Fast resin wetting forming technology based on material flow prepeak monitoring
A molding process and resin technology, which is applied in the field of rapid resin infiltration molding process, can solve the problems of inability to realize material flow front peak monitoring and process automatic control, inability to realize process automatic control, high labor cost, etc., and reduce filling such as incomplete infiltration The probability of defect occurrence, the reduction of labor consumption and production costs, and the effect of high automation
- Summary
- Abstract
- Description
- Claims
- Application Information
AI Technical Summary
Problems solved by technology
Method used
Image
Examples
Embodiment 1
[0074] In this embodiment, each of the three pipelines is one, and the sensor is a photoelectric sensor. figure 1 and figure 2 A schematic diagram of a composition structure and a schematic diagram of a control circuit corresponding to this embodiment are given respectively. The specific sequential work flow of "a rapid resin infiltration molding process system based on material flow front peak monitoring" of the present invention can be described as: when the rubber material starts to infiltrate, click the start button, and the solenoid valve on the feed pipeline in the sequential start and stop process The electromagnetic valve A on A and the intermediate pipeline is energized, and the intermediate pipeline is opened. When the photoelectric sensor installed on the intermediate pipeline detects that the material flow reaches the monitoring position, after a control signal is sent out, the solenoid valve A on the feed pipeline is closed, and the solenoid valve B on the inte...
Embodiment 2
[0076] The photoelectric sensor installed on the pipeline in "A Rapid Resin Infiltration Molding Process Based on Front Peak Monitoring of Material Flow" in this embodiment works based on the working principle of refraction and reflection of transmitted light. The working principle of refraction and reflection of transmitted light is as follows image 3 shown. When there is no glue in the transparent pipeline, the light emitted by the photoelectric sensor transmitting end T is refracted four times through the interface between the air and the pipe wall, and then received by the receiving end R, see image 3 (a); when a material with high light transmittance passes through, the light emitted from the emitting end T of the photoelectric sensor is also refracted four times through the interface between the air and the pipe wall, but because the material replaces the air in the rubber pipeline, resulting in The refractive index changes, and the light that finally passes through th...
Embodiment 3
[0078] In this example, based on the "rapid resin infiltration molding process based on material flow front peak monitoring" of the present invention, an epoxy resin-based thermosetting composite material plate with a size of 23cm×18cm and 10 layers of glass fiber cloth was prepared.
[0079] (1) Prefabricated mold: first apply a layer of release agent on the bottom surface of the mold cavity, cut the glass fiber into a size of 23cm×18cm, and lay it flat on the middle of the bottom surface of the mold cavity, laying 10 layers in total, and lay it on a top Tape the corners on the bottom of the mold cavity to facilitate subsequent demoulding; cut the release cloth into a size of 23cm×18cm, and lay it flat on top of the glass fiber, laying a total of 1 layer; cut the diversion net into 23cm×18cm Size, spread on the top of the release cloth, lay a total of 1 layer, and stick it to the bottom surface with tape at the four top corners; stick the sealant to the bottom surface to form ...
PUM
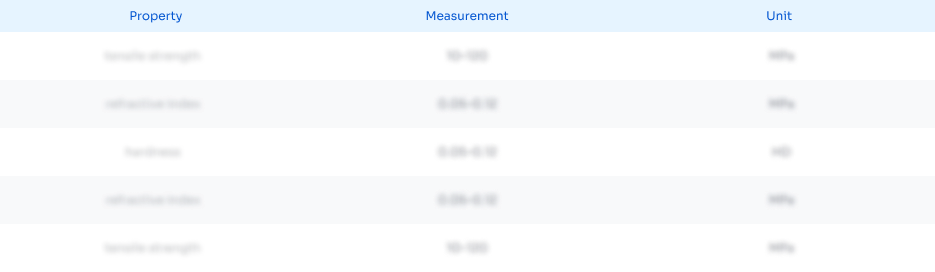
Abstract
Description
Claims
Application Information

- Generate Ideas
- Intellectual Property
- Life Sciences
- Materials
- Tech Scout
- Unparalleled Data Quality
- Higher Quality Content
- 60% Fewer Hallucinations
Browse by: Latest US Patents, China's latest patents, Technical Efficacy Thesaurus, Application Domain, Technology Topic, Popular Technical Reports.
© 2025 PatSnap. All rights reserved.Legal|Privacy policy|Modern Slavery Act Transparency Statement|Sitemap|About US| Contact US: help@patsnap.com