Optical source assembly structure of flip LED chip integrated package and manufacturing method thereof
A technology of LED chips and light source components, applied in the field of LED light sources, can solve the problems of reduced contact fastness and reliability of chip electrodes, chip displacement, and smaller heat dissipation channel area of the chip, etc., so as to ensure the photoelectric characteristics and reliability, Improve production capacity and shipment rate, maximize the effect of heat dissipation area
- Summary
- Abstract
- Description
- Claims
- Application Information
AI Technical Summary
Problems solved by technology
Method used
Image
Examples
Embodiment 1
[0047] Such as Figure 2A and Figure 2B As shown, it is a top view and a side view of the light source assembly structure of the flip-chip LED chip integrated package of the present invention, see figure 1 , the manufacturing method of the light source assembly structure described in the present embodiment, comprises the following steps:
[0048] Step 101. Arrange flip-chip LED chips on the sticky flexible transition base film that can withstand a temperature greater than 150° and is not deformed when baked according to the pre-designed chip spacing requirements;
[0049] Step 102, sticking the P and N electrode surfaces of the flip-chip LED chip on the adhesive side of the flexible transition base film to form a flip-chip LED chip array;
[0050] Step 103, coating a certain thickness of uniform encapsulation glue on the flexible transition base film, and curing the encapsulation glue;
[0051] Specifically, by attaching a dam 40 of a certain height around the flip-chip LE...
Embodiment 2
[0066] Such as Figure 2A , Figure 2B As shown, it is a top view and a side view of the light source assembly structure of the flip-chip LED chip integrated package of the present invention. The carrier substrate 61 after permanent interconnection and integration, and the unit cell of the light source module after the second printing of heat-conducting insulating glue;
[0067] Flip-chip LED chips 10, encapsulation glue carrier substrates of flip-chip LED chip arrays, carrier substrates after electrical interconnection integration, and light source component cells after secondary printing of heat-conducting insulating glue; wherein,
[0068] The encapsulation adhesive carrier substrate of the flip-chip LED chip array is on a flexible transition base film with a viscosity that can withstand a temperature greater than 150° and is not deformed when baked, and is flip-chip arranged regularly according to the pre-designed chip spacing requirements. LED chips; paste the P electro...
Embodiment 3
[0075] The following provides an application example of the manufacturing method of the light source component structure of the flip-chip LED chip integrated package of the present invention, see image 3 ,include:
[0076] Step 201. Arrange a plurality of flip-chip LED chips 10 on the flexible transition base film (conversion base film) 20 according to the designed chip spacing requirements, and paste the P electrodes 31 and N electrodes 32 of the flip-chip LED chips 10 on the flexible transition base film (conversion base film) 20. One side of the adhesive surface of the transition base film 20 forms an array of flip-chip LED chips, see Figure 4 .
[0077]Wherein, the flip-chip LED chip 10 is a chip sorted according to the excitation wavelength of the phosphor powder. The flip-chip LED chips are arranged equidistantly on the flexible transition base film 20 according to the design requirements, and the electrode surface of the flip-chip LED chip 10 is adhered to the flexi...
PUM
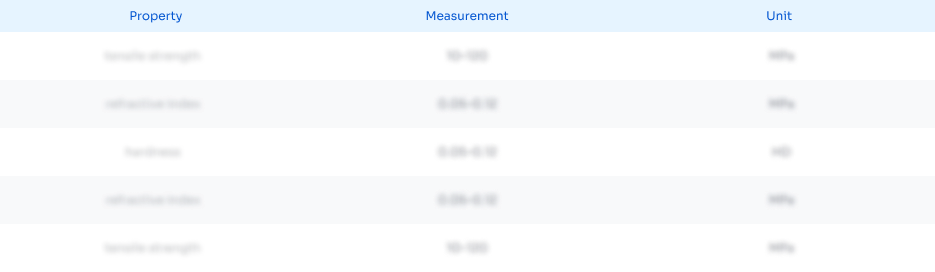
Abstract
Description
Claims
Application Information

- R&D Engineer
- R&D Manager
- IP Professional
- Industry Leading Data Capabilities
- Powerful AI technology
- Patent DNA Extraction
Browse by: Latest US Patents, China's latest patents, Technical Efficacy Thesaurus, Application Domain, Technology Topic, Popular Technical Reports.
© 2024 PatSnap. All rights reserved.Legal|Privacy policy|Modern Slavery Act Transparency Statement|Sitemap|About US| Contact US: help@patsnap.com