Ultrasonic helical hole milling device and machining method
A helical milling hole and ultrasonic technology, applied in metal processing equipment, milling machine equipment, manufacturing tools, etc., can solve the problems of hole diameter error, processing defects, etc., achieve the effect of reducing cutting force, good consistency, and ensuring real-time transmission
- Summary
- Abstract
- Description
- Claims
- Application Information
AI Technical Summary
Problems solved by technology
Method used
Image
Examples
Embodiment 1
[0074] Such as Figure 1-Figure 4 As shown, an ultrasonic helical milling device includes a main shaft support 1, an ultrasonic sleeve 2, an inner eccentric sleeve 3, an outer eccentric sleeve 4, a horn 5 and a transducer located in the ultrasonic sleeve 2 6. The horn 5 is connected with the milling cutter 8 through the collet 7,
[0075] The horn 5 is connected to the transducer 6 through an annular flange 9, and the annular flange 9 is connected to the transducer 6 through an annular force sensor 10 for measuring the axial and radial force of the annular flange 9. The inner wall of the ultrasonic sleeve 2 is connected, and the bottom of the ultrasonic sleeve 2 is provided with two concentric copper rings 11, and an electrode insulating sleeve 12 is arranged between the copper ring 11 and the ultrasonic sleeve 2. Two copper rings 11 are respectively connected with positive pole 13 and negative pole 14 of described transducer 6, and described spindle support 1 is provided wit...
Embodiment 2
[0093] Such as Figure 1-Figure 6 , a kind of ultrasonic helical milling hole processing method using a kind of ultrasonic helical milling device described in embodiment 1, has the following steps:
[0094] S1. The worm 21 moves along its axial direction to realize the adjustment of the eccentricity of the axis of the horn 5, and the eccentricity of the axis of the horn 5 satisfies the following formula:
[0095] Wherein, e is the eccentricity of the axis of the horn 5, which satisfies the formula D. 1 is the diameter of the milling cutter 8, D 2 is the diameter of the hole to be processed, e 1 is the eccentricity of the inner eccentric sleeve 3, e 2 is the eccentricity of the outer eccentric sleeve 4, and α is the relative deflection angle between the inner eccentric sleeve 3 and the outer eccentric sleeve 4;
[0096] S2, turn on the ultrasonic power supply connected to the transducer 6, and adjust the resonant frequency α of the ultrasonic helical milling device;
...
PUM
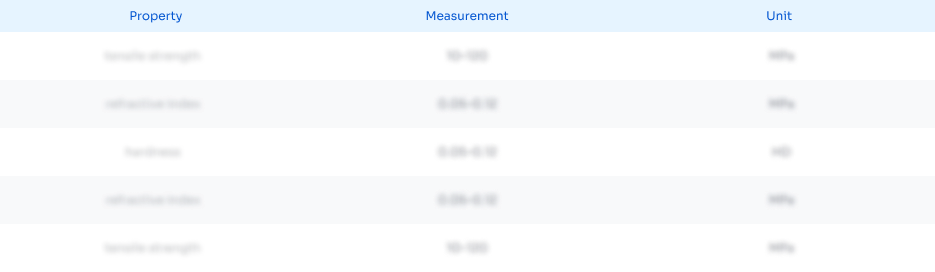
Abstract
Description
Claims
Application Information

- Generate Ideas
- Intellectual Property
- Life Sciences
- Materials
- Tech Scout
- Unparalleled Data Quality
- Higher Quality Content
- 60% Fewer Hallucinations
Browse by: Latest US Patents, China's latest patents, Technical Efficacy Thesaurus, Application Domain, Technology Topic, Popular Technical Reports.
© 2025 PatSnap. All rights reserved.Legal|Privacy policy|Modern Slavery Act Transparency Statement|Sitemap|About US| Contact US: help@patsnap.com