Rotary motion electrohydraulic control system for shield segment erector
An electro-hydraulic control system and rotary motion technology, applied in the direction of mechanical equipment, fluid pressure actuators, servo motors, etc., can solve the problems of impact oscillation, large impact torque, etc., to eliminate vibration impact, reduce the maximum impact torque, improve The effect of stability
- Summary
- Abstract
- Description
- Claims
- Application Information
AI Technical Summary
Problems solved by technology
Method used
Image
Examples
Embodiment
[0039] Set the rotating speed of the segment assembly machine to 6r / min, and the signal is a step signal, using AMESim software to establish figure 1 The model is simulated, and the parameters K are set to control it P = 1,K I =360, so
[0040]
[0041] Then the variable speed integral proportional integral controller parameters at the kth moment: proportional action constant 1, integral action constant f[e(k)]×360.
[0042] The speed response and impact torque of the rotary motion electro-hydraulic control system of the above-mentioned shield segment assembly machine are as follows: figure 2 and image 3 As shown, the figure shows the comparison with the existing technology, from figure 2 It can be seen that the present invention eliminates the system overshoot, but the adjustment time increases; from image 3 It can be seen from the figure that the present invention eliminates the vibration impact in the start-up phase, and the maximum impact is greatly reduced; ...
PUM
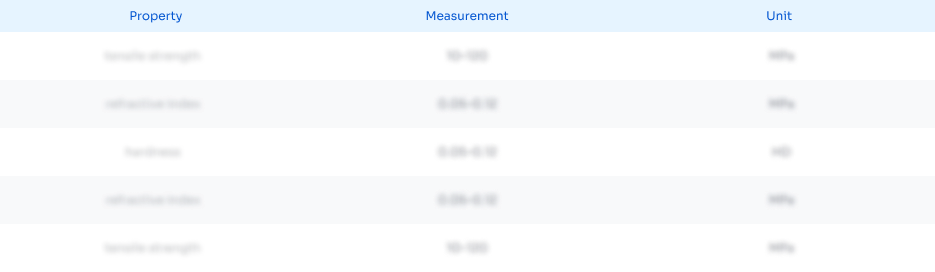
Abstract
Description
Claims
Application Information

- R&D Engineer
- R&D Manager
- IP Professional
- Industry Leading Data Capabilities
- Powerful AI technology
- Patent DNA Extraction
Browse by: Latest US Patents, China's latest patents, Technical Efficacy Thesaurus, Application Domain, Technology Topic, Popular Technical Reports.
© 2024 PatSnap. All rights reserved.Legal|Privacy policy|Modern Slavery Act Transparency Statement|Sitemap|About US| Contact US: help@patsnap.com