Manufacture process of high-strength welding wires
A manufacturing process and welding wire technology, applied in the field of welding wire manufacturing process, can solve the problems of inability to guarantee the smooth production of welding wire, high strength of semi-finished products of high-strength welding wire, and intensified work hardening of welding wire, etc. Good results
- Summary
- Abstract
- Description
- Claims
- Application Information
AI Technical Summary
Problems solved by technology
Method used
Image
Examples
Embodiment Construction
[0020] The present invention will be further described below in conjunction with the steps and the experimental data table. The high-strength welding wire manufacturing process includes welding wire smelting, off-line pickling, welding wire drawing, welding wire copper plating, welding wire layer winding, and the intermediate link of welding wire drawing is adding welding wire annealing process.
[0021] In the research on the necessity of welding wire annealing, the mold ratio used in the rough drawing and the fine drawing used in the annealing process without welding wire are shown in the attached figure 1 And attached figure 2 shown. The actual situation of the rough drawing process is recorded as: when the drawing reaches the specification of 3.85mm, the semi-finished welding wire appears shiny; when drawing to the specification of 3.55mm, the center of the welding wire cracks; more. The actual situation of the fine drawing process is recorded as: the welding wire cann...
PUM
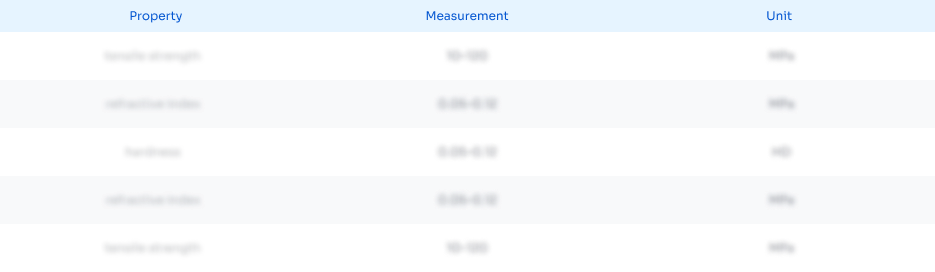
Abstract
Description
Claims
Application Information

- R&D Engineer
- R&D Manager
- IP Professional
- Industry Leading Data Capabilities
- Powerful AI technology
- Patent DNA Extraction
Browse by: Latest US Patents, China's latest patents, Technical Efficacy Thesaurus, Application Domain, Technology Topic, Popular Technical Reports.
© 2024 PatSnap. All rights reserved.Legal|Privacy policy|Modern Slavery Act Transparency Statement|Sitemap|About US| Contact US: help@patsnap.com