Process for reducing celestine in rotary hearth furnace to produce strontium sulfide
A technology of celestite and strontium sulfide, applied in the direction of magnesium/calcium/strontium/barium sulfide/polysulfide, energy input, etc., can solve the problems of low recovery rate, high cost, poor economic benefit, etc., and achieve high SrS production capacity , fast reduction reaction and high degree of control
- Summary
- Abstract
- Description
- Claims
- Application Information
AI Technical Summary
Problems solved by technology
Method used
Image
Examples
Embodiment 1
[0015] Will contain 65.6wt% SrSO 4 , 11.5wt% CaSO 4 , 8.2wt% CaCO 3 and 12.6 wt% BaSO 4 The composed celestite concentrate powder is ground in a ball mill so that its particle size reaches -100 mesh and is greater than 80%; the commercially available anthracite coal powder (0.2wt% S, 8.5wt% ash and 91.2wt% fixed carbon content) is sieved to make it The particle size reaches -100 mesh greater than 50%. Celestite concentrate powder and anthracite are batched and weighed according to the weight ratio of 85:15, and continuously added to the ball mill for mixing and grinding for 50 minutes, with a material-to-ball ratio of 10:1. Put the mixed raw materials into the sand mixer and mix them mechanically. At the same time, add 1.5wt% bentonite, 5wt% water and 2wt% syrup binder to make a wet material. The overall moisture content of the wet material should be controlled At 8 wt%. Afterwards, the wet material is continuously added to a double-roller ball press and pressed into elli...
PUM
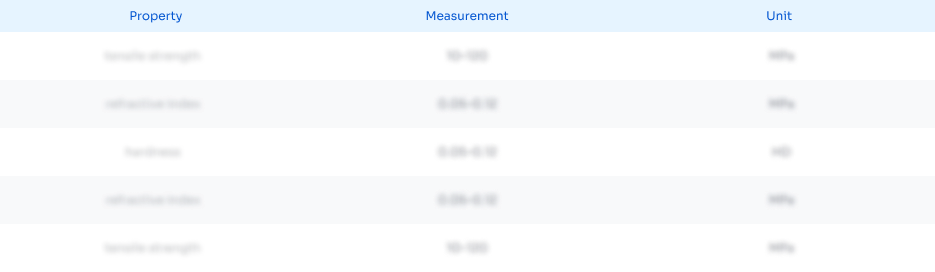
Abstract
Description
Claims
Application Information

- Generate Ideas
- Intellectual Property
- Life Sciences
- Materials
- Tech Scout
- Unparalleled Data Quality
- Higher Quality Content
- 60% Fewer Hallucinations
Browse by: Latest US Patents, China's latest patents, Technical Efficacy Thesaurus, Application Domain, Technology Topic, Popular Technical Reports.
© 2025 PatSnap. All rights reserved.Legal|Privacy policy|Modern Slavery Act Transparency Statement|Sitemap|About US| Contact US: help@patsnap.com