Synthetic method of dipropylene glycol dibenzoate
A technology of dipropylene glycol dibenzoate and synthesis method, which is applied in the direction of carboxylate preparation, chemical instruments and methods, preparation of organic compounds, etc., can solve the problems of using volatile solvents, slow reaction speed, high production cost, etc. Achieve the effect of reducing color number, short production cycle and small color number
- Summary
- Abstract
- Description
- Claims
- Application Information
AI Technical Summary
Problems solved by technology
Method used
Examples
Embodiment 1
[0017] Under the condition of nitrogen as the water-carrying agent, 134 parts (1 kg each, the same below) of dipropylene glycol, 243 parts of benzoic acid, 0.25 part of stannous oxalate, and 0.5 part of basic zirconium carbonate were added to the reaction kettle. Raise the temperature, start stirring after the material melts, control the temperature at 230-235°C, and continue to keep warm for 6 hours; cool down to 85°C, slowly add 10 parts of hydrogen peroxide into the reaction kettle, keep warm for 30min, then raise the temperature to 115°C, and keep warm at this temperature 15 minutes; cool down to 90°C, add 60 parts of 5% sodium carbonate solution and 50 parts of soft water, and stir for 30 minutes. During the process, you can add lye or soft water to adjust the pH of the system to about 9, otherwise it will not be easy to stratify; stand still Separated, drained phase; washed with 50 parts of soft water, the lower oil phase was dehydrated by vacuum distillation at 120°C to ...
Embodiment 2
[0019] Under the condition of nitrogen as the water-carrying agent, 134 parts of dipropylene glycol, 243 parts of benzoic acid, 0.5 part of stannous oxalate, and 0.5 part of basic zirconium carbonate were added to the reaction kettle. Raise the temperature, start stirring after the material melts, control the temperature at 230-235°C, and continue to keep warm for 6 hours; cool down to 85°C, slowly add 10 parts of hydrogen peroxide into the reaction kettle, keep warm for 30min, then raise the temperature to 115°C, and keep warm at this temperature 15 minutes; cool down to 90°C, add 60 parts of 5% sodium carbonate solution and 50 parts of soft water, and stir for 30 minutes. During the process, you can add lye or soft water to adjust the pH of the system to about 9, otherwise it will not be easy to stratify; stand still Separate the layers, drain the phase; wash with 50 parts of soft water, and dehydrate the lower oil phase at 120°C to obtain 320 parts of the finished product, t...
Embodiment 3
[0021] Under the condition of nitrogen as the water-carrying agent, 134 parts of dipropylene glycol, 243 parts of benzoic acid, 0.5 part of stannous oxalate, and 1.0 part of basic zirconium carbonate were added to the reaction kettle. Raise the temperature, start stirring after the material melts, control the temperature at 180-210°C, and continue to keep warm for 7 hours; cool down to 86-87°C, slowly add 12 parts of hydrogen peroxide into the reaction kettle, heat it up to 116°C after 38 minutes of heat preservation, and keep it at this temperature Keep warm for 18 minutes; cool down to 90°C, add 65 parts of 5% sodium carbonate solution and 50 parts of soft water, and stir for 30 minutes. During the process, add lye or soft water to adjust the pH of the system to about 9, otherwise it will not be easy to stratify; Stand to separate and separate, drain the phase; add 50 parts of soft water to wash, and the lower oil phase is dehydrated by vacuum distillation at 125°C to obtain ...
PUM
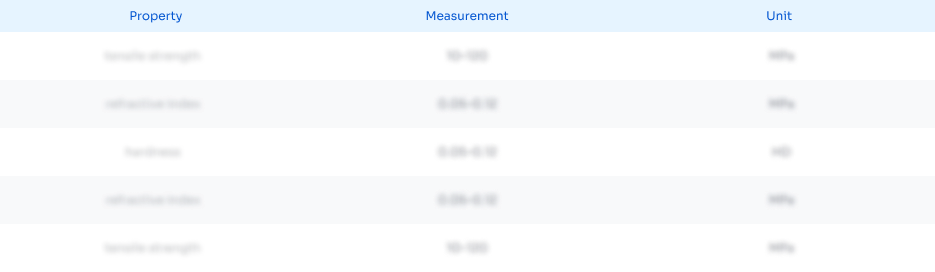
Abstract
Description
Claims
Application Information

- R&D
- Intellectual Property
- Life Sciences
- Materials
- Tech Scout
- Unparalleled Data Quality
- Higher Quality Content
- 60% Fewer Hallucinations
Browse by: Latest US Patents, China's latest patents, Technical Efficacy Thesaurus, Application Domain, Technology Topic, Popular Technical Reports.
© 2025 PatSnap. All rights reserved.Legal|Privacy policy|Modern Slavery Act Transparency Statement|Sitemap|About US| Contact US: help@patsnap.com