Resistance welding technology with online continuous weld heat treatment
A resistance welding and process technology, applied in resistance welding equipment, welding equipment, welding/welding/cutting items, etc., can solve the sudden rise and drop of temperature in the welding area, the inability to meet the requirements of special material steel grades, weld seams and heat-affected zones Fracture and other problems, to avoid the escape of diffusible hydrogen, avoid hydrogen-induced cracks, and reduce the welding strain rate.
- Summary
- Abstract
- Description
- Claims
- Application Information
AI Technical Summary
Problems solved by technology
Method used
Image
Examples
Embodiment 1
[0045] A resistance welding machine with on-line continuous weld seam heat treatment, including a welding trolley 1, and a shearing device 2, a resistance welding device 3 and a rolling device 4 installed on the welding trolley 1 in sequence, and the welding trolley 1 Corresponding to the position in front of the resistance welding device 3 is provided with a preheating device 5 that can perform online continuous temperature rise and preheating of the welding area, and the preheating device 5 is arranged between the shearing device 2 and the resistance welding device 3, The position corresponding to the rear of the resistance welding device 3 on the welding trolley 1 is provided with a heat treatment device 6 capable of performing online continuous weld seam heat treatment on the weld seam area. Preheating the welding area before welding can not only reduce the welding stress, but also reduce the welding strain rate, which is beneficial to avoid welding cracks and the escape of...
Embodiment 2
[0050] Embodiment 2 (for high-strength alloy steel and high-phosphorus steel, etc., of course, 400 series stainless steel can also adopt the scheme of this embodiment, but it is easy to produce brittleness):
[0051] A resistance welding process with on-line continuous weld seam heat treatment, comprising the following steps:
[0052] 1) The on-line strip steel is cut and stitched by the shearing device 2 on the shearing station of the welding process;
[0053] 2) After the shearing and jointing is completed, the welding area of the on-line strip steel is preheated to 150-200° C. through the preheating device 5 on the preheating station of the welding process;
[0054] 3) After heating up and preheating, the online strip steel is welded by the resistance welding device 3 on the welding station of the welding process;
[0055] 4a1) After the welding is completed, the weld zone of the online strip steel is carried out on the primary normalizing station of the welding process ...
Embodiment 3
[0061] Embodiment 3 (specifically for 400 series stainless steel):
[0062] A resistance welding process with on-line continuous weld seam heat treatment, comprising the following steps:
[0063] 1) The on-line strip steel is cut and stitched by the shearing device 2 on the shearing station of the welding process;
[0064]2) After the shearing and jointing is completed, the welding area of the on-line strip steel is preheated to 100-200° C. through the preheating device 5 on the preheating station of the welding process;
[0065] 3) After heating up and preheating, the online steel strip is welded by the resistance welding device 3 on the welding station of the welding process;
[0066] 4a1) After the welding is completed, the weld zone of the online strip steel is carried out on the primary normalizing station of the welding process through the primary normalizing mechanism 6a1 for primary normalizing of the online continuous weld seam, and the primary normalizing temperat...
PUM
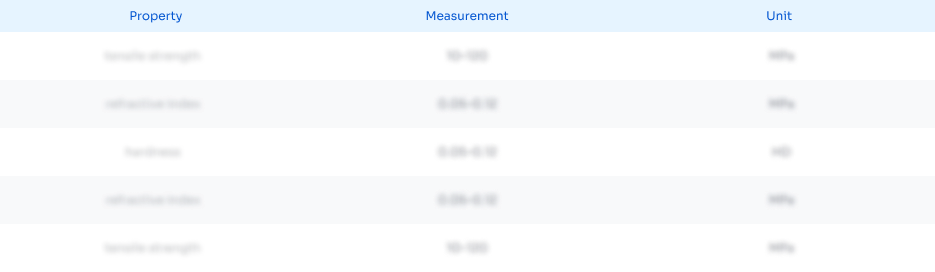
Abstract
Description
Claims
Application Information

- R&D
- Intellectual Property
- Life Sciences
- Materials
- Tech Scout
- Unparalleled Data Quality
- Higher Quality Content
- 60% Fewer Hallucinations
Browse by: Latest US Patents, China's latest patents, Technical Efficacy Thesaurus, Application Domain, Technology Topic, Popular Technical Reports.
© 2025 PatSnap. All rights reserved.Legal|Privacy policy|Modern Slavery Act Transparency Statement|Sitemap|About US| Contact US: help@patsnap.com