Corrosion method for ultra-high-voltage and high-specific-capacity positive electrode corrosion foil
An anode corrosion and ultra-high voltage technology, applied in capacitors, electrolytic capacitors, electrical components, etc., can solve the problems of small corrosion holes, high loss, and easy blockage of anode foils, and achieve the effects of large pore size, moderate density, and high mechanical strength
- Summary
- Abstract
- Description
- Claims
- Application Information
AI Technical Summary
Problems solved by technology
Method used
Image
Examples
Embodiment 1
[0042] The previous treatment: put the light foil into a sodium hydroxide solution with a concentration of 2wt%, and soak it at 30°C for 120s.
[0043] The first two treatments: put the above-mentioned aluminum foil that has undergone the first treatment into a mixed solution of 1 wt% sulfuric acid and 10 wt% nitric acid, and soak it at 50°C for 180s.
[0044] First-level DC electrochemical corrosion: put the aluminum foil that has undergone the above two treatments into a solution of 30Wt% sulfuric acid, 3Wt% hydrochloric acid, and 1Wt% aluminum ions, and electrolyze at 60°C for 50s, with a current density of 0.6A / cm 2 .
[0045] Intermediate treatment: put the aluminum foil that has undergone the above-mentioned one-stage direct current electrochemical corrosion into a dilute phosphoric acid solution with a concentration of pH=5.0, and soak at 20°C for 300s.
[0046] Secondary direct current electrochemical corrosion: put the aluminum foil treated above into a solution of...
Embodiment 2
[0050] The previous treatment: put the light foil into a sodium hydroxide solution with a concentration of 3wt%, and soak it at 40°C for 90s.
[0051] First-level DC electrochemical corrosion: Put the aluminum foil that has undergone the above two treatments into a solution of 35Wt% sulfuric acid, 4Wt% hydrochloric acid, and 1.5Wt% aluminum ions, electrolyze at 65°C for 60s, and the current density is 0.5A / cm 2 .
[0052] Intermediate treatment: put the aluminum foil that has undergone the above-mentioned first-stage direct current electrochemical corrosion into a sodium bicarbonate solution with a concentration of pH=9.0, and soak at 25°C for 240s.
[0053] Secondary direct current electrochemical corrosion: Put the aluminum foil treated above into a solution of 6wt% nitric acid and 0.3wt% aluminum ion, electrolyze at 70°C for 300s, and the current density is 0.15A / cm 2 .
[0054] Three-stage direct current electrochemical corrosion: put the aluminum foil that has undergo...
Embodiment 3
[0057] The previous treatment: put the light foil into a sodium hydroxide solution with a concentration of 4wt%, and soak it at 50°C for 90s.
[0058] The first two treatments: put the above-mentioned aluminum foil that has undergone the first treatment into a mixed solution of 3 wt% sulfuric acid and 15 wt% nitric acid, and soak it at 60°C for 150s.
[0059] First-level DC electrochemical corrosion: Put the aluminum foil that has undergone the above two treatments into a solution of 40Wt% sulfuric acid, 5Wt% hydrochloric acid, and 1Wt% aluminum ions, and electrolyze it at 70°C for 75s, with a current density of 0.4A / cm 2 .
[0060] Intermediate treatment: put the aluminum foil that has undergone the above-mentioned one-stage direct current electrochemical corrosion into a sodium carbonate solution with a concentration of pH=8.0, and soak at 30°C for 180s.
[0061] Two-stage direct current electrochemical corrosion: put the aluminum foil treated in the above process into a ...
PUM
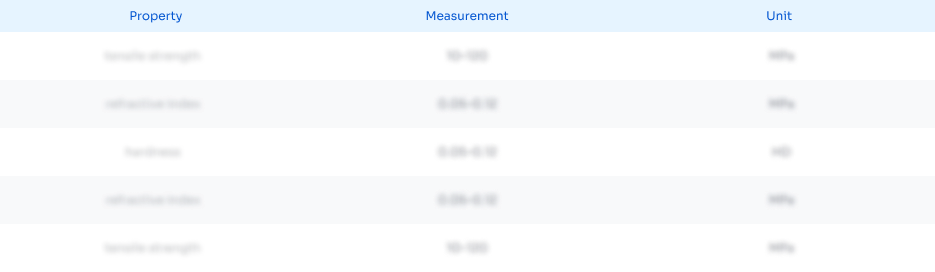
Abstract
Description
Claims
Application Information

- R&D Engineer
- R&D Manager
- IP Professional
- Industry Leading Data Capabilities
- Powerful AI technology
- Patent DNA Extraction
Browse by: Latest US Patents, China's latest patents, Technical Efficacy Thesaurus, Application Domain, Technology Topic, Popular Technical Reports.
© 2024 PatSnap. All rights reserved.Legal|Privacy policy|Modern Slavery Act Transparency Statement|Sitemap|About US| Contact US: help@patsnap.com