A kind of multi-material composite 3D printer and its working method and application
A 3D printer and working method technology, applied in the field of additive manufacturing, can solve the problems of low printing resolution, low mixing efficiency, and difficulty in printing multiple materials, achieve a wide range of printing materials, solve low circuit resolution, and print droplets. Small diameter effect
- Summary
- Abstract
- Description
- Claims
- Application Information
AI Technical Summary
Problems solved by technology
Method used
Image
Examples
Embodiment 1
[0055] like figure 1 As shown, the multi-material composite 3D printer includes: base 1, x-y workbench 2, print bed 3, first nozzle 4, second nozzle 5, third nozzle 6, z-direction worktable 1 7, z-direction workbench II 8, z direction workbench III 9, high voltage power supply 10, UV curing light source 11, frame 12, pressure pipeline 13. The base 1 is placed at the bottom; the x-y workbench 2 is placed on the base 1; the printing bed 3 is fixed on the x-y workbench 2; the first nozzle 4 is placed directly above the print bed 3 and is in phase with the z-direction workbench I 7 Connection; the z-direction workbench I 7 is fixed on the beam 1201 of the frame 12; the second nozzle 5 is placed above the printing bed 3 and connected with the z-direction workbench II 8; the z-direction workbench II 8 is fixed on the frame 12 on the beam 1201; the third nozzle 6 is placed above the print bed 3 and connected with the z-direction workbench III 9; the z-direction workbench III 9 is fi...
Embodiment 2
[0069] The working method of multi-material composite 3D printer comprises the following steps:
[0070] Step 1: Utilize the first shower head 4 and / or the third shower head 6 to print the base layer (bottom layer) and the structural layer;
[0071] Step 2: When it is necessary to print a circuit (functional layer), start the second nozzle 5 to print a specific circuit (functional layer) on the structural layer;
[0072] Step 3: If the object to be printed is a single-layer structure, go directly to step 4; if it is a multi-layer structure, repeat steps 1 and 2 until the last layer of circuit printing is printed;
[0073] Step 4: Print the topmost structure by using the first spray head 4 and / or the third spray head 6, and complete the printing of the final packaging structure.
[0074] When printing the circuit in step 3, the pause function can also be used to embed electronic components such as sensors, antennas, batteries, and LEDs.
[0075] For the second spray head 5, a...
Embodiment 3
[0079] like image 3 As shown, the multi-material composite 3D printer includes: base 1, x-y workbench 2, print bed 3, first nozzle 4, second nozzle 5, third nozzle 6, z-direction worktable 1 7, z-direction workbench II 8, z direction workbench III 9, high voltage power supply 10, UV curing light source 11, frame 12, pressure pipeline 13, fixed workbench 14. The base 1 is placed at the bottom; the x-y table 2 is placed on the base 1; the printing bed 3 is fixed on the fixed table 14; the fixed table 14 is placed on the base 1; the first nozzle 4 is placed directly above the printing bed 3 , and connected with the z-direction workbench I 7; the z-direction worktable I 7 is fixed on the beam 1201 of the frame 12; the second nozzle 5 is placed above the printing bed 3 and connected with the z-direction workbench II 8; The z-direction workbench II 8 is fixed on the beam 1201 of the frame 12; the third nozzle 6 is placed above the printing bed 3 and connected with the z-direction ...
PUM
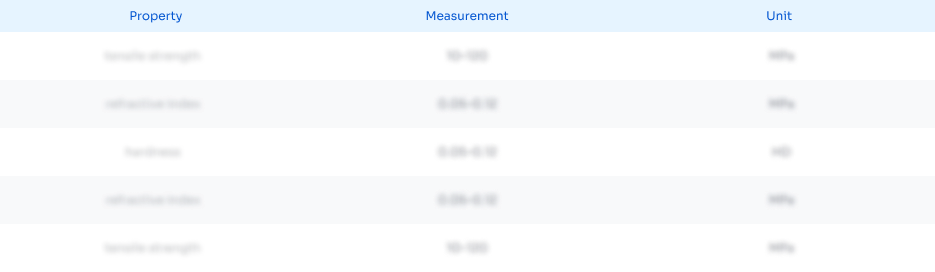
Abstract
Description
Claims
Application Information

- R&D
- Intellectual Property
- Life Sciences
- Materials
- Tech Scout
- Unparalleled Data Quality
- Higher Quality Content
- 60% Fewer Hallucinations
Browse by: Latest US Patents, China's latest patents, Technical Efficacy Thesaurus, Application Domain, Technology Topic, Popular Technical Reports.
© 2025 PatSnap. All rights reserved.Legal|Privacy policy|Modern Slavery Act Transparency Statement|Sitemap|About US| Contact US: help@patsnap.com