Preparation technique of high-purity hydroxyethyl methacrylate
The technology of hydroxyethyl methacrylate and methacrylic acid is applied in the field of preparation technology of hydroxy methacrylate, which can solve the problems of difficult handling of polymers and easy occurrence of polymerization reaction, so as to improve the polymerization inhibition effect and prevent the polymerization reaction. , to prevent the effect of violent aggregation
- Summary
- Abstract
- Description
- Claims
- Application Information
AI Technical Summary
Problems solved by technology
Method used
Image
Examples
Embodiment 1
[0029] Under vacuum conditions, 2000kg of methacrylic acid, chromium acetate with a mass fraction of 2.0%, 13×10 -4 Hydroquinone and p-hydroxyanisole, after the completion, ensure that the vacuum is 0.75Mpa, add ethylene oxide after the metering tank is replaced by nitrogen, ensure that the oxygen / nitrogen volume ratio is 0.25%, and drop it under the condition of steam heating to 80°C Add ethylene oxide, by controlling the drop rate of ethylene oxide to ensure the pressure ≤ 60KPa, the molar ratio of ethylene oxide to methacrylic acid is 1.02:1, control the reaction temperature at 90°C by cooling with cooling water, and the reaction time is 1.5 hours After the dropwise addition is completed, the cooling water is turned off and the temperature rises naturally. After the temperature drops, the sampling detection of methacrylic acid mass percentage is less than 0.5%, which is considered as the completion of the addition reaction;
[0030] Thin-film evaporator is used for weight r...
Embodiment 2
[0035] Under vacuum conditions, 2000kg of methacrylic acid, chromium acetate with a mass fraction of 5.0%, 13×10 -4 of hydroquinone and paraben and 5 x 10 -3 After completion, ensure that the vacuum is at 0.75Mpa, fill in nitrogen to ensure that the oxygen / nitrogen volume ratio is 0.25%, add ethylene oxide dropwise under the condition of steam heating to 80°C, and ensure that the pressure is ≤ 60KPa by controlling the drop rate of ethylene oxide , the molar ratio of ethylene oxide to methacrylic acid is 1.06:1, the reaction temperature is controlled at 90°C by cooling with cooling water, and the reaction time is 1.5 hours; after the addition is completed, the cooling water is turned off and the temperature rises naturally. After the temperature drops, samples are taken to detect methyl The mass percentage of acrylic acid is less than 0.5% as the addition reaction is complete;
[0036]Thin-film evaporator is used for weight removal under vacuum conditions to obtain primary dis...
Embodiment 3
[0038] Under vacuum conditions, 2000kg of methacrylic acid, chromium acetate with a mass fraction of 2.0%, 13×10 -4 of hydroquinone and paraben and 5 x 10 -3 After completion, ensure that the vacuum is at 0.75Mpa, fill in nitrogen to ensure that the oxygen / nitrogen volume ratio is 0.25%, add ethylene oxide dropwise under the condition of steam heating to 85°C, and ensure that the pressure is ≤ 60KPa by controlling the drop rate of ethylene oxide , the molar ratio of ethylene oxide to methacrylic acid is 1.02:1, the reaction temperature is controlled at 90°C by cooling with cooling water, and the reaction time is 1.5 hours; after the addition is completed, the cooling water is turned off and the temperature rises naturally. After the temperature drops, samples are taken to detect methyl The mass percentage of acrylic acid is less than 0.5% as the addition reaction is complete;
[0039] Thin-film evaporator is used for weight removal under vacuum conditions to obtain primary di...
PUM
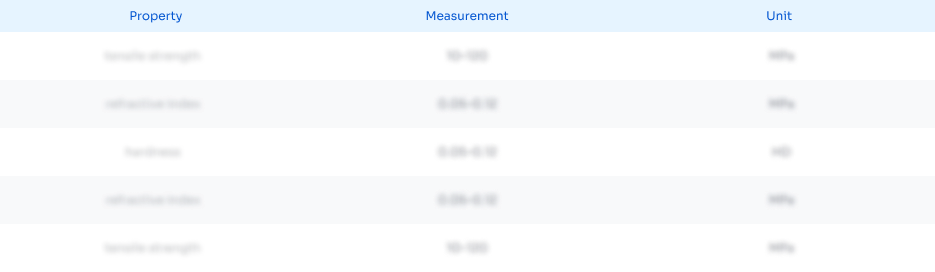
Abstract
Description
Claims
Application Information

- Generate Ideas
- Intellectual Property
- Life Sciences
- Materials
- Tech Scout
- Unparalleled Data Quality
- Higher Quality Content
- 60% Fewer Hallucinations
Browse by: Latest US Patents, China's latest patents, Technical Efficacy Thesaurus, Application Domain, Technology Topic, Popular Technical Reports.
© 2025 PatSnap. All rights reserved.Legal|Privacy policy|Modern Slavery Act Transparency Statement|Sitemap|About US| Contact US: help@patsnap.com