A system for treating wolframite with sulfuric acid to prepare tungstate solution
A technology of sulfuric acid solution and wolframite, which is applied in the field of tungsten smelting, can solve the problems of less processing research, high equipment requirements, corrosion, etc., and achieve the effects of simple equipment, reduced energy consumption, and reduced consumption
- Summary
- Abstract
- Description
- Claims
- Application Information
AI Technical Summary
Problems solved by technology
Method used
Image
Examples
Embodiment 1
[0070] A wolframite (WO 3 The mass percent content is 56%), wolframite and water 1:1 are wet-milled in a vibrating mill for 10 minutes, and the particle size is 4 .
[0071] Prepare the ammonium carbonate solution with a final theoretical excess of 100g / L containing 5% NH 3 ·H 2 O, add the above transformation material into the solution, the liquid-solid ratio is 3:1, the temperature is 30°C, react for 2 hours, filter to obtain ammonium tungstate solution, and the tungsten content in the filter residue is <1%.
Embodiment 2
[0073] A wolframite (WO 3 The mass percent content is 56%), wolframite and water 1:1 are wet-milled in a vibrating mill for 10 minutes, and the particle size is 4 .
[0074] Prepare a theoretical concentration of sodium carbonate solution, add the above transformation materials into the solution, the liquid-solid ratio is 3:1, the temperature is 30°C, react for 2 hours, filter to obtain sodium tungstate solution, and the tungsten content in the filter residue is <3%.
Embodiment 3
[0076] A wolframite (WO 3 The mass percent content is 56%), wolframite and water 1:1 were wet-milled in a vibrating mill for 20 minutes, and the particle size was 4 .
[0077] Prepare the final ammonium carbonate solution with a theoretical excess of 150g / L containing 5% NH 3 ·H 2 O, add the above transformation material into the solution, the liquid-solid ratio is 3:1, the temperature is 25°C, react for 1h, and filter to obtain ammonium tungstate solution, the tungsten content in the filter residue is <1%.
PUM
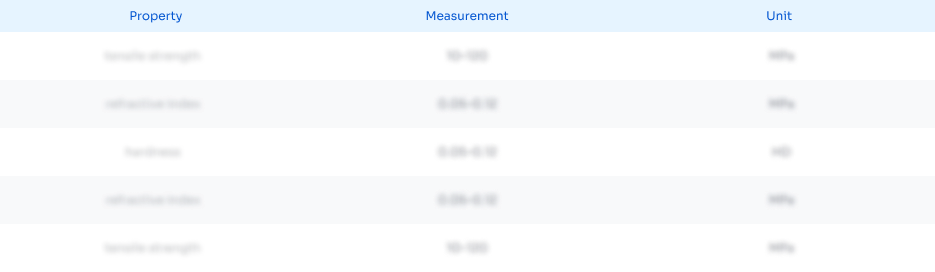
Abstract
Description
Claims
Application Information

- R&D Engineer
- R&D Manager
- IP Professional
- Industry Leading Data Capabilities
- Powerful AI technology
- Patent DNA Extraction
Browse by: Latest US Patents, China's latest patents, Technical Efficacy Thesaurus, Application Domain, Technology Topic, Popular Technical Reports.
© 2024 PatSnap. All rights reserved.Legal|Privacy policy|Modern Slavery Act Transparency Statement|Sitemap|About US| Contact US: help@patsnap.com