Self-flame-resisting type acrylic emulsion and preparation method thereof
An acrylic emulsion, flame retardant technology, used in coatings, fire retardant coatings, etc., can solve the problems of weakened flame retardant performance and uneven distribution, and achieve the effect of not easy to dissociate
- Summary
- Abstract
- Description
- Claims
- Application Information
AI Technical Summary
Problems solved by technology
Method used
Image
Examples
Embodiment 1
[0022] a. Add 30.0 parts of deionized water, 2.0 parts of sodium acrylamido isopropyl sulfonate, methyl methacrylate and 10.0 parts of butyl acrylate mixed monomer, 4.0 parts of 2,4-dibromostyrene, 2.0 parts of fluorostyrene, 1.7 parts of acrylic acid, 2.0 parts of β-hydroxyethyl acrylate, 1.05 parts of sodium bicarbonate solution; ~1300r / min high-speed stirring to emulsify to obtain milky white pre-emulsified mixed monomer emulsion;
[0023] b. When the temperature rises to 75°C, reduce the speed to 800r / min, add dropwise an aqueous solution containing 0.05 parts of ammonium persulfate, and when the temperature rises to 80°C, the reaction is initiated and blue light appears; (Note: The initiator is prepared in advance for 5 % aqueous solution)
[0024] c. When there is no reflux in the reaction, add 35.0 parts of the remaining mixed monomers and ammonium persulfate solution (containing 0.2 parts of ammonium persulfate) dropwise at the same time, keep the temperature at 81-83...
Embodiment 2
[0026] a. Add 22.0 parts of deionized water, 3.0 parts of sodium dodecylbenzenesulfonate, methyl methacrylate and acrylic acid into a four-port reaction vessel equipped with a speed-adjusting stirrer, a reflux tube, a dropping funnel and a thermometer 10.0 parts of ethyl ester mixed monomer, 5.0 parts of 2,4-difluorostyrene, 1.8 parts of acrylic acid, 2.0 parts of β-hydroxyethyl acrylate monomer, 0.18 parts of 30% sodium hydroxide; Emulsify under high-speed stirring to obtain a milky white pre-emulsified mixed monomer emulsion;
[0027] b. When the temperature rises to 75°C, reduce the speed to 800r / min, add dropwise an aqueous solution containing 0.06 parts of potassium persulfate, and when the temperature rises to 80°C, the reaction is initiated, and blue light appears; (Note: The initiator is prepared in advance for 5 % aqueous solution)
[0028] c. When there is no reflux in the reaction, add 26.0 parts of the remaining mixed monomer and the remaining potassium persulfate...
Embodiment 3
[0030] a. Add 28.0 parts of deionized water, 1.5 parts of sodium acrylamido isopropyl sulfonate, methyl methacrylate and 20.0 parts of butyl methacrylate mixed monomer, 10.0 parts of 2,4,6-tribromostyrene, 1.0 parts of acrylic acid, 1.0 parts of β-hydroxypropyl methacrylate, 1.08 parts of 30% ammonia water; Emulsify under high-speed stirring at 1300r / min to obtain a milky white pre-emulsified mixed monomer emulsion;
[0031] b. When the temperature rises to 75°C, reduce the speed to 800r / min, add dropwise an aqueous solution containing 0.1 part of sodium persulfate, and when the temperature rises to 80°C, the reaction is initiated, and blue light appears; (Note: The initiator is prepared in advance for 5 % aqueous solution)
[0032] c. When there is no reflux in the reaction, add 26.0 parts of the remaining mixed monomers and the remaining sodium persulfate solution (containing 0.4 parts of sodium persulfate) dropwise at the same time, keep the temperature at 81-83°C, and dro...
PUM
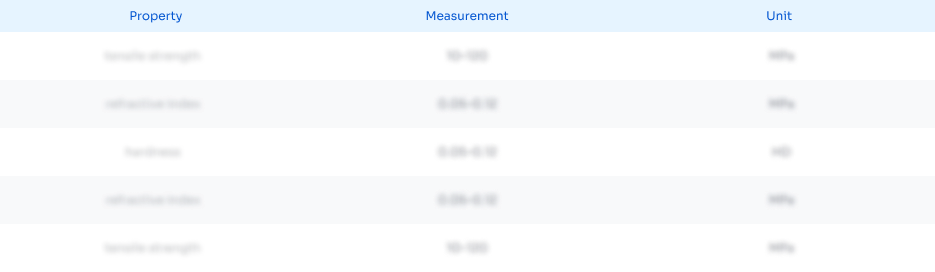
Abstract
Description
Claims
Application Information

- Generate Ideas
- Intellectual Property
- Life Sciences
- Materials
- Tech Scout
- Unparalleled Data Quality
- Higher Quality Content
- 60% Fewer Hallucinations
Browse by: Latest US Patents, China's latest patents, Technical Efficacy Thesaurus, Application Domain, Technology Topic, Popular Technical Reports.
© 2025 PatSnap. All rights reserved.Legal|Privacy policy|Modern Slavery Act Transparency Statement|Sitemap|About US| Contact US: help@patsnap.com