High-strength wear-resistant alloy brush wire and production technology thereof
A technology of wear-resistant alloy and production process, which is applied in the field of high-strength wear-resistant alloy brush wire and its production process, can solve the problems of low strength, high wear rate, affecting the service life and reliability of engine brush seals, and achieve good resistance High temperature wear resistance, improved service life and reliability, and controllable production process
- Summary
- Abstract
- Description
- Claims
- Application Information
AI Technical Summary
Problems solved by technology
Method used
Examples
Embodiment 1
[0016] Example 1 A high-strength wear-resistant alloy brush filament, which is composed of the following raw materials in mass percentage: chromium 12%, manganese 8%, molybdenum 1.8%, cobalt 6%, iron 2%, titanium 0.2%, aluminum 0.6%, carbon 0.05%, polyethylene resin 40%, PBT resin 30%, aminopropyltriethoxysilane 2%, aminopropyltrimethylaminosilane 2%, antiwear agent 0.05%, antiaging agent 0.05%, 1% temperature resistant agent, 0.05% plasticizer, 0.05% acetone, 10% diamond.
[0017] A high-strength wear-resistant alloy brush wire and its production process, comprising the following steps:
[0018] (1) Weighing the raw materials in the mass percentage and melting them in a vacuum melting furnace at a melting temperature of 1400-1680° C., casting them into alloy steel;
[0019] (2) performing homogenization annealing treatment on the alloy steel obtained above, the homogenization annealing temperature is 1200-1450°C, the time is 24-30h, and then forging and rolling are carried o...
Embodiment 2
[0025] Example 2 A high-strength wear-resistant alloy brush filament, which is composed of the following raw materials in mass percentage: 20% chromium, 10% manganese, 3.2% molybdenum, 9% cobalt, 4% iron, 0.8% titanium, aluminum 1.2%, carbon 0.1%, polyethylene resin 55%, PBT resin 35%, aminopropyltriethoxysilane 5%, aminopropyltrimethylaminosilane 5%, anti-wear agent 1%, anti-aging agent 1%, 2% temperature resistant agent, 1% plasticizer, 1% acetone, 10-15% diamond.
[0026] A high-strength wear-resistant alloy brush wire and its production process, comprising the following steps:
[0027] (1) Weighing the raw materials in the mass percentage and melting them in a vacuum melting furnace at a melting temperature of 1400-1680° C., casting them into alloy steel;
[0028] (2) performing homogenization annealing treatment on the alloy steel obtained above, the homogenization annealing temperature is 1200-1450°C, the time is 24-30h, and then forging and rolling are carried out to p...
Embodiment 3
[0034] Example 3 A high-strength wear-resistant alloy brush filament, which is composed of the following raw materials in mass percentage: chromium 16%, manganese 9%, molybdenum 2.5%, cobalt 8%, iron 3%, titanium 0.6%, aluminum 0.9%, carbon 0.08%, polyethylene resin 48%, PBT resin 32%, aminopropyltriethoxysilane 4%, aminopropyltrimethylaminosilane 3%, antiwear agent 0.08%, antiaging agent 0.08%, Temperature resistant agent 1.5%, plasticizer 0.09%, acetone 0.06%, diamond 12%.
[0035] A high-strength wear-resistant alloy brush wire and its production process, comprising the following steps:
[0036] (1) Weighing the raw materials in the mass percentage and melting them in a vacuum melting furnace at a melting temperature of 1400-1680° C., casting them into alloy steel;
[0037] (2) performing homogenization annealing treatment on the alloy steel obtained above, the homogenization annealing temperature is 1200-1450°C, the time is 24-30h, and then forging and rolling are carried...
PUM
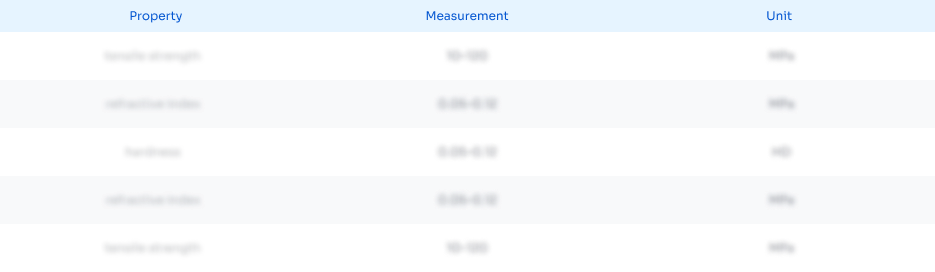
Abstract
Description
Claims
Application Information

- Generate Ideas
- Intellectual Property
- Life Sciences
- Materials
- Tech Scout
- Unparalleled Data Quality
- Higher Quality Content
- 60% Fewer Hallucinations
Browse by: Latest US Patents, China's latest patents, Technical Efficacy Thesaurus, Application Domain, Technology Topic, Popular Technical Reports.
© 2025 PatSnap. All rights reserved.Legal|Privacy policy|Modern Slavery Act Transparency Statement|Sitemap|About US| Contact US: help@patsnap.com