SMA-GFRP (Styrene Maleic Anhydride-Glass Fiber Reinforced Plastics) hyperelastic composite bar and manufacturing method thereof
A composite reinforcement and superelasticity technology, applied in the direction of structural elements, building components, building reinforcements, etc., to reduce the accumulation of residual displacement, improve the seismic performance, and improve the overall performance.
- Summary
- Abstract
- Description
- Claims
- Application Information
AI Technical Summary
Problems solved by technology
Method used
Image
Examples
Embodiment 1
[0025] Embodiment 1: as figure 1 As shown, the SMA-GFRP superelastic composite tendon includes SMA filament 1, GFRP filament bundle 2 and a flexible vinyl ester resin matrix 3 solidified between the SMA filament 1 and the GFRP filament bundle 2 through a pultrusion process; The SMA wire 1 and the GFRP wire bundle 2 are placed in parallel.
[0026] A kind of preparation method of SMA-GFRP superelastic composite bar, concrete steps are:
[0027] a. Place 24% by volume ultra-fine SMA wire 1 with a diameter of 0.5 mm and 44% GFRP tow 2 in parallel, and use a flexible vinyl ester resin matrix 3 to solidify between the two fibers through a pultrusion process, The volume percentage of the flexible vinyl ester resin matrix 3 is 32%, and it is formed by a pultrusion process, and the cross-section adopts the same circular shape as the steel bar;
[0028] b. In order to enhance the anchorage between the SMA-GFRP bar and the concrete, the surface of the SMA-GFRP bar is made of special s...
Embodiment 2
[0029] Embodiment 2: as figure 2 As shown, the SMA-GFRP superelastic composite tendon includes SMA filament 1, GFRP filament bundle 2 and a flexible vinyl ester resin matrix 3 solidified between the SMA filament 1 and the GFRP filament bundle 2 through a pultrusion process; The SMA wire 1 and the GFRP wire bundle 2 are placed in a ring.
[0030] A kind of preparation method of SMA-GFRP superelastic composite bar, concrete steps are:
[0031] a. Place 24% by volume ultra-fine SMA wire 1 with a diameter of 0.5 mm and 44% GFRP tow 2 in a ring, and use a flexible vinyl ester resin matrix 3 to solidify between the two fibers through a pultrusion process , the volume percentage of the flexible vinyl ester resin matrix 3 is 32%, formed by a pultrusion process, and the cross-sectional form adopts the same circular shape as the steel bar;
[0032] b. In order to enhance the anchorage between the SMA-GFRP bar and the concrete, the surface of the SMA-GFRP bar is made of special shape ...
PUM
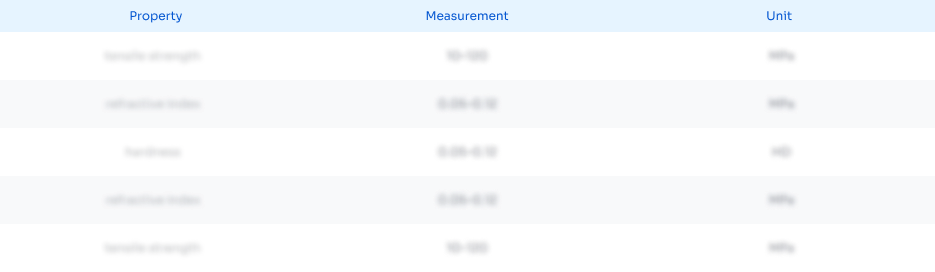
Abstract
Description
Claims
Application Information

- R&D
- Intellectual Property
- Life Sciences
- Materials
- Tech Scout
- Unparalleled Data Quality
- Higher Quality Content
- 60% Fewer Hallucinations
Browse by: Latest US Patents, China's latest patents, Technical Efficacy Thesaurus, Application Domain, Technology Topic, Popular Technical Reports.
© 2025 PatSnap. All rights reserved.Legal|Privacy policy|Modern Slavery Act Transparency Statement|Sitemap|About US| Contact US: help@patsnap.com