Halogenation reaction method
A technology of halogenation reaction and halogenation agent, applied in the direction of organic chemical methods, chemical instruments and methods, organic halogenation, etc., can solve problems such as uneven stirring, many side reactions, and long halogenation time, and achieve the effect of avoiding side reactions
- Summary
- Abstract
- Description
- Claims
- Application Information
AI Technical Summary
Problems solved by technology
Method used
Examples
Embodiment 1
[0032] Example 1 uses a packed supergravity reactor as the core reactor device, and sets the supergravity level to 200g. Toluene and catalyst FeCl 3 The solution enters the supergravity reactor through the liquid inlet pipe, and the chlorine gas enters the supergravity reactor through the gas inlet pipe. The materials are efficiently mixed and halogenated in the supergravity reactor, and the reacted liquid materials leave from the liquid outlet of the supergravity reactor. In the supergravity reactor, the reacted gaseous substances leave the supergravity reactor through the gas outlet pipe. Wherein the molar ratio of toluene to chlorine is 1:0.9, the mass content of the catalyst in toluene is 0.02wt%, and the reaction body temperature is 20°C. After analysis and detection, the content of polyhalogenated by-products is 0.09%, and the yield of monochlorotoluene is 99.6%.
Embodiment 2
[0033] Example 2 uses a spiral channel type supergravity reactor as the core reactor device, and sets the supergravity level to 800g. Using acid catalysis, mix acetone and 35% hydrochloric acid and enter the high gravity reactor through the liquid inlet pipe, chlorine gas enters the high gravity reactor through the gas inlet pipe, and the materials are efficiently mixed and halogenated in the high gravity reactor. The final liquid material leaves the supergravity reactor from the liquid outlet of the supergravity reactor, and the reacted gaseous substance leaves the supergravity reactor through the gas outlet pipe. Wherein, the feeding molar ratio is acetone:chlorine:hydrochloric acid=4.5:1:0.01, and the reaction body temperature is 20°C. After analysis and detection, the content of monochloroacetone in the product is 98.9%, and the content of 1,1-dichloroacetone is 0.08%.
Embodiment 3
[0034] Embodiment 3 uses a stator-rotor type supergravity reactor as the core reactor device, and sets the supergravity level to 5g-10g. Ethyl acetoacetate and sulfuryl chloride are input into the supergravity reactor through the liquid inlet pipe and the liquid inlet pipe at the same time. The materials are mixed efficiently in the supergravity reactor and halogenated. The outlet leaves the high-gravity reactor, and the reacted gaseous substances leave the high-gravity reactor through the gas outlet pipe. The molar ratio of ethyl acetoacetate to sulfuryl chloride is 1.1:05, and the temperature of the reaction body is 12-18°C. After analysis and detection, the content of polyhalogenated by-products is 0.01 wt%, and the yield of ethyl 2-chloroacetoacetate is 97.8%.
PUM
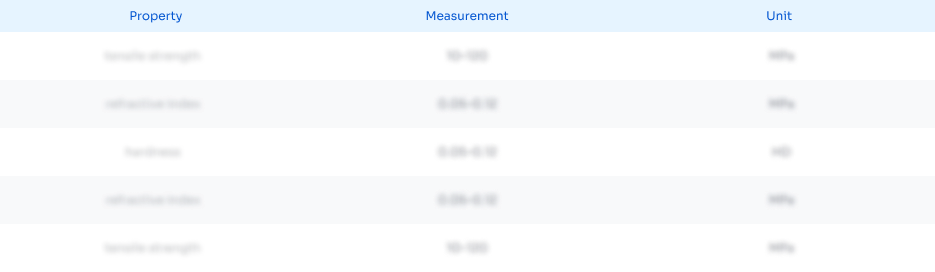
Abstract
Description
Claims
Application Information

- Generate Ideas
- Intellectual Property
- Life Sciences
- Materials
- Tech Scout
- Unparalleled Data Quality
- Higher Quality Content
- 60% Fewer Hallucinations
Browse by: Latest US Patents, China's latest patents, Technical Efficacy Thesaurus, Application Domain, Technology Topic, Popular Technical Reports.
© 2025 PatSnap. All rights reserved.Legal|Privacy policy|Modern Slavery Act Transparency Statement|Sitemap|About US| Contact US: help@patsnap.com