Deoiling agent for viscose fabric cold pad-batch one-bath method production process, and application method of deoiling agent
A technology of production process and application method, applied in the direction of dyeing method, textile and papermaking, dry cleaning fiber products, etc., can solve the problems of increasing the difficulty of wastewater treatment, cumbersome configuration, low efficiency, etc. The effect of production costs
- Summary
- Abstract
- Description
- Claims
- Application Information
AI Technical Summary
Problems solved by technology
Method used
Image
Examples
Embodiment 1
[0020] Prepare degreaser according to the following percentages by weight, wherein the percentage by weight of AES is 5%, the percentage by weight of AEO-9 is 1%, the percentage by weight of isopropyl alcohol is 5%, and the balance is water; fatty alcohol polyoxyethylene ether sulfuric acid Sodium (AES), AEO-9, and isopropanol are added to water and mixed well to obtain a degreaser.
[0021] The above-mentioned degreasing agent is used in the production process of the viscose fabric cold pad-batch one-bath method, and the specific steps are as follows:
[0022] (1) Based on 1L of water, dissolve 9g / L anhydrous sodium carbonate, 25g / L anhydrous sodium sulfate, and 1.5g / L ethylenediaminetetraacetic acid in water, then add 1g / L degreaser, and finally add 45g / L active turquoise blue dye is dissolved completely to obtain the treatment solution;
[0023] (2) Immerse the viscose fabric in the treatment solution, put the viscose fabric into the sealed room after two dips and two roll...
Embodiment 2
[0028] Prepare degreaser according to the following percentages by weight, wherein the percentage by weight of AES is 10%, the percentage by weight of AEO-9 is 15%, the percentage by weight of acetone is 9%, and the balance is water; the fatty alcohol polyoxyethylene ether sodium sulfate (AES), AEO-9, and isopropanol are added to water and mixed evenly to obtain a degreaser.
[0029] The above-mentioned degreasing agent is used in the production process of the viscose fabric cold pad-batch one-bath method, and the specific steps are as follows:
[0030] (1) Based on 1L of water, dissolve 8g / L anhydrous sodium carbonate, 20g / L anhydrous sodium sulfate, and 1.2g / L ethylenediaminetetraacetic acid in water, then add 2g / L degreaser, and finally add 35g / L reactive red dye and it is dissolved completely, obtains treatment liquid;
[0031] (2) Immerse the viscose fabric in the treatment solution, put the viscose fabric into the sealed room after two dips and two rollings, and stack i...
Embodiment 3
[0036] Prepare degreaser according to the following percentages by weight, wherein the percentage by weight of AES is 8%, the percentage by weight of AEO-9 is 10%, the percentage by weight of butanol is 8%, and the balance is water; the fatty alcohol polyoxyethylene ether sulfuric acid Sodium (AES), AEO-9, and isopropanol are added to water and mixed well to obtain a degreaser.
[0037] The above-mentioned degreasing agent is used in the production process of the viscose fabric cold pad-batch one-bath method, and the specific steps are as follows:
[0038] (1) Based on 1L of water, dissolve 7g / L anhydrous sodium carbonate, 15g / L anhydrous sodium sulfate, and 1g / L ethylenediaminetetraacetic acid in water, then add 3g / L degreaser, and finally add 25g / L active dark blue dye and it is completely dissolved to obtain a treatment solution;
[0039] (2) Immerse the viscose fabric in the treatment solution, put the viscose fabric in the sealed room after two dips and two rollings, an...
PUM
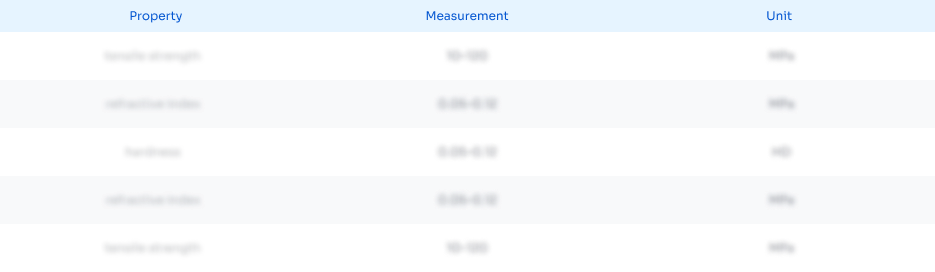
Abstract
Description
Claims
Application Information

- R&D
- Intellectual Property
- Life Sciences
- Materials
- Tech Scout
- Unparalleled Data Quality
- Higher Quality Content
- 60% Fewer Hallucinations
Browse by: Latest US Patents, China's latest patents, Technical Efficacy Thesaurus, Application Domain, Technology Topic, Popular Technical Reports.
© 2025 PatSnap. All rights reserved.Legal|Privacy policy|Modern Slavery Act Transparency Statement|Sitemap|About US| Contact US: help@patsnap.com