A kind of disperse/reactive homogeneous printing dye and its printing process
A printing process and reactive dye technology, applied in the field of textile printing and dyeing, can solve the problems of poor compatibility, low color yield of reactive and disperse dyes, etc., and achieve the effect of bright color, stable product quality, and promoting dye fixation.
- Summary
- Abstract
- Description
- Claims
- Application Information
AI Technical Summary
Problems solved by technology
Method used
Examples
Embodiment 1
[0021] Polyester cotton blended (T / C=65:35) woven bleached fabric
[0022] The composition formula of the compound paste slurry: sodium alginate, sodium polyacrylate, polyethylene glycol 2000, polyvinylpyrrolidone, the ratio is 60%:20%:15%:5%.
[0023] Preparation of compound paste slurry: Mix the raw materials according to the required ratio, slowly add to warm water (50-60°C) while stirring, and stir with a mechanical stirrer for about 3-4 hours to fully expand the paste to Until it becomes uniform and transparent, let it stand overnight to make the paste fully expand, and let it stand still to get the compound paste slurry, which is formulated into a 7% compound paste slurry solution according to the formula.
[0024] same paste printing formula
[0025] Compound paste slurry solution (containing 7% compound paste paste) 50%
[0026] Urea 5%
[0027] Sodium bicarbonate 1.5%
[0028] Anti-stain salt 1%
[0029] Reactive dye M-3R 2.5%
[0030] Reactive dye M-3BE 3.0%
...
Embodiment 2
[0038] Polyester cotton blended (T / C=65:35) woven bleached fabric
[0039] Composite paste composition formula: sodium alginate, sodium polyacrylate, polyethylene glycol 2000, polyvinylpyrrolidone, the ratio is 60%:25%:10%:5%.
[0040] Preparation of compound paste slurry: Mix the raw materials according to the required ratio, slowly add to warm water (50-60°C) while stirring, and stir with a mechanical stirrer for about 3-4 hours to fully expand the paste to Until it becomes uniform and transparent, let it stand overnight to make the paste fully expand, and let it stand still to get the compound paste slurry, which is formulated into a 7% compound paste slurry solution according to the formula.
[0041] same paste printing formula
[0042] Compound paste slurry solution (containing 7% compound paste paste) 50%
[0043] Urea 5%
[0044] Sodium bicarbonate 1.5%
[0045] Anti-stain salt 1%
[0046] Reactive dye M-3R 2.5%
[0047] Reactive dye M-3BE 3.0%
[0048] Reactive ...
Embodiment 3
[0055] Polyester cotton blended (T / C=65:35) woven bleached fabric
[0056] The compound paste composition formula: sodium alginate, sodium polyacrylate, polyethylene glycol 2000, polyvinylpyrrolidone, the ratio is 60%:30%:5%:5%.
[0057]Preparation of compound paste slurry: Mix the raw materials according to the required ratio, slowly add to warm water (50-60°C) while stirring, and stir with a mechanical stirrer for about 3-4 hours to fully expand the paste to Until it becomes uniform and transparent, let it stand overnight to make the paste fully expand, and let it stand still to get the compound paste slurry, which is formulated into a 7% compound paste slurry solution according to the formula.
[0058] same paste printing formula
[0059] Compound paste slurry solution (containing 7% compound paste paste) 50%
[0060] Urea 5%
[0061] Sodium bicarbonate 1.5%
[0062] Anti-stain salt 1%
[0063] Reactive dye M-3R 2.5%
[0064] Reactive dye M-3BE 3.0%
[0065] Reactive...
PUM
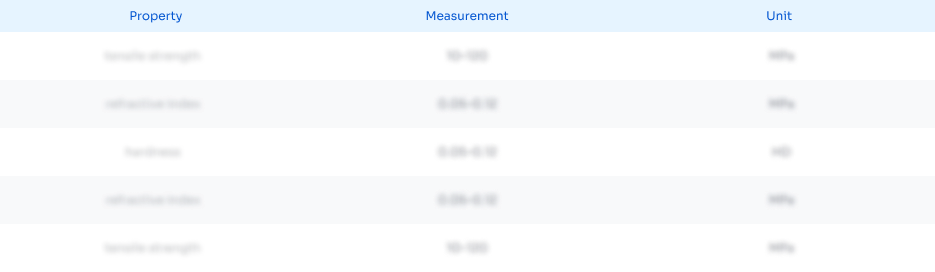
Abstract
Description
Claims
Application Information

- Generate Ideas
- Intellectual Property
- Life Sciences
- Materials
- Tech Scout
- Unparalleled Data Quality
- Higher Quality Content
- 60% Fewer Hallucinations
Browse by: Latest US Patents, China's latest patents, Technical Efficacy Thesaurus, Application Domain, Technology Topic, Popular Technical Reports.
© 2025 PatSnap. All rights reserved.Legal|Privacy policy|Modern Slavery Act Transparency Statement|Sitemap|About US| Contact US: help@patsnap.com