Resource utilization method of paint slag
A recycling and paint slag technology, applied in the field of resource utilization of paint waste, can solve problems affecting kiln working conditions, high energy consumption, secondary pollution, etc., and achieve low disposal or utilization costs, simple process methods, and no secondary pollution The effect of secondary pollution
- Summary
- Abstract
- Description
- Claims
- Application Information
AI Technical Summary
Problems solved by technology
Method used
Examples
Embodiment 1
[0045] The mixed paint residue from an automobile factory was selected for the test, with a moisture content of 82.1wt%. The wet paint slag is converted into recyclable solid raw materials and a liquid coal clean combustion accelerator for energy saving and emission reduction according to the following steps:
[0046] (1) Pretreatment and separation: Grind wet state (flocculation) paint slag into 180-mesh slurry, use medium-temperature (150°C) dry gas as the medium, and spray-dry the 180-mesh slurry directly to obtain powdery slag , Recover all the water-containing volatile organic matter waste liquid to obtain water-containing organic matter waste liquid (water content 87.9%).
[0047] The obtained powdery slag, one of the two major components, has the potential of cementing and hardening, and can be directly recycled as a raw material: the powder is pressed into a vase shape at 30 MPa and then cured at 180°C to obtain a "porcelain" vase.
[0048] (2) Preparation of liquid c...
Embodiment 2
[0055] The mixed paint residue from an automobile painting workshop was selected for the test, with a moisture content of 84.1wt%. The wet paint slag is converted into recyclable solid raw materials and a liquid coal clean combustion accelerator for energy saving and emission reduction according to the following steps:
[0056] (1) Pretreatment and separation: Grind the wet state (flocculation) paint slag into a 200-mesh slurry, and use a medium-temperature (160°C) dry gas as a medium to directly spray dry the 200-mesh slurry to obtain powdery slag , Recover all the water-containing volatile organic matter waste liquid to obtain water-containing organic matter waste liquid (water content 86.3%).
[0057] The powdery slag of one of the two major components obtained has potential cementation and hardening ability, and is directly recycled as raw material: the powder is ground according to a known method for preparing a primer, adding solvent and acrylic resin, etc., to obtain a ...
Embodiment 3
[0064] The water-based paint residue from an automobile painting workshop was selected for the test, with a moisture content of 78.9wt%. The wet paint slag is converted into recyclable solid raw materials and a liquid coal clean combustion accelerator for energy saving and emission reduction according to the following steps:
[0065] (1) Pretreatment and separation: Grind the paint slag in the wet state (flocculation) into a 300-mesh slurry, and use a medium-temperature (150°C) dry gas as a medium to directly spray dry the 300-mesh slurry to obtain powdery slag. Recover all the water-containing volatile organic matter waste liquid to obtain water-containing organic matter waste liquid (water content 81.9%).
[0066] The obtained powdery slag, one of the two major components, has the potential of cementing and hardening, and can be directly recycled as raw materials: the powder is pressed at 30MPa into a board and then cured at 180°C to obtain a "porcelain" board.
[0067] (2)...
PUM
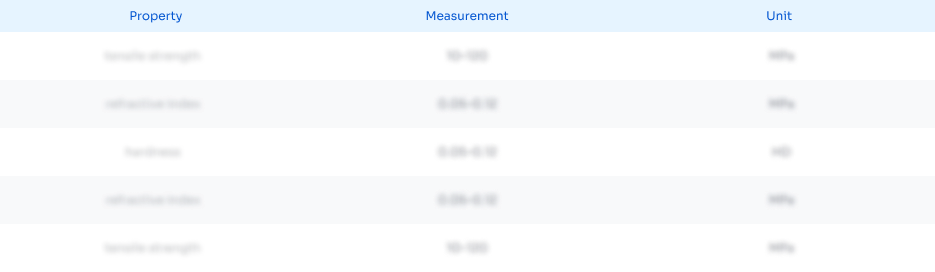
Abstract
Description
Claims
Application Information

- R&D
- Intellectual Property
- Life Sciences
- Materials
- Tech Scout
- Unparalleled Data Quality
- Higher Quality Content
- 60% Fewer Hallucinations
Browse by: Latest US Patents, China's latest patents, Technical Efficacy Thesaurus, Application Domain, Technology Topic, Popular Technical Reports.
© 2025 PatSnap. All rights reserved.Legal|Privacy policy|Modern Slavery Act Transparency Statement|Sitemap|About US| Contact US: help@patsnap.com