After-reaction processing method for preparation of diacetone-acrylamide
A technology of acetone acrylamide and acrylamide, applied in the separation/purification of carboxylic acid amide, organic chemistry and other directions, can solve the problems of reduced DAAM yield, high energy consumption, large investment, etc., to reduce the difficulty of subsequent purification, reduce decomposition, avoid The effect of investment and high cost
- Summary
- Abstract
- Description
- Claims
- Application Information
AI Technical Summary
Problems solved by technology
Method used
Image
Examples
Embodiment approach
[0039] (1) Use saturated ammonium sulfate aqueous solution to mix with the reaction mixture, feed ammonia gas to neutralize the hydrolysis mixture, separate out ammonium sulfate solid in the neutralization process, separate out ammonium sulfate solid (i.e. by-product), ammonium sulfate aqueous solution (return to Hydrolysis process recycling) and organic layer (neutralization product, ie diacetone acrylamide crude product).
[0040] (2) Use saturated ammonium sulfate aqueous solution to mix with the reaction mixture, then stand still or separate the heavy phase and the light phase with continuous chromatography. The heavy phase is neutralized with ammonia gas, and ammonium sulfate solid is precipitated during the neutralization process, and ammonium sulfate solid (i.e. by-product), ammonium sulfate aqueous solution (returned to the hydrolysis process for recycling) and organic layer are separated separately, and air can be introduced before phase separation The organic matter ...
Embodiment 1
[0048] Take 200 g of the reaction mixture obtained by reacting acrylonitrile and acetone under the action of concentrated sulfuric acid, add it into a four-neck flask with a thermometer, and start stirring. Slowly add 600 g of saturated ammonium sulfate aqueous solution into the four-neck flask, and continue stirring for 30 minutes after the addition is complete. Ammonia gas was introduced slowly, the temperature was controlled below 20°C, the pH value at the end point of neutralization was 8.5, and the stirring was continued for 30 minutes to stop. All the materials were added to the separatory funnel, and allowed to stand for 60 minutes, and the ammonium sulfate solid, ammonium sulfate aqueous solution and organic layer were separated successively. 97g of organic layer (containing water) was obtained, which contained 60g of DAAM.
Embodiment 2
[0050] Take 200 g of the reaction mixture obtained by reacting acrylonitrile and diacetone alcohol under the action of concentrated sulfuric acid, add it into a four-neck flask with a thermometer, and start stirring. Get 400g of 40% ammonium sulfate aqueous solution and add slowly into the four-necked flask, and stop stirring after adding and continuing to stir for 30 minutes. All the hydrolyzed materials were added to the separatory funnel and allowed to stand for 60 minutes. Separate the heavy phase, add it to a four-necked bottle with a thermometer, start stirring, slowly introduce ammonia gas, control the temperature below 50°C, neutralize to pH 7.5, continue stirring for 15 minutes, stop stirring, and add all the materials to the liquid funnel, put air into it for flotation for 30 minutes, let it stand for 60 minutes, separate the ammonium sulfate solid, ammonium sulfate aqueous solution and organic layer in sequence; % ammonia water, the temperature is controlled below ...
PUM
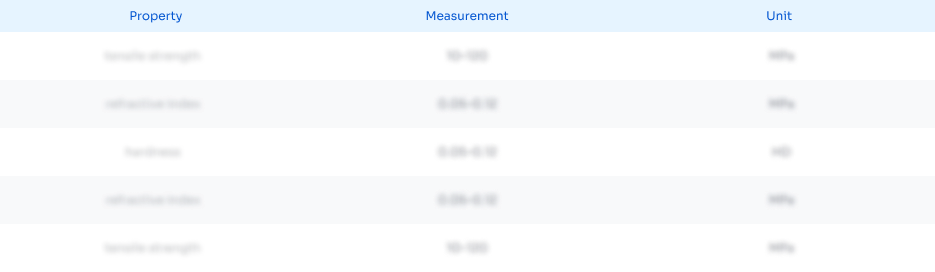
Abstract
Description
Claims
Application Information

- Generate Ideas
- Intellectual Property
- Life Sciences
- Materials
- Tech Scout
- Unparalleled Data Quality
- Higher Quality Content
- 60% Fewer Hallucinations
Browse by: Latest US Patents, China's latest patents, Technical Efficacy Thesaurus, Application Domain, Technology Topic, Popular Technical Reports.
© 2025 PatSnap. All rights reserved.Legal|Privacy policy|Modern Slavery Act Transparency Statement|Sitemap|About US| Contact US: help@patsnap.com