Boride metal ceramic coating material and preparation method
A metal-ceramic coating and metal-ceramic technology, which is applied in metal material coating process, coating, melting spraying and other directions, can solve the problems of high cost, unsuitable for mass production and use, and long preparation time.
- Summary
- Abstract
- Description
- Claims
- Application Information
AI Technical Summary
Problems solved by technology
Method used
Image
Examples
Embodiment 1
[0035] Choose commercially available micron TiB with a purity of 99.6% or more 2 , Ni, Cr powder, TiB in the powder 2 Powder, Ni powder and Cr powder weight ratio is 60wt.%: 32wt.%: 8wt.%, organic dispersant PAANH 4 The mass of the powder is 0.8%-1.2% of the mass of the mixed powder, and the mass of the organic binder polyethylene glycol is 15%-20% of the mass of the mixed powder.
[0036] The following steps are used to prepare high-performance agglomerated and sintered powders:
[0037] (1) Put the above materials into deionized water, add the mixed solution into a planetary ball mill and mix at a low speed of 200r / min for 10 hours to form a viscous slurry.
[0038](2) Prepare agglomerated spherical powder by centrifugal spray drying method. The inlet temperature of the spray drying tower is 180°C, the outlet temperature is 90°C, the rotation speed of the centrifugal spray plate is 20000r / min, and the feed rate is 0.4mL / s for constant temperature and constant speed spray ...
Embodiment 2
[0047] Choose commercially available micron TiB with a purity of 99.6% or more 2 , Ni, Cr powder, TiB in the powder 2 The weight ratio of powder, Ni powder and Cr powder is 60wt.%: 32wt.%: 8wt.%, using the powder preparation process in Example 1 to prepare agglomerated and sintered powder.
[0048] The substrate used for spraying is low carbon steel, and the surface of the substrate is derusted, degreased and sandblasted before spraying.
[0049] The spraying equipment is the JP-5000 supersonic flame spraying system produced by the British TAFA company. The main spraying process parameters are: spraying distance 380mm, oxygen flow rate 940L / min, kerosene flow rate 24.6L / h, N 2 The flow rate is 10.3L / min, and the powder feeding rate is about 40g / min. The spraying thickness is controlled at 0.25-0.5mm.
[0050] The mechanical properties of the coating prepared in Example 2 were tested. The test results are shown in Table 1.
Embodiment 3
[0052] Choose commercially available micron TiB with a purity of 99.6% or more 2 , Ni, Cr powder, TiB in the powder 2 The weight ratio of powder, Ni powder and Cr powder is 70wt.%: 24wt.%: 6wt.%, using the powder preparation process in Example 1 to prepare agglomerated and sintered powder.
[0053] The substrate used for spraying is low carbon steel, and the surface of the substrate is derusted, degreased and sandblasted before spraying.
[0054] The spraying equipment is the JP-5000 supersonic flame spraying system produced by the British TAFA company. The main spraying process parameters are: spraying distance 355mm, oxygen flow rate 870L / min, kerosene flow rate 22.7L / h, N 2 The flow rate is 10.3L / min, and the powder feeding rate is about 40g / min. The spraying thickness is controlled at 0.25-0.5mm.
[0055] The mechanical properties of the coating prepared in Example 3 were tested. The test results are shown in Table 1.
[0056] It can be seen from Table 1 that the micr...
PUM
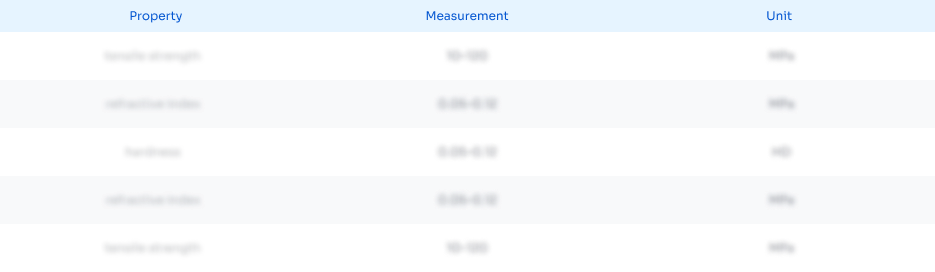
Abstract
Description
Claims
Application Information

- R&D Engineer
- R&D Manager
- IP Professional
- Industry Leading Data Capabilities
- Powerful AI technology
- Patent DNA Extraction
Browse by: Latest US Patents, China's latest patents, Technical Efficacy Thesaurus, Application Domain, Technology Topic, Popular Technical Reports.
© 2024 PatSnap. All rights reserved.Legal|Privacy policy|Modern Slavery Act Transparency Statement|Sitemap|About US| Contact US: help@patsnap.com