Composite packaging material and preparation method thereof
A technology of composite packaging materials and raw materials, applied in the field of composite packaging materials and their preparation, can solve the problems of packaging materials not meeting the requirements of use, deformation, and related mechanical properties reduction, and achieve high fracture resistance and tear resistance, The effect of high temperature resistance and simple preparation method
- Summary
- Abstract
- Description
- Claims
- Application Information
AI Technical Summary
Problems solved by technology
Method used
Examples
Embodiment 1
[0019] A composite packaging material, which is made of the following raw materials in parts by weight: 13 parts of sodium polyacrylate, 11 parts of polyacrylamide, 10 parts of hydroxyanisole, 7 parts of triallylamine, 8 parts of polylactic acid, poly 7 parts of caprolactone, 15 parts of polycarbonate, 20 parts of polyvinyl chloride, 11 parts of sodium carboxymethyl starch, 15 parts of polybutene, 5 parts of methyl silicone resin, 8 parts of chloroether resin, 0.6 parts of sodium tripolyphosphate Parts, 1.8 parts of blowing agent, 11 parts of isopropanol.
[0020] The preparation method of described composite packaging material, comprises the following steps:
[0021] (1) Take sodium polyacrylate, polyacrylamide, hydroxyanisole, triallylamine, polylactic acid, polycaprolactone, polycarbonate, polyvinyl chloride, chloroether resin, hair Foaming agent and isopropanol, put the above raw material components into the reaction kettle, heat and stir evenly;
[0022] (2) Take sodium...
Embodiment 2
[0027] A composite packaging material, which is made of the following raw materials in parts by weight: 15 parts of sodium polyacrylate, 10 parts of polyacrylamide, 11 parts of hydroxyanisole, 5 parts of triallylamine, 5 parts of polylactic acid, poly 8 parts of caprolactone, 14 parts of polycarbonate, 24 parts of polyvinyl chloride, 8 parts of sodium carboxymethyl starch, 17 parts of polybutene, 6 parts of methyl silicone resin, 9 parts of chloroether resin, 0.8 parts of sodium tripolyphosphate Parts, 1.5 parts of blowing agent, 10 parts of isopropanol.
[0028] The preparation method of described composite packaging material, comprises the following steps:
[0029] (1) Take sodium polyacrylate, polyacrylamide, hydroxyanisole, triallylamine, polylactic acid, polycaprolactone, polycarbonate, polyvinyl chloride, chloroether resin, hair Foaming agent and isopropanol, put the above raw material components into the reaction kettle, heat and stir evenly;
[0030] (2) Take sodium ...
Embodiment 3
[0035] A composite packaging material, which is made of the following raw materials in parts by weight: 10 parts of sodium polyacrylate, 10 parts of polyacrylamide, 8 parts of hydroxyanisole, 7 parts of triallylamine, 6 parts of polylactic acid, poly 8 parts of caprolactone, 13 parts of polycarbonate, 22 parts of polyvinyl chloride, 9 parts of sodium carboxymethyl starch, 16 parts of polybutene, 5 parts of methyl silicone resin, 9 parts of chloroether resin, 0.8 parts of sodium tripolyphosphate Parts, 1.5 parts of blowing agent, 12 parts of isopropanol.
[0036] The preparation method of described composite packaging material, comprises the following steps:
[0037] (1) Take sodium polyacrylate, polyacrylamide, hydroxyanisole, triallylamine, polylactic acid, polycaprolactone, polycarbonate, polyvinyl chloride, chloroether resin, hair Foaming agent and isopropanol, put the above raw material components into the reaction kettle, heat and stir evenly;
[0038] (2) Take sodium c...
PUM
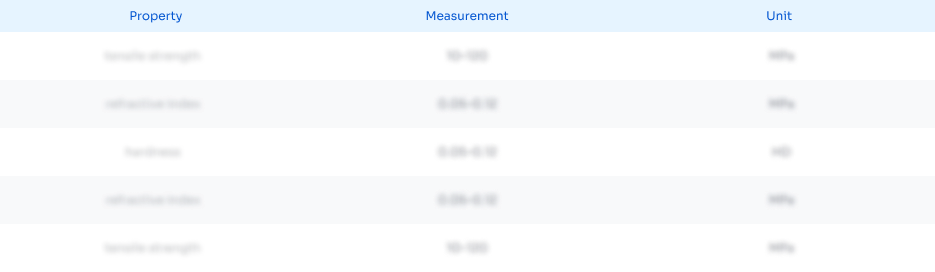
Abstract
Description
Claims
Application Information

- R&D
- Intellectual Property
- Life Sciences
- Materials
- Tech Scout
- Unparalleled Data Quality
- Higher Quality Content
- 60% Fewer Hallucinations
Browse by: Latest US Patents, China's latest patents, Technical Efficacy Thesaurus, Application Domain, Technology Topic, Popular Technical Reports.
© 2025 PatSnap. All rights reserved.Legal|Privacy policy|Modern Slavery Act Transparency Statement|Sitemap|About US| Contact US: help@patsnap.com