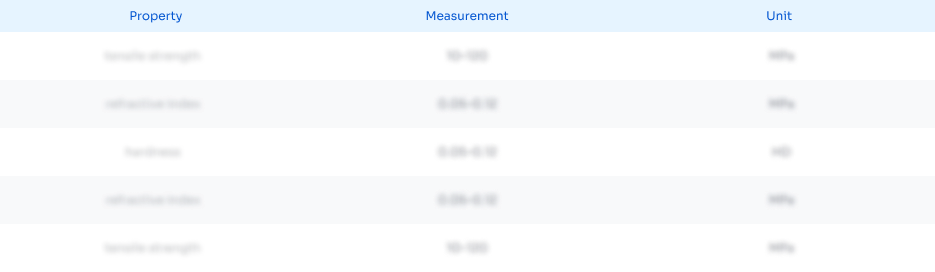
Abstract
Description
Claims
Application Information

- Generate Ideas
- Intellectual Property
- Life Sciences
- Materials
- Tech Scout
- Unparalleled Data Quality
- Higher Quality Content
- 60% Fewer Hallucinations
Browse by: Latest US Patents, China's latest patents, Technical Efficacy Thesaurus, Application Domain, Technology Topic, Popular Technical Reports.
© 2025 PatSnap. All rights reserved.Legal|Privacy policy|Modern Slavery Act Transparency Statement|Sitemap|About US| Contact US: help@patsnap.com