Lubricating oil composition for supporting roller large bearing shell of rotary kiln and preparation method thereof
A lubricating oil composition and rotary kiln technology, applied in the field of lubricating oil, can solve the problems of unfavorable heat dissipation, increased energy consumption, high oil viscosity, etc., and achieve the effects of avoiding direct contact friction, reducing the probability of heating, and high viscosity coefficient index
- Summary
- Abstract
- Description
- Claims
- Application Information
AI Technical Summary
Problems solved by technology
Method used
Image
Examples
preparation example Construction
[0040] The present invention also provides a preparation method of the lubricating oil composition of the rotary kiln supporting wheel and large tile, which comprises the following steps:
[0041] Thickener, antioxidant, metal deactivator, corrosion inhibitor and antifoaming agent are added to base oil polyalphaolefin and bright oil in sequence, heated and stirred evenly under vacuum conditions to obtain rotary kiln supporting wheel tiles lubricating oil composition.
[0042] When the additive is selected as a composite agent, the preparation method is as follows:
[0043] The compounding agent and the antifoaming agent are sequentially added to the composition formed by the base oil polyalpha-olefin, the bright oil and the thickening agent, and heated and stirred evenly under vacuum conditions to obtain the lubricating oil composition for the rotary kiln support wheel large tile.
[0044] In the present invention, the heating temperature is preferably 45°C to 130°C, more pre...
Embodiment 1~4
[0048] According to the proportioning in Table 2, the configuration of the lubricating oil composition of the rotary kiln supporting wheel and large tile is carried out, and the specific method is as follows:
[0049] Add compounding agent and anti-foaming agent to the mixture formed by base oil polyalpha-olefin, bright oil and thickener in sequence, heat and stir at 45-65°C under vacuum condition of 100-350Pa, and obtain rotary kiln supporting wheel tile Lubricating oil composition.
PUM
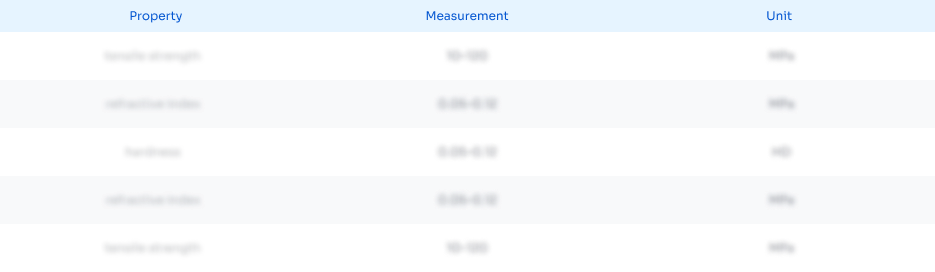
Abstract
Description
Claims
Application Information

- R&D
- Intellectual Property
- Life Sciences
- Materials
- Tech Scout
- Unparalleled Data Quality
- Higher Quality Content
- 60% Fewer Hallucinations
Browse by: Latest US Patents, China's latest patents, Technical Efficacy Thesaurus, Application Domain, Technology Topic, Popular Technical Reports.
© 2025 PatSnap. All rights reserved.Legal|Privacy policy|Modern Slavery Act Transparency Statement|Sitemap|About US| Contact US: help@patsnap.com