Multi-element alloy lining plate suitable for semi-automatic mill and machining process thereof
A semi-autogenous mill and multi-element alloy technology, applied in the direction of manufacturing tools, furnace types, furnaces, etc., can solve the problems of reduced equipment operation rate, short service life of lining board, easy fracture and wear resistance, etc., and achieve high wear resistance , high yield strength, simple operation
- Summary
- Abstract
- Description
- Claims
- Application Information
AI Technical Summary
Problems solved by technology
Method used
Image
Examples
Embodiment 1
[0032] A processing technology for a multi-element alloy liner suitable for semi-autogenous mills, including the following processes:
[0033] (a) casting molding:
[0034] The smelting molten iron temperature is 1480°C, and the pouring temperature is 1420°C. Resin self-setting sand molding process. After molding, remove the sprue to make the as-cast liner.
[0035] The molten iron includes the following components in mass percentage: 1.2% carbon, 0.45% silicon, 12.4% manganese, 1.0% chromium, 0.2% molybdenum, 0.3% vanadium, 0.1% titanium, phosphorus <0.05%, sulfur <0.03%, and the balance for iron.
[0036] The multi-element alloy liner finally prepared includes the following components in mass percentage: 1.2% carbon, 0.45% silicon, 12.4% manganese, 1.0% chromium, 0.2% molybdenum, 0.3% vanadium, 0.1% titanium, phosphorus<0.05%, sulfur< 0.03%, the balance is iron;
[0037] (b) Heat treatment of the as-cast liner: put the as-cast liner into the heat treatment furnace, rais...
Embodiment 2
[0039] A processing technology for ausferic ductile iron grinding balls suitable for semi-autogenous mills, including the following processes:
[0040] (a) casting molding:
[0041] The smelting molten iron temperature is 1470°C, and the pouring temperature is 1400°C. Resin self-setting sand molding process. After molding, remove the sprue to make the as-cast liner.
[0042]The molten iron includes the following components in mass percentage: 1.1% carbon, 0.6% silicon, 11.8% manganese, 1.2% chromium, 0.3% molybdenum, 0.45% vanadium, 0.15% titanium, phosphorus <0.05%, sulfur <0.03%, and the balance for iron.
[0043] The multi-element alloy liner finally prepared includes the following components in mass percentage: 1.1% carbon, 0.6% silicon, 11.8% manganese, 1.2% chromium, 0.3% molybdenum, 0.45% vanadium, 0.15% titanium, phosphorus<0.05%, sulfur< 0.03%, the balance is iron;
[0044] (b) Heat-treat the as-cast liner: put the as-cast liner into the heat treatment furnace, r...
Embodiment 3
[0046] A processing technology for ausferic ductile iron grinding balls suitable for semi-autogenous mills, including the following processes:
[0047] (a) casting molding:
[0048] The temperature for smelting molten iron is 1450°C, and the pouring temperature is 1380°C. Resin self-setting sand molding process. After molding, remove the sprue to make the as-cast liner.
[0049] The molten iron includes the following components in mass percentage: 1.3% carbon, 0.5% silicon, 13% manganese, 1.5% chromium, 0.3% molybdenum, 0.5% vanadium, 0.15% titanium, phosphorus <0.05%, sulfur <0.03%, and the balance for iron.
[0050] The multi-element alloy liner finally prepared includes the following components in mass percentage: 1.3% carbon, 0.5% silicon, 13% manganese, 1.5% chromium, 0.3% molybdenum, 0.5% vanadium, 0.15% titanium, phosphorus<0.05%, sulfur< 0.03%, the balance is iron;
[0051] (b) Heat treatment of the as-cast liner: put the as-cast liner into the heat treatment furn...
PUM
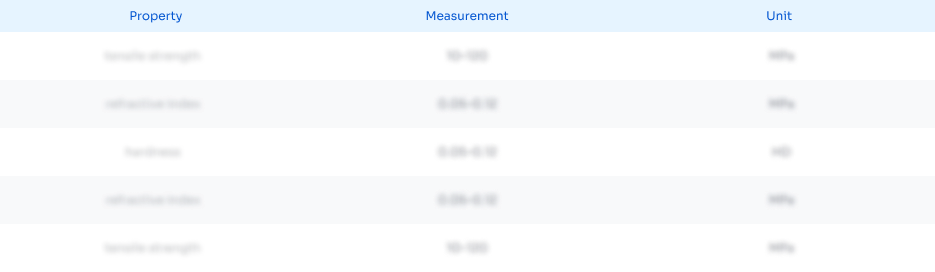
Abstract
Description
Claims
Application Information

- Generate Ideas
- Intellectual Property
- Life Sciences
- Materials
- Tech Scout
- Unparalleled Data Quality
- Higher Quality Content
- 60% Fewer Hallucinations
Browse by: Latest US Patents, China's latest patents, Technical Efficacy Thesaurus, Application Domain, Technology Topic, Popular Technical Reports.
© 2025 PatSnap. All rights reserved.Legal|Privacy policy|Modern Slavery Act Transparency Statement|Sitemap|About US| Contact US: help@patsnap.com