Preparation method of mineral printing paste
A technology of printing paste and minerals, applied in dyeing, textiles and papermaking, etc., can solve problems such as insufficient color yield of printing paste, high color yield of printing paste, rough hand feeling of printed products, etc., and achieve good suspension Stability, soft touch, rich color effect
- Summary
- Abstract
- Description
- Claims
- Application Information
AI Technical Summary
Problems solved by technology
Method used
Examples
example 1
[0019] First weigh 15g of yeast powder, pour it into a mortar and grind it for 3 minutes, then pour it into a beaker filled with 100mL of warm water at 30°C, stir and mix it with a glass rod for 1 minute, and let it stand for 10 minutes to obtain an activated yeast liquid; then weigh 600g of bentonite in turn, Add 500g of flour into a plastic basin filled with 400mL of deionized water, then add the above-mentioned activated yeast liquid, knead manually to form a dough, keep it airtight for 4 hours, then transfer the dough to a steamer, and steam at 90°C After making for 15 minutes, the expanded dough was obtained, which was then transferred to an oven, and dried to constant weight at 105°C, and then the dried expanded dough was transferred to a pulverizer, crushed and passed through an 80-mesh sieve to obtain a mixed white powder; Weigh 600g of the above-mentioned mixed white powder, place it in a muffle furnace, feed nitrogen gas into the furnace at a rate of 3mL / min, and grad...
example 2
[0022] First weigh 18g of yeast powder, pour it into a mortar and grind for 4 minutes, then pour it into a beaker filled with 110mL of warm water at 35°C, stir and mix with a glass rod for 2 minutes, and let it stand for 13 minutes to obtain activated yeast liquid; then weigh 700g of bentonite in turn, Add 550g of flour into a plastic basin filled with 450mL of deionized water, then add the above-mentioned activated yeast liquid, knead manually to form a dough, keep it sealed for 5 hours, then transfer the dough to a steamer, and steam at 93°C After making for 18 minutes, the expanded dough was obtained, which was then transferred to an oven, and dried to constant weight at 108°C, and then the dried expanded dough was transferred to a pulverizer, crushed and passed through a 100-mesh sieve to obtain a mixed white powder; Weigh 700g of the above-mentioned mixed white powder, place it in a muffle furnace, feed nitrogen into the furnace at a rate of 4mL / min, and gradually raise th...
example 3
[0025] First weigh 20g of yeast powder, pour it into a mortar and grind it for 5 minutes, then pour it into a beaker filled with 120mL of warm water at 40°C, stir and mix with a glass rod for 3 minutes, and let it stand for 15 minutes to obtain activated yeast liquid; then weigh 800g of bentonite in turn, Add 600g of flour into a plastic basin filled with 500mL of deionized water, then add the above-mentioned activated yeast liquid, knead manually to form a dough, keep it airtight for 6 hours, then transfer the dough to a steamer, and steam at 95°C Prepare for 20 minutes to obtain the expanded dough, then transfer it to an oven, and dry it to constant weight at 110°C, then transfer the dried expanded dough to a pulverizer, pass through a 120-mesh sieve after crushing, and obtain a mixed white powder; then Weigh 800g of the above-mentioned mixed white powder, place it in a muffle furnace, feed nitrogen gas into the furnace at a rate of 5mL / min, and gradually raise the temperatur...
PUM
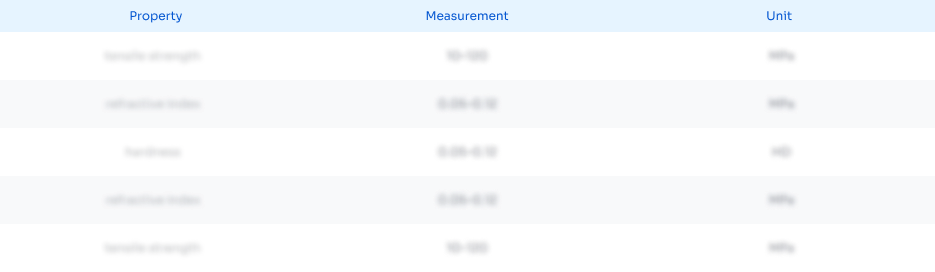
Abstract
Description
Claims
Application Information

- Generate Ideas
- Intellectual Property
- Life Sciences
- Materials
- Tech Scout
- Unparalleled Data Quality
- Higher Quality Content
- 60% Fewer Hallucinations
Browse by: Latest US Patents, China's latest patents, Technical Efficacy Thesaurus, Application Domain, Technology Topic, Popular Technical Reports.
© 2025 PatSnap. All rights reserved.Legal|Privacy policy|Modern Slavery Act Transparency Statement|Sitemap|About US| Contact US: help@patsnap.com