Catalyst for propane dehydrogenation to propylene, preparation method and application thereof
A propane dehydrogenation and catalyst technology, applied in chemical instruments and methods, metal/metal oxide/metal hydroxide catalysts, physical/chemical process catalysts, etc., can solve the problem of low conversion rate of propylene selectivity
- Summary
- Abstract
- Description
- Claims
- Application Information
AI Technical Summary
Problems solved by technology
Method used
Image
Examples
Embodiment 1
[0037] This example is used to illustrate the preparation of the catalyst for propane dehydrogenation to propylene provided by the present invention.
[0038] Preparation: impregnate 60g of γ-alumina (Shandong Aluminum) at 75°C in 0.03mol / L chloroplatinic acid (Sinopharm Chemical Reagent Co., Ltd.), 0.2mol / L stannous chloride (Tianjin Guangfu Fine Chemical Research ) and 2mol / L boric acid (Sinopharm Group Chemical Reagent Co., Ltd.) aqueous solution for 0.5h, wherein the volume of the solution was measured according to the mass content of the catalyst component, and dried by rotary evaporation at 75°C for 0.5h, then the The material was placed in a muffle furnace and calcined in an air atmosphere at 450° C. for 3 hours to obtain catalyst precursor I. Take out catalyst precursor I, place it in tube furnace, under H 2 and C 2 h 4 The catalyst precursor II was obtained by calcining in a mixed atmosphere with a volume ratio of 1:1 for 15 min at a calcining temperature of 500°C....
Embodiment 2
[0042] Preparation: The preparation method is the same as in Example 1, but the active components of the catalyst and the mass content of the auxiliary agent are different, and the catalyst 2 is prepared, and its composition is Al 2 o 3 / Pt / Sn-C-B.
[0043] Based on the total mass of catalyst 2, the mass content of each component in catalyst 2 is shown in Table 1.
[0044] Detection: Fill the catalyst 2 in the fixed bed reactor, the filling volume is 30mL, and the volume space velocity of the propane feed is controlled to be 500h -1 , the reaction pressure is normal pressure, the temperature at the inlet of the reactor is 565° C., and the reaction is carried out for 3 hours. The propane dehydrogenation products are analyzed by HP7890 gas chromatography. The test results are shown in Table 2.
Embodiment 3
[0046] Preparation: The preparation method is the same as in Example 1, but the active components of the catalyst and the mass content of the auxiliary agent are different, and the catalyst 3 is prepared, and its composition is Al 2 o 3 / Pt / Sn-C-B.
[0047] Based on the total mass of catalyst 3, the mass content of each component in catalyst 3 is shown in Table 1.
[0048] Detection: Fill the catalyst 3 in the fixed bed reactor, the filling volume is 30mL, and the volume space velocity of the propane feed is controlled to be 1600h -1 , the reaction pressure is normal pressure, the inlet temperature of the reactor is 600° C., and the reaction is carried out for 3 hours. The propane dehydrogenation products are analyzed by HP7890 gas chromatography. The test results are shown in Table 2.
PUM
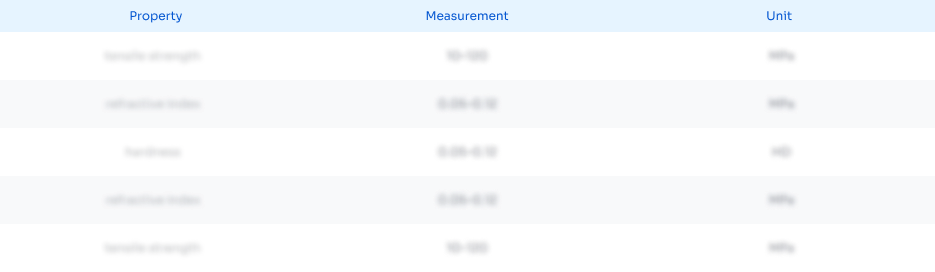
Abstract
Description
Claims
Application Information

- R&D
- Intellectual Property
- Life Sciences
- Materials
- Tech Scout
- Unparalleled Data Quality
- Higher Quality Content
- 60% Fewer Hallucinations
Browse by: Latest US Patents, China's latest patents, Technical Efficacy Thesaurus, Application Domain, Technology Topic, Popular Technical Reports.
© 2025 PatSnap. All rights reserved.Legal|Privacy policy|Modern Slavery Act Transparency Statement|Sitemap|About US| Contact US: help@patsnap.com