A wear-resistant roller sleeve of trapezoidal bainite-martensitic composite phase steel and its preparation method
A technology of bainite and multiphase steel, which is applied in the field of wear-resistant roller sleeves of trapezoidal bainite-martensitic multiphase steel and its preparation, can solve the problem of shedding of strengthening layers, increase the production cost of composite roller sleeves, and improve the alloying elements. High content and other problems, to avoid defects such as cracks, ensure service reliability, and simple heat treatment process
- Summary
- Abstract
- Description
- Claims
- Application Information
AI Technical Summary
Problems solved by technology
Method used
Image
Examples
Embodiment 1
[0023] This embodiment prepares 3 tons of bainite-martensite composite phase steel centrifugal composite grinding roll sleeve, the outer wall thickness is 100mm, and the inner wall thickness is 200mm; the chemical composition mass percentage table of the inner and outer two layers of materials 1 shows:
[0024] Table 1
[0025]
[0026] The preparation method of the bainite-martensite complex phase steel centrifugal composite grinding roller sleeve described in this embodiment specifically includes the following steps:
[0027] (1) Batching: Batching is carried out according to the composition of the outer layer and the inner layer, and the intermediate frequency induction furnace is used for melting respectively.
[0028] (2) Centrifugal casting forming: First, the outer layer of molten steel is poured into the high-speed rotating casting metal mold (the temperature of the outer layer of molten steel is 1550°C, and the pouring temperature is 1470°C), and the outer layer o...
Embodiment 2
[0033] This embodiment prepares 5 tons of bainite-martensite composite phase steel centrifugal composite grinding roller sleeve, the outer wall thickness is 100mm, and the inner wall thickness is 300mm; the chemical composition mass percentage table of the inner and outer two layers of materials 2 shows:
[0034] Table 2
[0035]
[0036] The preparation method of the bainite-martensite complex phase steel centrifugal composite grinding roller sleeve described in this embodiment specifically includes the following steps:
[0037] (1) Batching: Batching is carried out according to the composition of the outer layer and the inner layer, and is smelted separately in an intermediate frequency induction furnace;
[0038] (2) Centrifugal casting forming: first pour the outer layer of molten steel into the high-speed rotating casting metal mold (the temperature of the outer layer of molten steel is 1560°C, and the pouring temperature is 1500°C), and under the action of centrifuga...
Embodiment 3
[0043] This embodiment prepares 3 tons of bainite-martensite composite phase steel centrifugal composite grinding roll sleeve, the outer wall thickness is 100mm, and the inner wall thickness is 150mm; the chemical composition mass percentage table of the inner and outer two layers of materials 3 shows:
[0044] table 3
[0045]
[0046] The preparation method of the bainite-martensite complex phase steel centrifugal composite grinding roller sleeve described in this embodiment specifically includes the following steps:
[0047] (1) Batching: Batching is carried out according to the composition of the outer layer and the inner layer, and the intermediate frequency induction furnace is used for melting respectively.
[0048] (2) Centrifugal casting forming: first pour the outer layer of molten steel into the high-speed rotating casting metal mold (the temperature of the outer layer of molten steel is 1580°C, and the pouring temperature is 1530°C), and under the action of cen...
PUM
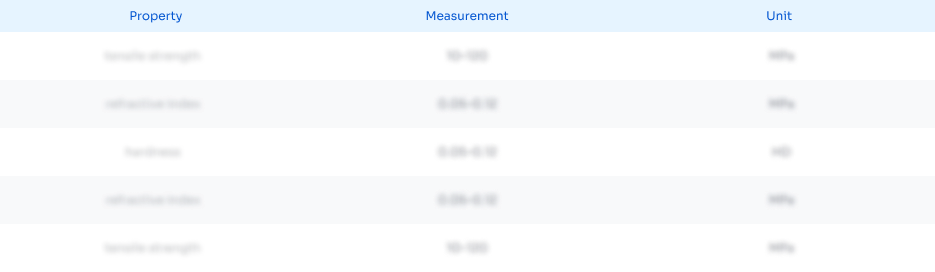
Abstract
Description
Claims
Application Information

- Generate Ideas
- Intellectual Property
- Life Sciences
- Materials
- Tech Scout
- Unparalleled Data Quality
- Higher Quality Content
- 60% Fewer Hallucinations
Browse by: Latest US Patents, China's latest patents, Technical Efficacy Thesaurus, Application Domain, Technology Topic, Popular Technical Reports.
© 2025 PatSnap. All rights reserved.Legal|Privacy policy|Modern Slavery Act Transparency Statement|Sitemap|About US| Contact US: help@patsnap.com