Processing method of marble polypropylene composite slab and composite slab prepared by method
A processing method and marble slab technology, applied in the field of building decoration and decoration materials, can solve the problems of high price, unreusable tiles, and failure to meet the requirements of use, and achieve the effect of low cost
- Summary
- Abstract
- Description
- Claims
- Application Information
AI Technical Summary
Problems solved by technology
Method used
Image
Examples
Embodiment 1
[0074] The concrete processing method of the present embodiment is as follows:
[0075] Preparation of pellet 1:
[0076] components
parts by weight
100
dialkyl peroxide
0.1
maleic anhydride
20
[0077] Polypropylene, peroxide compound and maleic anhydride are melt-blended to obtain a molten mixture, which is then prepared into granules to obtain Pellet 1.
[0078] Preparation of foam masterbatch:
[0079] components
parts by weight
30
15
1
monophenol
10
0.1
Azodimethylamide (AC)
30
[0080] The mixture of thermoplastic polymer, zinc oxide, zinc stearate, antioxidant, crosslinking agent and foaming agent is banburyed at 250° C. for 0.5 hour, and then prepared into granules to obtain foam masterbatch.
[0081] The above granules 1, foam masterbatch and 5 parts by weight of American S...
Embodiment 2
[0086] The concrete processing method of the present embodiment is as follows:
[0087] Preparation of pellet 1:
[0088] components
parts by weight
50
diacyl peroxide
10
maleic anhydride
1
[0089] Polypropylene, peroxide compound and maleic anhydride are melt-blended to obtain a molten mixture, which is then prepared into granules to obtain Pellet 1.
[0090] Preparation of foam masterbatch:
[0091]
[0092]
[0093] The mixture of thermoplastic polymer, zinc oxide, zinc stearate, antioxidant, crosslinking agent, foaming agent and auxiliary agent is banburyed at 80 for 4 hours, and then prepared into granules to obtain foam masterbatch.
[0094] The above granules 1, foam masterbatch and 80 parts by weight of American Santoprene TPV 111-80 were mechanically stirred evenly, and extruded and calendered at 120° C. to form a modified polypropylene board.
[0095] Processing method of marble polypropylene com...
Embodiment 3
[0099] The concrete processing method of the present embodiment is as follows:
[0100] Preparation of pellet 1:
[0101]
[0102]
[0103] Polypropylene, peroxide compound and maleic anhydride are melt-blended to obtain a molten mixture, which is then prepared into granules to obtain Pellet 1.
[0104] Preparation of foam masterbatch:
[0105] components
parts by weight
40
Zinc oxide
13
2
Quinol
9
1
Dinitrosopentamethylenetetramine
27
3
[0106] The mixture of thermoplastic polymer, zinc oxide, zinc stearate, antioxidant, crosslinking agent, foaming agent and auxiliary agent is banburyed at 230°C for 1 hour, and then prepared into granules to obtain foam masterbatch.
[0107] The above granules 1, foam masterbatch and 10 parts by weight of American Santoprene TPV 111-87 were mechanically stirred evenly, and ext...
PUM
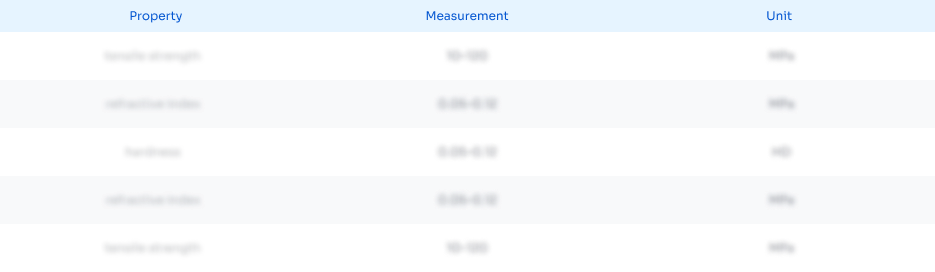
Abstract
Description
Claims
Application Information

- R&D Engineer
- R&D Manager
- IP Professional
- Industry Leading Data Capabilities
- Powerful AI technology
- Patent DNA Extraction
Browse by: Latest US Patents, China's latest patents, Technical Efficacy Thesaurus, Application Domain, Technology Topic, Popular Technical Reports.
© 2024 PatSnap. All rights reserved.Legal|Privacy policy|Modern Slavery Act Transparency Statement|Sitemap|About US| Contact US: help@patsnap.com