Preparation method of ultrathin graphite phase carbon nitride
A graphitic carbon nitride, ultra-thin technology, applied in the field of materials, can solve the problems of large thickness of graphitic carbon nitride sheets, restricting large-scale mass production, and high difficulty in preparation process operation, so as to avoid structural defects and environmental pollution. problems, no heavy metal pollution, cheap raw materials
- Summary
- Abstract
- Description
- Claims
- Application Information
AI Technical Summary
Problems solved by technology
Method used
Image
Examples
Embodiment 1
[0035] 1) Put melamine in a crucible, put it into an ash furnace, raise the temperature from room temperature to a calcination temperature of 520°C at a rate of 5°C / min, then calcinate at the calcination temperature for 4h, and then cool naturally to room temperature to obtain Lumpy g-C 3 N 4 ;
[0036] 2) Take 500mg of block g-C prepared in step 1) 3 N 4 , placed in a glass vessel with a volume of 250mL, add 200mL of deionized water, insert the probe of the ultrasonic cell breaker into the block g-C 3 N 4 In the deionized water mixture, the probe is 1cm deep into the liquid surface, the probe diameter is 10mm, the ultrasonic power is 900W, and the ultrasonic crushing is 90min;
[0037] 3) The obtained product was centrifuged at a speed of 8000r / min for 15min, and then the solid obtained after centrifugation was dried in a vacuum oven at 60°C for 12h;
[0038] 4) Transfer the dried solid into a crucible, then put it into an ash furnace, raise the temperature from room te...
Embodiment 2
[0040] 1) Put melamine in a crucible, then put it into an ash furnace, raise the temperature from room temperature to a calcination temperature of 520°C at a rate of 10°C / min, then calcinate at the calcination temperature for 4h, and then cool naturally to room temperature to obtain Lumpy g-C 3 N 4 ;
[0041] 2) Take 500mg of block g-C prepared in step 1) 3 N 4 , placed in a glass vessel with a volume of 250mL, add 150mL of deionized water, insert the probe of the ultrasonic cell breaker into the block g-C 3 N 4 In the deionized water mixture, the probe penetrates 1cm into the liquid surface, the diameter of the probe is 10mm, the ultrasonic power is 600W, and the ultrasonic crushing is 120min;
[0042] 3) The obtained product was centrifuged at a speed of 12000r / min for 5min, and then the solid obtained after centrifugation was dried in a vacuum oven at 80°C for 10h;
[0043] 4) Transfer the dried solid into a crucible, put it into an ash furnace, raise the temperature ...
Embodiment 3
[0045] 1) Put melamine in a crucible, then put it into an ash furnace, raise the temperature from room temperature to a calcination temperature of 520°C at a rate of 5°C / min, then calcinate at the calcination temperature for 3h, and then cool naturally to room temperature to obtain Lumpy g-C 3 N 4 ;
[0046] 2) Take 500mg of block g-C prepared in step 1) 3 N 4 , placed in a glass vessel with a volume of 250mL, add 200mL of deionized water, insert the probe of the ultrasonic cell breaker into the block g-C 3 N 4 In the deionized water mixture, the probe penetrates 1cm into the liquid surface, the diameter of the probe is 10mm, the ultrasonic power is 1200W, and the ultrasonic crushing is 60min;
[0047] 3) The obtained product was centrifuged at a speed of 10000r / min for 10min, and then the centrifuged solid was dried in a vacuum oven at 60°C for 12h;
[0048] 4) Transfer the dried solid into a crucible, then put it into the ash furnace, raise the temperature from room te...
PUM
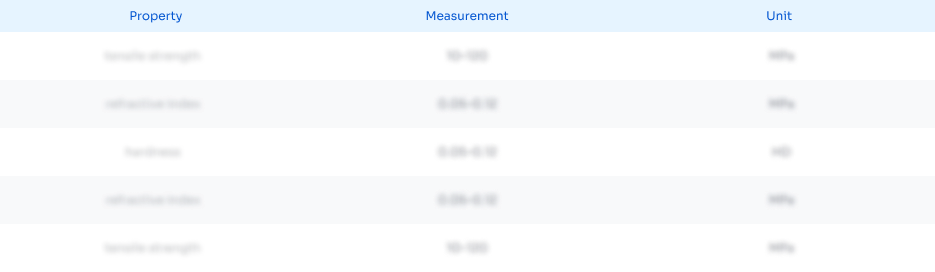
Abstract
Description
Claims
Application Information

- R&D
- Intellectual Property
- Life Sciences
- Materials
- Tech Scout
- Unparalleled Data Quality
- Higher Quality Content
- 60% Fewer Hallucinations
Browse by: Latest US Patents, China's latest patents, Technical Efficacy Thesaurus, Application Domain, Technology Topic, Popular Technical Reports.
© 2025 PatSnap. All rights reserved.Legal|Privacy policy|Modern Slavery Act Transparency Statement|Sitemap|About US| Contact US: help@patsnap.com