Method for preparing solidified bodies on basis of cesium-adsorbed silicon-based heteropolyacid salt composite adsorbents
A composite adsorption and heteropolyacid technology, applied in radioactive purification, nuclear engineering and other directions, can solve the problems of poor compatibility of phosphorus elements, limit the practical application of heteropolyacid salt inorganic adsorbents, etc., and achieve high fixation rate and good adsorption. And capture ability, anti-leaching performance superior effect
- Summary
- Abstract
- Description
- Claims
- Application Information
AI Technical Summary
Problems solved by technology
Method used
Image
Examples
Embodiment 1
[0021] The silicon-based ammonium phosphomolybdate composite adsorbent after adsorbing cesium and allophane (main component: SiO 2 78.78%, Al 2 o 3 12.39%, Fe 2 o 3 3.51%, K 2 O 1.64%, Na 2 O 0.48%) were ground and mixed at a mass ratio of 1:0.5, 1:2, and 1:4, and then placed in a cylindrical abrasive tool and pressed at 40Mpa, and then sintered at 800°C in a high-temperature muffle furnace. Hours, annealed to room temperature to obtain a ceramic solidified body.
[0022] figure 1 It is the X-ray diffraction pattern of the cesium-containing ceramic solidified body sintered under the conditions of different proportions of the samples of this embodiment. Depend on figure 1 It can be seen that after sintering at 800 degrees, the structure of ammonium phosphomolybdate has collapsed, forming stable cesium aluminum silicate (PDF: 41-0569), aluminosilicate (PDF: 15-0776) and silicon dioxide ( PDF: 39-1425) mixed crystals, as the proportion of allophane increases, the inte...
Embodiment 2
[0024] The silica-based ammonium molybdate composite adsorbent after adsorbing cesium and allophane (main component: SiO 2 78.78%, Al 2 o 3 12.39%, Fe 2 o 3 3.51%, K 2 O 1.64%, Na 2 O 0.48%) with a mass ratio of 1:1 to grind and mix evenly, place it in a cylindrical abrasive tool and press it at 45Mpa, then sinter in a high-temperature muffle furnace at 900, 1000, and 1200 degrees for 2 hours, and anneal After reaching room temperature, a ceramic solidified body is obtained. Cured body X-ray diffraction pattern and figure 1 Similarities are no longer listed. After sintering at 900 degrees, the structure of ammonium phosphomolybdate has collapsed, forming a stable cesium aluminum silicate, aluminosilicate and silicon dioxide mixed crystals. After sintering at 1000 and 1200 degrees, the intensity of diffraction peaks increases, the degree of crystallinity is higher, and a more complete mixed crystalline substance is formed. X-ray fluorescence analysis was carried out ...
Embodiment 3
[0026] The silicon-based ammonium phosphotungstate composite adsorbent after adsorbing cesium and natural mordenite (main component: SiO 2 81.31%, Al 2 o 3 12.51%, Fe2 o 3 1.96%, K 2 O 1.25%, Na 2 O 0.65%) with a mass ratio of 1:0.8, 1:1.5, 1:2.5 to grind and mix evenly, place it in a cylindrical abrasive tool and press it at 50Mpa, and then sinter it in a high-temperature muffle furnace at 1300 degrees. Hours, annealed to room temperature to obtain a ceramic solidified body.
[0027] figure 2 It is the X-ray diffraction pattern of the cesium-containing ceramic solidified body sintered under different ratio conditions for the sample of this embodiment. Depend on figure 2 It can be seen that after sintering at 1300 degrees, the structure of ammonium phosphotungstate has collapsed, forming stable cesium aluminosilicate crystals (PDF: 41-0569) and crystalline silicon dioxide (PDF: 39-1425) Mixed crystal ceramic solidified body. X-ray fluorescence analysis was carried...
PUM
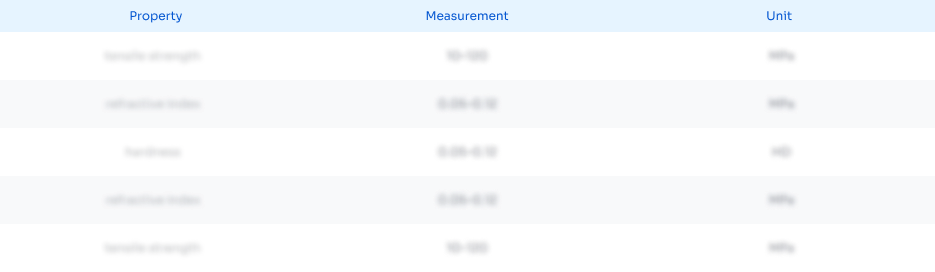
Abstract
Description
Claims
Application Information

- R&D
- Intellectual Property
- Life Sciences
- Materials
- Tech Scout
- Unparalleled Data Quality
- Higher Quality Content
- 60% Fewer Hallucinations
Browse by: Latest US Patents, China's latest patents, Technical Efficacy Thesaurus, Application Domain, Technology Topic, Popular Technical Reports.
© 2025 PatSnap. All rights reserved.Legal|Privacy policy|Modern Slavery Act Transparency Statement|Sitemap|About US| Contact US: help@patsnap.com