Transfer method of CVD method prepared graphene
A transfer method and graphene technology, which is applied in the field of graphene preparation, can solve problems such as poor square resistance uniformity and increased adhesion square resistance, and achieve the effects of increased concentration, counteracted square resistance increase, and strong high temperature resistance
- Summary
- Abstract
- Description
- Claims
- Application Information
AI Technical Summary
Problems solved by technology
Method used
Image
Examples
Embodiment 1
[0037] Direct transfer method, see flow chart figure 1 , including the following steps:
[0038] 1) Dissolving the polymer m(PVP):m(VP / VA)=5:1 in ethanol to form a mixed solution with 0.1wt% PVP and 0.02wt% VP / VA;
[0039] 2) Coating the mixed solution on the target substrate PET (commercially available, with a thickness of 150 μm), the coating method adopts the soaking and pulling method, and the coated PET is dried at 70 ° C;
[0040] 3) Attach the grown graphene / metal / graphene to the polymer surface of the target substrate, and apply a pressure of 0.2MPa at 80-150°C;
[0041] 4) Hydrochloric acid / hydrogen peroxide (also can be ammonium persulfate solution, FeCl 3 solution, sulfuric acid / hydrogen peroxide solution) etching to obtain the target product.
[0042] The square resistance of the single-layer graphene film obtained by the method of this embodiment is about 200Ω, and the adhesion force between graphene and the target substrate is about 11N / 25mm; After processing...
Embodiment 2
[0044] Adhesive film transfer method, see flow chart figure 2 , including the following steps:
[0045] 1) Dissolving the polymer m(PVP):m(VP / VA)=5:1 in ethanol to form a mixed solution with 0.1wt% PVP and 0.02wt% VP / VA;
[0046] 2) Coating the mixed solution on the target substrate PET (commercially available, with a thickness of 50 μm), the coating method is the soaking and pulling method, and the coated PET is naturally dried at room temperature;
[0047] 3) one side of the graphene of the film / graphene structure obtained in the film transfer method is attached to the polymer surface of the target substrate, and a pressure of 0.2 MPa is applied at 80-150 ° C;
[0048] 4) Remove the film to obtain the target product.
[0049] The square resistance of the single-layer graphene film obtained by the method of this embodiment is 200Ω, and the adhesion force between graphene and the target substrate is about 11N / 25mm; After treatment, the square resistance of the obtained graph...
Embodiment 3
[0051] Direct transfer method, see flow chart figure 1 , including the following steps:
[0052] 1) Dissolving the polymer m(PVP):m(VP / VA)=2:1 in ethanol to form a mixed solution with 0.8wt% PVP and 0.04wt% VP / VA;
[0053] 2) Coating the mixed solution on the surface of the target substrate. The material of the target substrate is glass (commercially available, with a thickness of 500 μm). The coating method is spin coating, and the coated glass is dried at 150° C.;
[0054] 3) Attach the grown graphene / metal / graphene or adhesive film to the polymer surface of the target substrate, and apply a pressure of 0.2MPa at 80-150°C;
[0055] 4) The target product can be obtained by etching with hydrochloric acid / hydrogen peroxide (ammonium persulfate solution, FeCl3 solution, sulfuric acid / hydrogen peroxide solution) attached to graphene / growth substrate / .
[0056] The square resistance of the graphene film obtained by the method of this embodiment is about 200Ω, and the adhesion be...
PUM
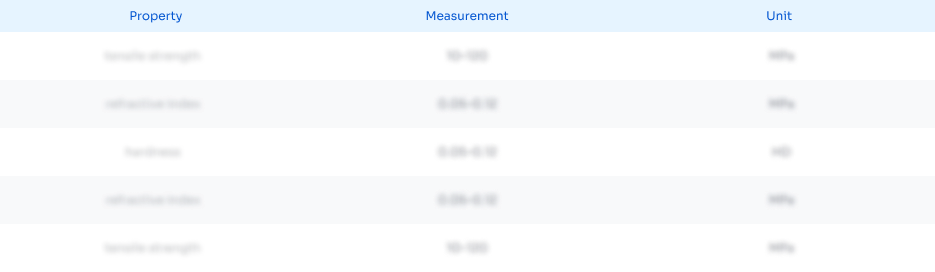
Abstract
Description
Claims
Application Information

- R&D Engineer
- R&D Manager
- IP Professional
- Industry Leading Data Capabilities
- Powerful AI technology
- Patent DNA Extraction
Browse by: Latest US Patents, China's latest patents, Technical Efficacy Thesaurus, Application Domain, Technology Topic, Popular Technical Reports.
© 2024 PatSnap. All rights reserved.Legal|Privacy policy|Modern Slavery Act Transparency Statement|Sitemap|About US| Contact US: help@patsnap.com