Hub forging method
A hub forging and final forging technology, applied in the field of forging, can solve the problems of increasing process time, waste of raw materials, long processing time, etc., and achieve the effects of reducing heating space, saving energy consumption, good product quality and performance improvement
- Summary
- Abstract
- Description
- Claims
- Application Information
AI Technical Summary
Problems solved by technology
Method used
Image
Examples
Embodiment 1
[0037] Example 1, a method for forging a wheel hub, see attached figure 1 It is mainly divided into the major steps of material preparation, forging, spinning, heat treatment and machining. Based on a 17-inch aluminum alloy wheel hub, the 65mm thick 7A04 aluminum alloy extruded sheet is hot-cut to a size of 350mm ×350mm×65mm square blank;
[0038] The material preparation stage is a continuous production process in this embodiment, a. After the aluminum rod is melted and cast, an extruder is used to extrude an aluminum alloy sheet of 350mm×65mm; b. The extruded aluminum alloy sheet is delivered online for preheating The furnace is heated to 440°C and preheated for 30 minutes; c. One end of the preheated aluminum alloy sheet from the furnace is pressed against the holding mechanism, and the hydraulic cutter at the exit of the furnace directly directly affects the preheated aluminum alloy. Perform on-line hot cutting, and the cut blank will directly fall into the lower feeding chu...
Embodiment 2
[0042] Example 2, a method for forging a wheel hub, see attached figure 1 It is mainly divided into the major steps of material preparation, forging, spinning, heat treatment and machining. Based on a 17-inch aluminum alloy wheel hub, the 65mm thick 6061 aluminum alloy extruded sheet is hot cut into a size of 350mm ×350mm×65mm square blank;
[0043] The material preparation stage is a continuous production process in this embodiment, a. After the aluminum rod is melted and cast, an extruder is used to extrude an aluminum alloy sheet of 350mm×65mm; b. The extruded aluminum alloy sheet is delivered online for preheating The furnace is heated to 470℃, and the preheat treatment is 40 minutes; c. One end of the preheated aluminum alloy sheet from the furnace is pressed on the support mechanism, and the hydraulic cutter at the exit of the furnace directly affects the preheated aluminum alloy. Perform on-line hot cutting, and the cut blank will directly fall into the lower feeding chut...
Embodiment 3
[0047] Example 3, a method for forging a wheel hub, see attached figure 1 It is mainly divided into the major steps of material preparation, forging, spinning, heat treatment and machining. Based on a 17-inch aluminum alloy wheel hub, the 6061 aluminum alloy extruded sheet with a thickness of 58mm is hot cut into a size of 370mm ×370mm×58mm square blank;
[0048] The material preparation stage is a continuous production process in this embodiment, a. After the aluminum rod is melted and cast, an extruder is used to extrude an aluminum alloy sheet of 370mm×58mm; b. The extruded aluminum alloy sheet is sent online for preheating The furnace is heated to 450°C and preheated for 40 minutes; c. One end of the preheated aluminum alloy sheet from the furnace is placed on the support mechanism, and the hydraulic cutter at the exit of the furnace directly directly affects the preheated aluminum alloy. Perform on-line hot cutting, and the cut blank will directly fall into the lower feedin...
PUM
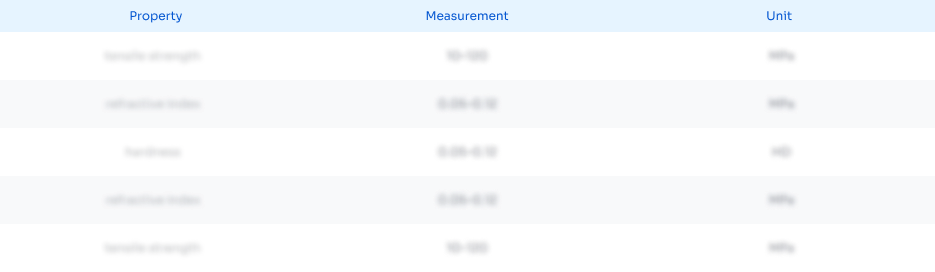
Abstract
Description
Claims
Application Information

- R&D
- Intellectual Property
- Life Sciences
- Materials
- Tech Scout
- Unparalleled Data Quality
- Higher Quality Content
- 60% Fewer Hallucinations
Browse by: Latest US Patents, China's latest patents, Technical Efficacy Thesaurus, Application Domain, Technology Topic, Popular Technical Reports.
© 2025 PatSnap. All rights reserved.Legal|Privacy policy|Modern Slavery Act Transparency Statement|Sitemap|About US| Contact US: help@patsnap.com