A cleaning method for iron core used for winding ≤0.1mm thick silicon steel strip
A silicon steel belt and iron core technology, applied in the field of iron core cleaning, can solve the problems of reducing the resistance of the iron core end face, the iron core is easy to be corroded, and the end faces are easy to contact together, etc., to achieve the effect of improving the service life
- Summary
- Abstract
- Description
- Claims
- Application Information
AI Technical Summary
Problems solved by technology
Method used
Examples
Embodiment 1
[0025] A silicon steel thin strip thickness of the present embodiment is 0.03mm, and its winding iron core cleaning steps:
[0026] 1) For the first time, use water to remove impurities and oil stains on the surface of the iron core until the surface is clean;
[0027] 2) Stop the cleaned iron core to remove water droplets on the surface, and the moisture content on the surface after dripping is 0.0097wt%;
[0028] 3) Spray pickling with sulfuric acid on the cutting surface of the iron core, the pickling time is 2.5min; the pH value of the pickling solution is 4.5;
[0029] 4) Drip the acid solution on the surface of the iron core washed with acid and sulfuric acid, and the content of the acid solution on the surface of each layer after dripping is 0.009wt%;
[0030] 5) Clean the acid solution on the surface of the iron core with water for the second time until the surface is clean;
[0031] 6) The iron core is sprayed with sodium hydroxide solution with a pH of 8.4 for alka...
Embodiment 2
[0038] A silicon steel thin strip thickness of the present embodiment is 0.01mm, and its winding iron core cleaning steps:
[0039] 1) For the first time, use water to remove impurities and oil stains on the surface of the iron core until the surface is clean;
[0040] 2) Stop the cleaned iron core to remove water droplets on the surface, and the moisture content on the surface after dripping is 0.0093wt%;
[0041] 3) Spray pickling with sulfuric acid on the cutting surface of the iron core, the pickling time is 0.5min; the pH value of the pickling solution is 3.5;
[0042] 4) Drip the acid solution on the surface of the iron core after being washed with acid and sulfuric acid, and the content of the acid solution on the surface of each layer after dropping is 0.0092wt%;
[0043] 5) Clean the acid solution on the surface of the iron core with water for the second time until the surface is clean;
[0044] 6) The iron core is sprayed with potassium hydroxide solution with a pH...
Embodiment 3
[0051] A silicon steel thin strip thickness of the present embodiment is 0.03mm, and its winding iron core cleaning steps:
[0052] 1) For the first time, use water to remove impurities and oil stains on the surface of the iron core until the surface is clean;
[0053] 2) Stop the cleaned iron core to remove water droplets on the surface, and the moisture content on the surface after dripping is 0.0093wt%;
[0054] 3) Spray pickling with sulfuric acid on the cutting surface of the iron core, the pickling time is 3min; the pH value of the pickling solution is 5.5;
[0055] 4) Drip the acid solution on the surface of the iron core after being washed with acid and sulfuric acid, and the content of the acid solution on the surface of each layer after dropping is 0.0092wt%;
[0056] 5) Clean the acid solution on the surface of the iron core with water for the second time until the surface is clean;
[0057] 6) The iron core is sprayed with an aluminum hydroxide solution with a pH...
PUM
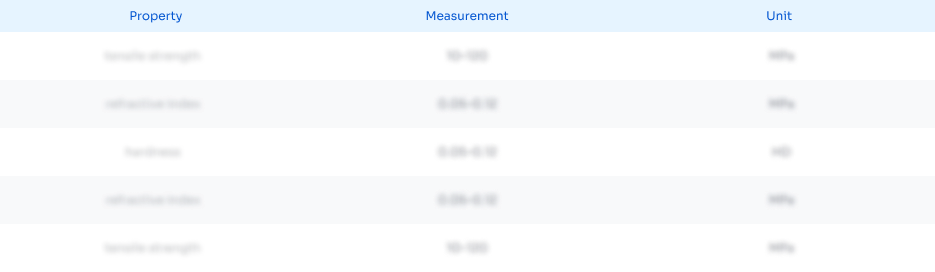
Abstract
Description
Claims
Application Information

- R&D
- Intellectual Property
- Life Sciences
- Materials
- Tech Scout
- Unparalleled Data Quality
- Higher Quality Content
- 60% Fewer Hallucinations
Browse by: Latest US Patents, China's latest patents, Technical Efficacy Thesaurus, Application Domain, Technology Topic, Popular Technical Reports.
© 2025 PatSnap. All rights reserved.Legal|Privacy policy|Modern Slavery Act Transparency Statement|Sitemap|About US| Contact US: help@patsnap.com