Composite catalyst based on denitration and demercuration reinforcing function of prepositive SCO smoke of coal-fired power plant and preparation method thereof
A technology for composite catalysts and coal-fired power plants, applied in physical/chemical process catalysts, chemical instruments and methods, separation methods, etc., can solve the problems of reduced oxidation efficiency and uneconomical conditions, and achieve enhanced oxygen storage performance, reliable performance, and high efficiency Effect of Hg Oxidation Removal Efficiency
- Summary
- Abstract
- Description
- Claims
- Application Information
AI Technical Summary
Problems solved by technology
Method used
Image
Examples
Embodiment 1
[0039] (1) Evenly mix 4.5ml of deionized water and 90ml of absolute ethanol, add 1.1g of cerium nitrate Ce(NO 3 ) 3 ·6H 2 O, fully stirred to obtain solution A; 22ml of butyl titanate was added to 88 parts by volume of absolute ethanol and uniformly mixed to obtain solution B. Add solution A to solution B dropwise, add 0.5ml of glacial acetic acid dropwise, and keep stirring for 2 hours to obtain a brown-yellow sol;
[0040] (2) Place the sol obtained in step (1) to age naturally for 36 hours at room temperature (to form a gel);
[0041] (3) Dry the gel obtained in step (2) at 80°C for 28 hours, and grind it properly to obtain a light yellow powder with an average particle size of <0.5mm;
[0042] (4) Put the light yellow powder obtained in step (3) in a temperature-programmed muffle furnace, control the heating rate to 4°C / min, and the air flow rate to 50ml / min, and roast it at the end temperature of 500°C for 1h, and cool to room temperature;
[0043] (5) Sieve the calc...
Embodiment 2
[0050] (1) Evenly mix 4.5ml of deionized water and 90ml of absolute ethanol, add 1.4g of cerium nitrate Ce(NO 3 ) 3 ·6H 2 O, fully stirred to obtain solution A; 22ml of butyl titanate was added to 88 parts by volume of absolute ethanol and uniformly mixed to obtain solution B. Add solution A to solution B dropwise, add 0.5ml of glacial acetic acid dropwise, and keep stirring for 2.5h to obtain a brown-yellow sol;
[0051] (2) Place the sol obtained in step (1) at room temperature for natural aging for 40 hours (to form a gel);
[0052] (3) Dry the gel obtained in step (2) at 85°C for 24 hours, and grind it properly to obtain a light yellow powder with an average particle size of <0.5mm;
[0053] (4) Put the light yellow powder obtained in step (3) in a temperature-programmed muffle furnace, control the heating rate to 4°C / min, and the air flow rate to 50ml / min, and roast at the end temperature of 500°C for 1.5h, and cool to room temperature;
[0054] (5) Sieve the calcine...
Embodiment 3
[0061] (1) Evenly mix 4.5ml of deionized water and 90ml of absolute ethanol, add 1.7g of cerium nitrate Ce(NO 3 ) 3 ·6H 2 O, fully stirred to obtain solution A; 22ml of butyl titanate was added to 88 parts by volume of absolute ethanol and uniformly mixed to obtain solution B. Add solution A to solution B dropwise, add 0.5ml of glacial acetic acid dropwise, and keep stirring for 3 hours to obtain a brown-yellow sol;
[0062] (2) Place the sol obtained in step (1) at room temperature for natural aging for 48 hours (to form a gel);
[0063] (3) Dry the gel obtained in step (2) at 90°C for 20 hours, and grind it properly to obtain a light yellow powder with an average particle size of <0.5mm;
[0064] (4) Put the light yellow powder obtained in step (3) in a temperature-programmed muffle furnace, control the heating rate to 4°C / min, and the air flow rate to 50ml / min, and roast at the end temperature of 500°C for 2 hours, and cool to room temperature;
[0065] (5) Sieve the c...
PUM
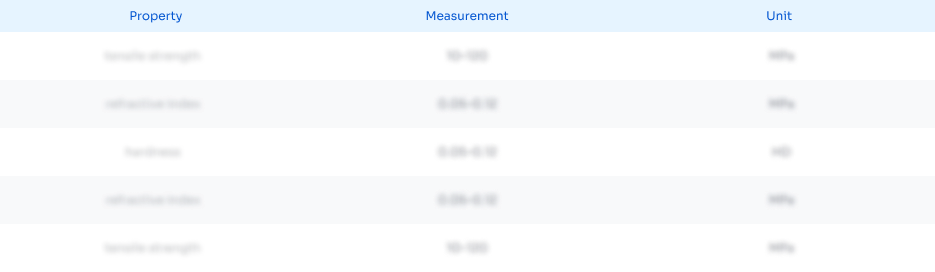
Abstract
Description
Claims
Application Information

- R&D Engineer
- R&D Manager
- IP Professional
- Industry Leading Data Capabilities
- Powerful AI technology
- Patent DNA Extraction
Browse by: Latest US Patents, China's latest patents, Technical Efficacy Thesaurus, Application Domain, Technology Topic, Popular Technical Reports.
© 2024 PatSnap. All rights reserved.Legal|Privacy policy|Modern Slavery Act Transparency Statement|Sitemap|About US| Contact US: help@patsnap.com