High-conductivity carbon brush materials and preparation method thereof
A high-conductivity, carbon brush technology, used in brush manufacturing, circuits, current collectors, etc., can solve the problems of easy wear and difficult to overcome, and achieve the effect of high electrical conductivity, improved wear resistance and hardness
- Summary
- Abstract
- Description
- Claims
- Application Information
AI Technical Summary
Problems solved by technology
Method used
Image
Examples
preparation example Construction
[0018] A preparation method for a high-conductivity carbon brush material, comprising the steps of:
[0019] (a) Graphene oxide, polypyrrole tube, acetylene black, zirconium nitride, chromium oxide, epoxy resin, silane coupling agent, electrolytic aluminum powder and dicyandiamide are mixed in proportion in corresponding parts by weight, and put into the mixer After mixing evenly, heat to 80-100°C and keep warm for 2-3 hours;
[0020] (b) continue to stir for 0.5 to 1 hour and then discharge the material. After the material is cooled to room temperature, put it into a pulverizer for reflux grinding, and pass the obtained powder through a 100-mesh sieve to obtain a micropowder; and
[0021] (c) Pressing the micropowder strip wire into shape, and the formed product is sent into a sintering furnace for high-temperature and high-pressure sintering. After sintering, it is cooled, punched, ground, embedding and arc-ground to form the high-conductivity powder. carbon brush material....
Embodiment 1
[0031] A high-conductivity carbon brush material consists of the following components in parts by weight: 15 parts of graphene oxide, 20 parts of polypyrrole tube, 20 parts of acetylene black, 2 parts of zirconium nitride, 2 parts of chromium oxide, and 10 parts of epoxy resin 2 parts, 2 parts of silane coupling agent, 1 part of dicyandiamide, 3 parts of electrolytic aluminum powder.
[0032] A kind of high-conductivity carbon brush material, comprises the following steps: with graphene oxide, polypyrrole tube, acetylene black, zirconium nitride, chromium oxide, epoxy resin, silane coupling agent, electrolytic aluminum powder and dicyandiamide by above-mentioned Proportional mixing, put into a mixer and mix evenly, heat to 80°C, keep warm for 2 hours, then continue to stir for 0.5 hours and then discharge, after the material is cooled to room temperature, put it into a pulverizer for reflux grinding, and the obtained powder passes through a 100-mesh sieve. Then the obtained mi...
Embodiment 2
[0035] A high-conductivity carbon brush material consists of the following components in parts by weight: 17 parts of graphene oxide, 22 parts of polypyrrole tube, 24 parts of acetylene black, 3 parts of zirconium nitride, 3 parts of chromium oxide, and 15 parts of epoxy resin 3 parts, 3 parts of silane coupling agent, 2 parts of dicyandiamide, 4 parts of electrolytic aluminum powder.
[0036]A preparation method for a high-conductivity carbon brush material, comprising the steps of: mixing graphene oxide, polypyrrole tube, acetylene black, zirconium nitride, chromium oxide, epoxy resin, silane coupling agent, electrolytic aluminum powder and dicyandiamide Mix the amines in proportion, put them into the mixer and mix evenly, heat to 900°C, keep warm for 2.5 hours, then continue to stir for 0.8 hours, then discharge the materials, after the materials are cooled to room temperature, put them into the pulverizer for reflux grinding, and the obtained powder passes through 100 mesh ...
PUM
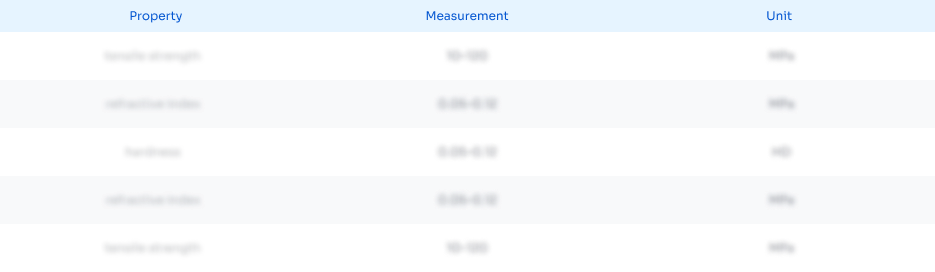
Abstract
Description
Claims
Application Information

- R&D
- Intellectual Property
- Life Sciences
- Materials
- Tech Scout
- Unparalleled Data Quality
- Higher Quality Content
- 60% Fewer Hallucinations
Browse by: Latest US Patents, China's latest patents, Technical Efficacy Thesaurus, Application Domain, Technology Topic, Popular Technical Reports.
© 2025 PatSnap. All rights reserved.Legal|Privacy policy|Modern Slavery Act Transparency Statement|Sitemap|About US| Contact US: help@patsnap.com