High-hardness alloy steel for door frame and preparation method thereof
A technology of high-hardness alloy steel and alloy steel, which is applied in the field of alloy steel, and can solve problems that affect the appearance and use, and the surface is prone to wear, corrosion, strength, hardness, toughness and other mechanical and mechanical performance defects.
- Summary
- Abstract
- Description
- Claims
- Application Information
AI Technical Summary
Problems solved by technology
Method used
Examples
Embodiment 1
[0020] (1) Wash the alloy steel with water, then perform anaerobic calcination at a temperature of 235°C for 5h, and then place it in sodium lauryl sulfate with a concentration of 30g / L for 35s of activation treatment;
[0021] (2) Heat the alloy steel after activation treatment from 20°C to 520°C at a heating rate of 10°C / min, and keep it at 520°C for 110 minutes to perform the first heating heat treatment; then from 520°C at 20°C / min Raise the temperature to 700°C at a heating rate of min, and keep it at 700°C for 60 minutes to perform the heat treatment of the second heating;
[0022] (3) Quenching the heat-treated alloy steel with a PAG quenching agent with a volume concentration of 6%, then heating at 500°C for 100min, then water-cooling to 125°C, then naturally cooling to 18°C, and finally placing In a magnesium chloride solution with a volume concentration of 18g / L, the high-hardness alloy steel A1 for the door frame is obtained;
[0023] Wherein, in parts by weight, t...
Embodiment 2
[0025] (1) The alloy steel is washed with water, followed by anaerobic calcination at a temperature of 295°C for 6h, and then placed in sodium lauryl sulfate with a concentration of 40g / L for 50s of activation treatment;
[0026] (2) Heat the alloy steel after activation treatment from 25°C to 540°C at a heating rate of 15°C / min, and keep it at 540°C for 130 minutes to perform the first heating heat treatment; then from 540°C at 25°C / min Raise the temperature to 720°C at a heating rate of min, and keep it at 720°C for 80 minutes to perform the heat treatment of the second heating;
[0027] (3) Quenching the heat-treated alloy steel with a PAG quenching agent with a volume concentration of 10%, then heating at 520°C for 120min, then water-cooling to 150°C, then naturally cooling to 25°C, and finally placing In the magnesium chloride solution that the volume concentration is 22g / L to make the high-hardness alloy steel A2 for the door frame;
[0028] Wherein, in parts by weight,...
Embodiment 3
[0030] (1) Wash the alloy steel with water and alcohol, then perform anaerobic calcination at a temperature of 260°C for 5.5h, and then place it in sodium lauryl sulfate with a concentration of 35g / L for 40s of activation treatment;
[0031] (2) Heat the alloy steel after activation treatment from 23°C to 530°C at a heating rate of 13°C / min, and keep it at 530°C for 120 minutes to perform the first heating heat treatment; then from 530°C at 20°C / min Raise the temperature to 710°C at a heating rate of min, and keep it at 710°C for 70 minutes to perform the heat treatment of the second heating;
[0032] (3) Quenching the heat-treated alloy steel with a PAG quenching agent with a volume concentration of 8%, then heating at 510°C for 110min, then water-cooling to 135°C, then naturally cooling to 22°C, and finally placing In a magnesium chloride solution with a volume concentration of 20g / L to obtain a high-hardness alloy steel A3 for door frames;
[0033] Wherein, in parts by wei...
PUM
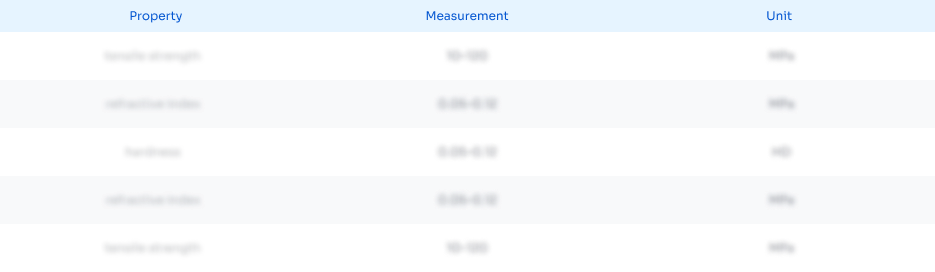
Abstract
Description
Claims
Application Information

- Generate Ideas
- Intellectual Property
- Life Sciences
- Materials
- Tech Scout
- Unparalleled Data Quality
- Higher Quality Content
- 60% Fewer Hallucinations
Browse by: Latest US Patents, China's latest patents, Technical Efficacy Thesaurus, Application Domain, Technology Topic, Popular Technical Reports.
© 2025 PatSnap. All rights reserved.Legal|Privacy policy|Modern Slavery Act Transparency Statement|Sitemap|About US| Contact US: help@patsnap.com