Non-curing rubber asphalt waterproof coating and preparation method thereof
A technology of asphalt waterproof coating and non-curing rubber, applied in asphalt coatings, recycled rubber coatings, anti-corrosion coatings, etc., can solve problems such as low tear resistance, achieve sufficient interaction, ensure creep characteristics, and reduce production costs. Effect
- Summary
- Abstract
- Description
- Claims
- Application Information
AI Technical Summary
Problems solved by technology
Method used
Image
Examples
Embodiment 1
[0030] (1) Granite powder 15g, linear low density polyethylene 13g and zinc stearate 2g were mixed and ground for 35-60 minutes;
[0031] (2) the mixture formed in (1) is screened through 80 mesh sieves, and the mixed material below 80 mesh is used for subsequent use;
[0032] (3) 60g of asphalt, 6g of waste engine oil and 4g of regenerated animal and vegetable oil are uniformly mixed under the condition of 155-165°C;
[0033] (4) Add the mixed material, rosin resin 10g, fumed white carbon black 8g, nano calcium carbonate 9g and 80 mesh fly ash powder 8g obtained in (3) to the mixture obtained in (2), and heat up to 175- 185°C and fully stirred for 35-60 minutes;
[0034] (5) Add 35g of regenerated rubber powder, 6g of mica powder, and 7g of pottery clay to the mixture in (4), stir until the mixture is cooled to room temperature, and discharge.
Embodiment 2
[0036] (1) Granite powder 12g, linear low density polyethylene 12g and zinc stearate g were mixed and ground for 35-60 minutes;
[0037] (2) the mixture formed in (1) is screened through 80 mesh sieves, and the mixed material below 80 mesh is used for subsequent use;
[0038] (3) 50g of asphalt, 4g of waste engine oil and 8g of regenerated animal and vegetable oil are uniformly mixed under the condition of 155-165°C;
[0039] (4) Add the mixed material prepared in (2), 9 g of rosin resin, 5 g of nano-calcium carbonate and 10 g of 100 mesh fly ash powder to the mixture obtained in (3), raise the temperature to 175-185 ° C and fully stir for 35 -60 minutes;
[0040] (5) Add 29g of regenerated rubber powder and 9g of pottery clay to the mixture in (4), stir until the mixture is cooled to room temperature, and discharge.
Embodiment 3
[0042] (1) Granite powder 10g, linear low density polyethylene 11g and zinc stearate 5g were mixed and ground for 35-60 minutes;
[0043] (2) the mixture formed in (1) is screened through 80 mesh sieves, and the mixed material below 80 mesh is used for subsequent use;
[0044] (3) 40g of asphalt, 8g of waste engine oil and 2g of regenerated animal and vegetable oil are uniformly mixed under the condition of 155-165°C;
[0045] (4) Add the mixed material prepared in (2), 7g of rosin resin, 7g of fumed white carbon black, and 3g of nano-calcium carbonate to the mixture obtained in (3), raise the temperature to 175-185°C and stir thoroughly for 35-60 minute;
[0046] (5) Add 23g of regenerated rubber powder and 11g of mica powder into the mixture obtained in (4), stir until the mixture is cooled to room temperature, and discharge.
PUM
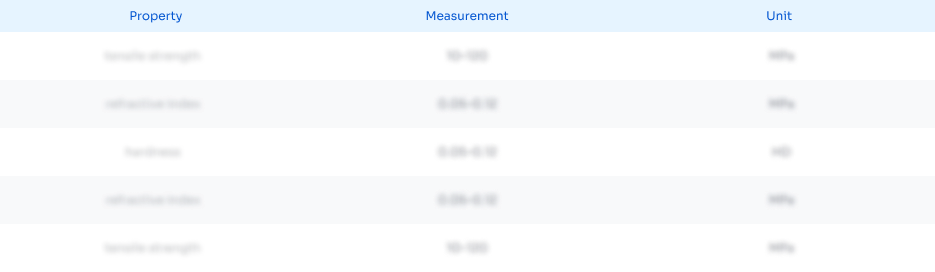
Abstract
Description
Claims
Application Information

- R&D Engineer
- R&D Manager
- IP Professional
- Industry Leading Data Capabilities
- Powerful AI technology
- Patent DNA Extraction
Browse by: Latest US Patents, China's latest patents, Technical Efficacy Thesaurus, Application Domain, Technology Topic, Popular Technical Reports.
© 2024 PatSnap. All rights reserved.Legal|Privacy policy|Modern Slavery Act Transparency Statement|Sitemap|About US| Contact US: help@patsnap.com