Grinding wheel ash hollow brick and production method thereof
A hollow brick and grinding wheel technology, applied in the field of grinding wheel ash hollow brick and its preparation, can solve the problems of poor wear resistance, waste of resources, small volume of clay solid bricks, etc. The effect of improving the hydraulic gelation activity
- Summary
- Abstract
- Description
- Claims
- Application Information
AI Technical Summary
Problems solved by technology
Method used
Examples
Embodiment 1
[0033] A grinding wheel ash hollow brick described in this embodiment is composed of the following raw materials in parts by weight: 18 parts of grinding wheel ash, 36 parts of river silt, 27 parts of cinder, 100 parts of water, 25 parts of Jiaoling stone, 37 parts of basalt, 4 parts of sawdust 2 parts, 2 parts of polystyrene grains, 3 parts of quicklime.
[0034] The preparation method of above-mentioned emery wheel ash hollow brick, comprises the following steps:
[0035] (1) Grind Jiaoling stone to 900 mesh;
[0036] (2) Mix the grinding wheel ash with the Jiaoling stone particles after step (1), seal and heat, keep the temperature at 670°C, the pressure at 4MPa, and the time for 48min;
[0037] (3) Grind polystyrene grains and quicklime to 1600 mesh respectively;
[0038] (4) The mixture after step (2) (3) is sealed and mixed with the sun-dried river silt for 2 hours, and ground to 1800 mesh;
[0039] (5) Cinder and basalt are crushed separately, and the particle size a...
Embodiment 2
[0048] A grinding wheel ash hollow brick described in this embodiment is composed of the following raw materials in parts by weight: 15 parts of grinding wheel ash, 40 parts of river silt, 25 parts of cinder, 105 parts of water, 20 parts of Jiaoling stone, 40 parts of basalt, 2 parts of sawdust Parts, 3 parts of polystyrene grains, 2 parts of quicklime.
[0049] The preparation method of above-mentioned emery wheel ash hollow brick, comprises the following steps:
[0050] (1) Grind Jiaoling stone to 1000 mesh;
[0051] (2) Mix the grinding wheel ash with the Jiaoling stone particles after step (1), seal and heat, keep the temperature at 650°C, the pressure at 6MPa, and the time for 40min;
[0052] (3) Grind polystyrene grains and quicklime to 1800 mesh respectively;
[0053] (4) The mixture after step (2) (3) is sealed and mixed with the sun-dried river silt for 2 hours, and ground to 2000 mesh;
[0054] (5) Cinder and basalt are crushed separately, and the particle size af...
Embodiment 3
[0063] A grinding wheel ash hollow brick described in this embodiment is composed of the following raw materials in parts by weight: 20 parts of grinding wheel ash, 30 parts of river silt, 30 parts of cinder, 90 parts of water, 30 parts of Jiaoling stone, 35 parts of basalt, 5 parts of sawdust 1 part, 1 part of polystyrene grain, 5 parts of quicklime.
[0064] The preparation method of above-mentioned emery wheel ash hollow brick, comprises the following steps:
[0065] (1) Grind Jiaoling stone to 800 mesh;
[0066] (2) Mix the grinding wheel ash with the Jiaoling stone particles after step (1), seal and heat, keep the temperature at 700°C, the pressure at 2MPa, and the time for 55min;
[0067] (3) Grind polystyrene grains and quicklime to 1500 mesh respectively;
[0068] (4) The mixture after step (2) (3) is sealed and mixed with the sun-dried river silt for 3 hours, and ground to 1800 mesh;
[0069] (5) Cinder and basalt are crushed separately, and the particle size after...
PUM
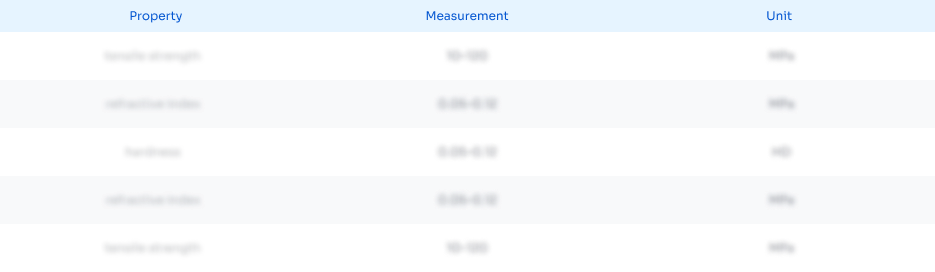
Abstract
Description
Claims
Application Information

- R&D
- Intellectual Property
- Life Sciences
- Materials
- Tech Scout
- Unparalleled Data Quality
- Higher Quality Content
- 60% Fewer Hallucinations
Browse by: Latest US Patents, China's latest patents, Technical Efficacy Thesaurus, Application Domain, Technology Topic, Popular Technical Reports.
© 2025 PatSnap. All rights reserved.Legal|Privacy policy|Modern Slavery Act Transparency Statement|Sitemap|About US| Contact US: help@patsnap.com