Aluminum rare earth alloy and preparation method thereof
A technology of aluminum rare earth and alloy, which is applied in the field of aluminum rare earth alloy and its preparation, can solve the problems of insufficient strength of aluminum rare earth alloy and achieve the effect of excellent strength
- Summary
- Abstract
- Description
- Claims
- Application Information
AI Technical Summary
Problems solved by technology
Method used
Image
Examples
Embodiment 1
[0015] An aluminum rare earth alloy, comprising the following raw materials in proportions by weight: 152 parts of aluminum, 18 parts of iron, 2 parts of cobalt, 5 parts of molybdenum, 5 parts of zirconium, 1 part of tin, 1 part of iridium, 1 part of terbium, and 1 part of dysprosium 1 part, 1 part of thulium, 1 part of ytterbium, 2 parts of potassium nitrate, 1 part of sodium aluminum fluoride, 1 part of hexafluorobenzene, 1 part of titanium sponge and 6 parts of chromium trioxide.
[0016] A kind of preparation method of aluminum rare earth alloy comprises the following steps:
[0017] 1) Pour 152 parts of aluminum, 18 parts of iron, 2 parts of cobalt, 5 parts of molybdenum, 5 parts of zirconium, 1 part of tin, 1 part of iridium, 1 part of terbium, 1 part of dysprosium, 1 part of thulium and 1 part of ytterbium into the In the metal smelting furnace, and then heated to 900°C, and stirred after all the raw materials are completely melted, liquid metal is obtained and set asid...
Embodiment 2
[0021] An aluminum rare earth alloy, comprising the following raw materials in proportions by weight: 150 parts of aluminum, 20 parts of iron, 4 parts of cobalt, 7 parts of molybdenum, 7 parts of zirconium, 3 parts of tin, 3 parts of iridium, 3 parts of terbium, and 3 parts of dysprosium 3 parts, 3 parts of thulium, 3 parts of ytterbium, 4 parts of potassium nitrate, 3 parts of sodium aluminum fluoride, 3 parts of hexafluorobenzene, 3 parts of titanium sponge and 8 parts of chromium trioxide.
[0022] A preparation method of aluminum rare earth alloy, comprising the following steps:
[0023] 1) Pour 150 parts of aluminum, 20 parts of iron, 4 parts of cobalt, 7 parts of molybdenum, 7 parts of zirconium, 3 parts of tin, 3 parts of iridium, 3 parts of terbium, 3 parts of dysprosium, 3 parts of thulium and 3 parts of ytterbium into the In the metal smelting furnace, and then heated to 900°C, and stirred after all the raw materials are completely melted, liquid metal is obtained an...
Embodiment 3
[0027] An aluminum rare earth alloy, comprising the following raw materials in parts by weight: 151 parts of aluminum, 19 parts of iron, 3 parts of cobalt, 6 parts of molybdenum, 6 parts of zirconium, 2 parts of tin, 2 parts of iridium, 2 parts of terbium, and 2 parts of dysprosium 2 parts of thulium, 2 parts of ytterbium, 3 parts of potassium nitrate, 2 parts of sodium aluminum fluoride, 2 parts of hexafluorobenzene, 2 parts of titanium sponge and 7 parts of chromium trioxide.
[0028] A preparation method of aluminum rare earth alloy, comprising the following steps:
[0029] 1) Pour 151 parts of aluminum, 19 parts of iron, 3 parts of cobalt, 6 parts of molybdenum, 6 parts of zirconium, 2 parts of tin, 2 parts of iridium, 2 parts of terbium, 2 parts of dysprosium, 2 parts of thulium and 2 parts of ytterbium into the In the metal smelting furnace, and then heated to 900°C, and stirred after all the raw materials are completely melted, liquid metal is obtained and set aside;
...
PUM
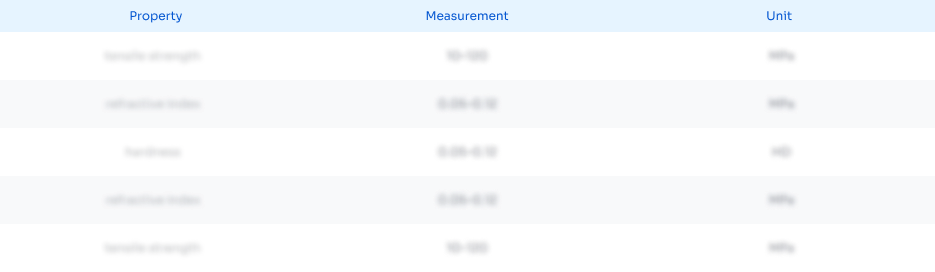
Abstract
Description
Claims
Application Information

- R&D
- Intellectual Property
- Life Sciences
- Materials
- Tech Scout
- Unparalleled Data Quality
- Higher Quality Content
- 60% Fewer Hallucinations
Browse by: Latest US Patents, China's latest patents, Technical Efficacy Thesaurus, Application Domain, Technology Topic, Popular Technical Reports.
© 2025 PatSnap. All rights reserved.Legal|Privacy policy|Modern Slavery Act Transparency Statement|Sitemap|About US| Contact US: help@patsnap.com