Modified phenolic resin heat insulation material used for external wall
A phenolic resin and thermal insulation material technology, applied in the field of thermal insulation materials, can solve the problems of mechanical properties, poor thermal stability, high brittleness, etc., and achieve the effects of excellent hardness and toughness, good elasticity, and excellent thermal insulation performance.
- Summary
- Abstract
- Description
- Claims
- Application Information
AI Technical Summary
Problems solved by technology
Method used
Examples
Embodiment 1
[0014] A modified phenolic resin insulation material for exterior walls proposed by the present invention, its raw materials include by weight: 30 parts of foamable phenolic resin, 5 parts of polyurethane, 1 part of foam stabilizer, 5 parts of foaming agent, azobis 1 part of formamide, 2 parts of surfactant, 5 parts of modified bagasse, 10 parts of silicone modified phenolic resin, 5 parts of expanded polystyrene, 1.2 parts of curing agent T-31, 0.1 part of epoxy accelerator, 2 parts of methyl vinyl dichlorosilane, 2 parts of p-toluenesulfonyl chloride, 12 parts of wollastonite, 3 parts of calcined clay, 15 parts of peat, and 50 parts of water.
Embodiment 2
[0016] A modified phenolic resin thermal insulation material for exterior walls proposed by the present invention, its raw materials include by weight: 60 parts of foamable phenolic resin, 1 part of polyurethane, 5 parts of foam stabilizer, 1 part of foaming agent, azobis 2 parts of formamide, 1 part of surfactant, 12 parts of modified bagasse, 5 parts of silicone modified phenolic resin, 10 parts of expanded polystyrene, 0.5 part of curing agent T-31, 0.8 part of epoxy accelerator, 1 part of methyl vinyl dichlorosilane, 6 parts of p-toluenesulfonyl chloride, 2 parts of wollastonite, 12 parts of calcined clay, 5 parts of peat, and 80 parts of water.
[0017] The modified bagasse is prepared by the following process: mixing and stirring bagasse, sodium monochloroacetate, and absolute ethanol, adding sodium hydroxide to stir, standing at room temperature, adjusting the pH value of the system to neutral with acetic acid, washing with ethanol, and suction filtration. Dry, add holl...
Embodiment 3
[0019] A modified phenolic resin insulation material for exterior walls proposed by the present invention, its raw materials include by weight: 40 parts of foamable phenolic resin, 4 parts of polyurethane, 2 parts of foam stabilizer, 4 parts of foaming agent, azobis 1.2 parts of formamide, 1.7 parts of surfactant, 6 parts of modified bagasse, 8 parts of silicone modified phenolic resin, 7 parts of expanded polystyrene, 1 part of curing agent T-31, 0.3 parts of epoxy accelerator, 1.7 parts of methyl vinyl dichlorosilane, 3 parts of p-toluenesulfonyl chloride, 10 parts of wollastonite, 5 parts of calcined clay, 12 parts of peat, and 60 parts of water.
[0020] The modified bagasse is prepared by the following process: 8 parts of bagasse, 5 parts of sodium monochloroacetate, and 60 parts of absolute ethanol are mixed and stirred for 20 minutes in parts by weight, the stirring temperature is 40 ° C, 1 part of sodium hydroxide is added and stirred for 50 minutes, and the The speed ...
PUM
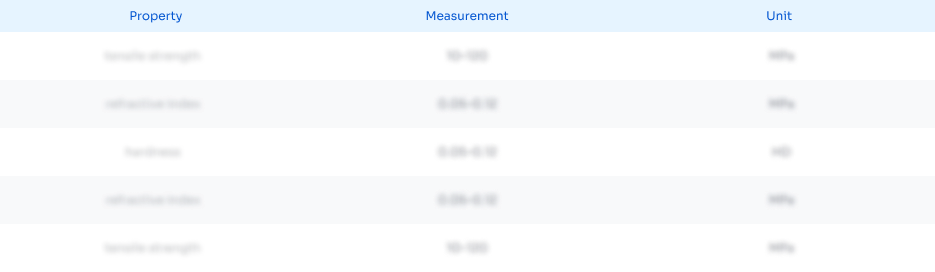
Abstract
Description
Claims
Application Information

- R&D Engineer
- R&D Manager
- IP Professional
- Industry Leading Data Capabilities
- Powerful AI technology
- Patent DNA Extraction
Browse by: Latest US Patents, China's latest patents, Technical Efficacy Thesaurus, Application Domain, Technology Topic, Popular Technical Reports.
© 2024 PatSnap. All rights reserved.Legal|Privacy policy|Modern Slavery Act Transparency Statement|Sitemap|About US| Contact US: help@patsnap.com