Casting technology for ductile iron box body
A casting process and box body technology, which is applied in the field of ductile iron box casting technology, can solve the problems of production efficiency, casting quality and production cost, difficulty in solving casting defects, and complex box structure, etc. To achieve the effect of dense structure, clear outline and large heat transfer coefficient
- Summary
- Abstract
- Description
- Claims
- Application Information
AI Technical Summary
Problems solved by technology
Method used
Examples
Embodiment Construction
[0016] In order to make the object, technical solution and advantages of the present invention clearer, the following examples are further detailed descriptions of the present invention.
[0017] An embodiment of the present invention is a casting process for a nodular iron box. The process steps include preparing coated sand, making an outer mold and clay core, molding, melting, pouring and sand cleaning.
[0018] The first step is to prepare coated sand: use raw sand as the main raw material, thermoplastic phenolic resin, urotropine solution, alkane coupling agent and calcium stearate as additives, and mix the raw sand and additives through a coated sand mixer Prepare the coated sand, wherein, in the prepared coated sand, the original sand is 100Kg, the thermoplastic phenolic resin is 3% (accounting for the original sand weight), and the urotropine solution is 1.8%-2.5% (accounting for the original sand weight). sand weight), alkane coupling agent is 0.15%-0.18% (accounting ...
PUM
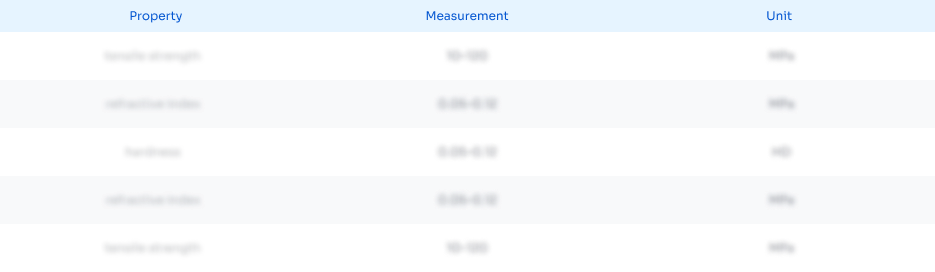
Abstract
Description
Claims
Application Information

- R&D
- Intellectual Property
- Life Sciences
- Materials
- Tech Scout
- Unparalleled Data Quality
- Higher Quality Content
- 60% Fewer Hallucinations
Browse by: Latest US Patents, China's latest patents, Technical Efficacy Thesaurus, Application Domain, Technology Topic, Popular Technical Reports.
© 2025 PatSnap. All rights reserved.Legal|Privacy policy|Modern Slavery Act Transparency Statement|Sitemap|About US| Contact US: help@patsnap.com