Process method for simultaneous production of methyl ethyl ketone by transfer hydrogenation of sec-butyl alcohol to sec-butyl acetate
A technology for transfer hydrogenation of sec-butyl acetate, applied in chemical instruments and methods, preparation of dehydrogenation, preparation of organic compounds, etc., can solve the problem that 100% conversion of sec-butyl acetate cannot be achieved, cannot be achieved, and high purity cannot be obtained Solve problems such as sec-butanol to achieve long-term stable operation, reduce severity, and maintain thermal balance
- Summary
- Abstract
- Description
- Claims
- Application Information
AI Technical Summary
Problems solved by technology
Method used
Image
Examples
Embodiment 1
[0021] Using the mixture of sec-butanol and sec-butyl acetate as raw material, wherein the molar ratio of sec-butanol and sec-butyl acetate is 1:1, fill 10g Cu-ZnO catalyst in the fixed bed reactor, the catalyst is prepared by co-precipitation method, copper The zinc atomic ratio is 1:1, the reaction temperature is 250°C, the reaction pressure is controlled at 0.0MPa (gauge pressure), and the reaction space velocity is 0.25h -1 Under certain conditions, the transfer hydrogenation of sec-butyl alcohol to sec-butyl acetate is realized, the sec-butanol is dehydrogenated to form methyl ethyl ketone, and the transfer hydrogenation of sec-butyl acetate generates sec-butanol and ethanol, and the generated sec-butanol is further dehydrogenated to form methyl ethyl ketone ; Collect the gas phase and liquid phase product of fixed bed reactor outlet respectively and carry out chromatographic analysis, and calculate the conversion ratio and the selectivity of sec-butyl acetate, sec-butanol...
Embodiment 2
[0023] Using the mixture of sec-butanol and sec-butyl acetate as raw material, wherein the molar ratio of sec-butanol and sec-butyl acetate is 1:0.8, 10g Cu-ZnO catalyst is loaded in the fixed bed reactor, and the catalyst is prepared by co-precipitation method, copper The atomic ratio of zinc is 0.5:1, the reaction temperature is 220°C, the controlled reaction pressure is 0.4MPa (gauge pressure), and the reaction space velocity is 0.5h -1 Under certain conditions, the transfer hydrogenation of sec-butyl alcohol to sec-butyl acetate is realized, the sec-butanol is dehydrogenated to form methyl ethyl ketone, and the transfer hydrogenation of sec-butyl acetate generates sec-butanol and ethanol, and the generated sec-butanol is further dehydrogenated to form methyl ethyl ketone ; Collect the gas phase and liquid phase product of fixed bed reactor outlet respectively and carry out chromatographic analysis, and calculate the conversion ratio and the selectivity of sec-butyl acetate,...
Embodiment 3
[0025] Using the mixture of sec-butanol and sec-butyl acetate as the raw material, the molar ratio of sec-butanol to sec-butyl acetate is 1:0.4, and 10g Cu / SiO is filled in the fixed bed reactor 2 Catalyst, the catalyst is prepared by impregnation method, the mass percentage of copper in the catalyst is 10%, the reaction temperature is 240°C, the controlled reaction pressure is 0.8MPa (gauge pressure), and the reaction space velocity is 1.0h -1 Under certain conditions, the transfer hydrogenation of sec-butyl alcohol to sec-butyl acetate is realized, the sec-butanol is dehydrogenated to form methyl ethyl ketone, and the transfer hydrogenation of sec-butyl acetate generates sec-butanol and ethanol, and the generated sec-butanol is further dehydrogenated to form methyl ethyl ketone ; Collect the gas phase and liquid phase product of fixed bed reactor outlet respectively and carry out chromatographic analysis, and calculate the conversion ratio and the selectivity of sec-butyl ace...
PUM
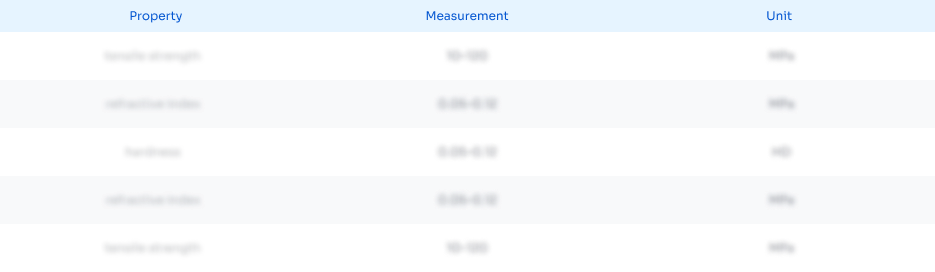
Abstract
Description
Claims
Application Information

- R&D
- Intellectual Property
- Life Sciences
- Materials
- Tech Scout
- Unparalleled Data Quality
- Higher Quality Content
- 60% Fewer Hallucinations
Browse by: Latest US Patents, China's latest patents, Technical Efficacy Thesaurus, Application Domain, Technology Topic, Popular Technical Reports.
© 2025 PatSnap. All rights reserved.Legal|Privacy policy|Modern Slavery Act Transparency Statement|Sitemap|About US| Contact US: help@patsnap.com